Pulse metallic polypropylene film capacitor
A technology of polypropylene film and polypropylene film, which is applied in the direction of film/thick film capacitors, capacitors, laminated capacitors, etc., can solve the problem of lack of anti-oxidation, anti-aging air absorption and water absorption performance, limited discharge current impact ability, and heavy Problems such as the operation of the lower capacitor, to achieve the effects of small loss, improved explosion-proof performance, and low square resistance
- Summary
- Abstract
- Description
- Claims
- Application Information
AI Technical Summary
Problems solved by technology
Method used
Image
Examples
Embodiment 1
[0024] Such as figure 1 with 2 As shown, a pulse metallized polypropylene film capacitor includes a metal cylinder, a capacitor core 3, a gold spray layer 4, an upper insulating cover 1 and a lower insulating cover 2. The capacitor core 3 is arranged in the metal cylinder, and the capacitor core 3 The top and bottom ends are provided with a gold-sprayed layer 4, the polypropylene film 10 is electrically connected to the gold-sprayed layer 4, and the polypropylene film 10 and the gold-sprayed layer 4 have an equipotential, so as to ensure that the capacitor forms a current path for normal operation.
[0025] The upper insulating cover 1 and the lower insulating cover 2 are fixedly connected by the explosion-proof plate 5. The plastic shell cover and the upper insulating cover 1 used by the capacitor can be integrally molded with high insulation strength, safety and reliability. The upper insulating cover 1 and the lower insulating cover 2 The surface is treated with sandblasting an...
Embodiment 2
[0035] The structure of Example 2 is roughly the same as that of Example 1, except that:
[0036] Among them, the impregnant 9 is made of the following parts by weight: 70 parts of polyisobutylene with a molecular weight of 500-1000 and a terminal α-olefin structure content of 75% to 80%, 4 parts of butylated hydroxytoluene, and 1.5 parts of refined rapeseed oil Parts, 3 parts of diatomaceous earth, 1.4 parts of auxiliary agents, 1.2 parts of tricresol phosphate, 0.3 parts of silane coupling agent.
[0037] The additives include carbon black and calcium silicate, and the weight ratio of carbon black and calcium silicate is 1:3.
[0038] The preparation method of the impregnant includes the following steps:
[0039] 1) Dissolve tricresol phosphate and silane coupling agent in refined rapeseed oil, sonicate at 650W for 40 minutes, then add butylated hydroxytoluene and diatomaceous earth, stir in a high-speed disperser at 650 rpm for 2 hours to obtain a mixed group Minute;
[0040] 2) Mi...
Embodiment 3
[0043] The structure of Example 3 is roughly the same as that of Example 1, except that:
[0044] Among them, the impregnant 9 is made of the following parts by weight: 65 parts of polyisobutylene with a molecular weight of 500-1000 and a terminal α-olefin structure content of 75% to 80%, 2 parts of butylated hydroxytoluene, and 1.5 parts of refined rapeseed oil Parts, 2 parts diatomaceous earth, 1.2 parts auxiliary agent, 0.8 parts tricresol phosphate, 0.2 parts silane coupling agent.
[0045] The additives include carbon black and calcium silicate, and the weight ratio of carbon black and calcium silicate is 1:2.5.
[0046] The preparation method of the impregnant includes the following steps:
[0047] 1) Dissolve tricresol phosphate and silane coupling agent in refined rapeseed oil, supersound at 700W for 40 minutes, then add butylated hydroxytoluene and diatomaceous earth, and stir in a high-speed disperser at 650 rpm for 1.5 hours to obtain a mixed group Minute;
[0048] 2) The m...
PUM
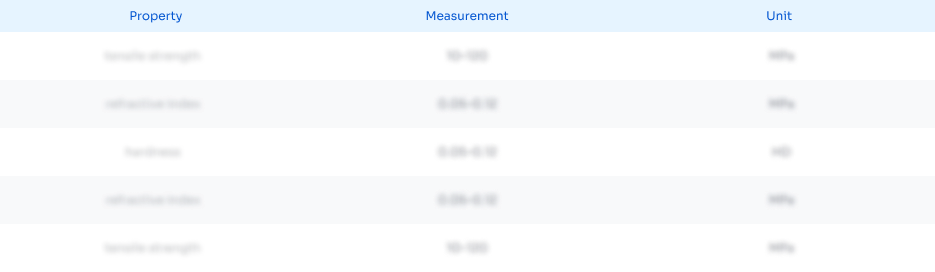
Abstract
Description
Claims
Application Information

- R&D
- Intellectual Property
- Life Sciences
- Materials
- Tech Scout
- Unparalleled Data Quality
- Higher Quality Content
- 60% Fewer Hallucinations
Browse by: Latest US Patents, China's latest patents, Technical Efficacy Thesaurus, Application Domain, Technology Topic, Popular Technical Reports.
© 2025 PatSnap. All rights reserved.Legal|Privacy policy|Modern Slavery Act Transparency Statement|Sitemap|About US| Contact US: help@patsnap.com