A method of ion implanting rare earth and alloy to improve the performance of sintered NdFeB magnet
A technology of ion implantation and neodymium iron boron, which is applied in the direction of magnetic materials, magnetic objects, and the magnetism of inorganic materials, can solve the problems of low actual utilization rate of diffusion sources, residues, and many diffusion sources, etc., to increase the depth of ion implantation and shorten the Diffusion path, effect of improving diffusion efficiency
- Summary
- Abstract
- Description
- Claims
- Application Information
AI Technical Summary
Problems solved by technology
Method used
Examples
Embodiment 1
[0015] 1) Change the alloy composition to Pr 7.03 Nd 21.84 Fe bal Cu 0.2 Ga 0.1 B 0.98 (mass fraction) NdFeB oriented green compacts are pre-fired in vacuum with a density of 95% and a size of The pre-sintered green body, numbered 1#;
[0016] 2) Put the pre-sintered compact into the ion implantation device, inject the heavy rare earth element Dy into the pre-sintered compact in the form of high-energy ions, the implantation energy is 200keV, and the implantation metering is 4×10 17 cm -2 , the obtained sample number is 2#;
[0017] 3) The samples numbered 1# and 2# were further sintered and densified and the grain boundaries diffused, the temperature was 950 ° C, the time was 1 h, the pressure was 2 MPa (provided by argon), and the vacuum degree before filling with argon was 3×10 -3 Pa;
[0018] 4) The 1# and 2# samples that have undergone sintering densification and grain boundary diffusion are subjected to vacuum tempering heat treatment, and the process parameter...
Embodiment 2
[0023] 1) Change the alloy composition to Pr 7.03 Nd 21.84 Fe bal Cu 0.2 Ga 0.1 B 0.98 (mass fraction) NdFeB oriented green compacts are pre-fired in vacuum with a density of 98% and a size of The pre-sintered green body, numbered 3#;
[0024] 2) Put the pre-sintered compact into the ion implantation device, and inject the rare earth alloy Dy in the form of high-energy ions 70 Cu 30 (Atomic fraction) injected into the calcined billet, the injection energy is 200keV, and the injection metering is 2×10 17 cm -2 , the obtained sample number is 4#;
[0025] 3) The samples numbered 3# and 4# were sintered and densified and the grain boundaries diffused, the temperature was 950°C, the time was 1h, the pressure was 0.2MPa (provided by argon), and the vacuum degree before filling with argon was 3×10 -3 Pa;
[0026] 4) The samples numbered 3# and 4# after the grain boundary diffusion treatment were subjected to vacuum tempering heat treatment, and the process parameters wer...
Embodiment 3
[0031] 1) Change the alloy composition to Pr 9.8 Nd 20.2 Fe bal al 0.15 Cu 0.2 Ga 0.1 B 0.98 (Mass fraction) Vacuum pre-fired density is 92%, size is pre-sintered compact, numbered 5#;
[0032] 2) Put the pre-sintered compact into the ion implantation device, and inject the rare earth alloy Pr in the form of high-energy ions 35 Dy 35 Cu 30 (Atomic fraction) into the pre-sintered compact, the injection energy is 300keV, and the injection metering is 6×10 17 cm -2 , the number is 6#;
[0033] 3) The samples numbered 5# and 6# were further sintered and densified and the grain boundaries diffused, the temperature was 920 ° C, the time was 1 h, the pressure was 3 MPa (provided by argon), and the vacuum degree before filling with argon was 3×10 -3 Pa;
[0034] 4) The samples numbered 5# and 6# that have undergone sintering densification and grain boundary diffusion treatment are subjected to vacuum tempering heat treatment, and the process parameters are: temperature 5...
PUM
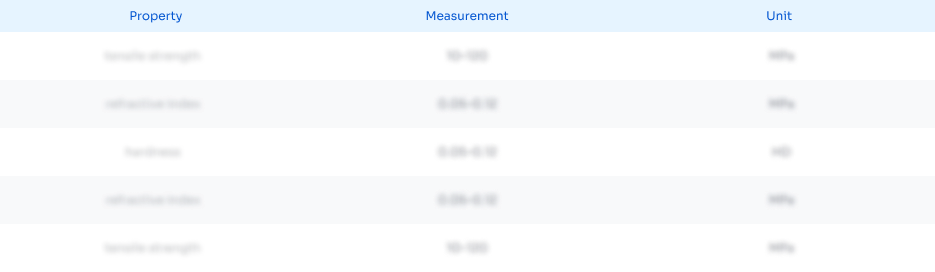
Abstract
Description
Claims
Application Information

- R&D
- Intellectual Property
- Life Sciences
- Materials
- Tech Scout
- Unparalleled Data Quality
- Higher Quality Content
- 60% Fewer Hallucinations
Browse by: Latest US Patents, China's latest patents, Technical Efficacy Thesaurus, Application Domain, Technology Topic, Popular Technical Reports.
© 2025 PatSnap. All rights reserved.Legal|Privacy policy|Modern Slavery Act Transparency Statement|Sitemap|About US| Contact US: help@patsnap.com