Barium magnesium niobate light-emitting ceramics and preparation method thereof
A technology of luminescent ceramics and barium magnesium niobate, applied in the field of luminescent materials, can solve the problems of low luminous efficiency and low quenching concentration, and achieve the effects of high luminous intensity, good density and high chemical stability
- Summary
- Abstract
- Description
- Claims
- Application Information
AI Technical Summary
Problems solved by technology
Method used
Image
Examples
Embodiment 1
[0030] 1) The analytically pure BaCO 3 , Nb 2 o 5 , 99.99% high-purity Sm 2 o 3 , MgO, SnO2 According to the molar ratio of 0.98:0.3:0.1:0.3:0.1, add ethanol and ball mill for 24 hours, then ignite at 1350°C to obtain the product obtained by ball milling for 12 hours for the second time, and then make Ba with 200 sieves. 0.98 SM 0.02 (Sn 0.1 Mg 0.3 Nb 0.6 )O 3 Ceramic powder.
[0031] 2) Add 5% polyvinyl alcohol aqueous solution (mass volume concentration: 1:20g / ml) to granulate the ceramic powder, stale for 24 hours, and crush the ceramic particles to pass through a 40 mesh sieve, then use the ceramic particles A dry-pressed tablet press was pressed into a ceramic green body under a pressure of 2 MPa, and then pressed under a cold isostatic pressure of 200 MPa for 10 minutes to make a uniformly pressed green body.
[0032] 3) After debinding the equalized green body at 600°C, carry out atmosphere sintering under an oxygen atmosphere. After fine polishing of chromiu...
Embodiment 2
[0034] 1) The analytically pure BaCO 3 , Nb 2 o 5 , 99.99% high-purity Sm 2 o 3 , MgO, SnO 2 According to the molar ratio of 0.995: 0.3: 0.0025: 0.3: 0.1, add ethanol and ball mill for 24 hours, then burn the product at 1300 ° C for 12 hours to make Ba 0.995 SM 0.005 (Sn 0.1 Mg 0.3 Nb 0.6 )O 3 Ceramic powder.
[0035] 2) Add 5% polyvinyl alcohol aqueous solution to the ceramic powder and granulate it, stale for 24 hours, break it into ceramic particles passing through a 40-mesh sieve, and then compress the ceramic particles under a pressure of 2 MPa with a dry tablet press into a ceramic green body, and then pressurized for 10 minutes under a cold isostatic pressure of 200 MPa to make a uniformly pressed green body.
[0036] 3) After debinding the equalized green body at 600°C, carry out atmosphere sintering under an oxygen atmosphere, the sintering temperature is 1575°C, keep warm for 60h, then cool with the furnace, rough sandpaper with 40 mesh and 200 mesh, and o...
Embodiment 3
[0038] 1) The analytically pure BaCO 3 , Nb 2 o 5 , 99.99% high-purity Sm 2 o 3 , MgO, SnO 2 According to the molar ratio of 0.985: 0.3: 0.0075: 0.3: 0.1, add ethanol and ball mill for 24 hours, then burn the product at 1300 ° C for 12 hours to make Ba 0.985 SM 0.015 (Sn 0.1 Mg 0.3 Nb 0.6 )O 3 Ceramic powder.
[0039] 2) Add 5% polyvinyl alcohol aqueous solution to the ceramic powder and granulate it, stale for 24 hours, break it into ceramic particles passing through a 40-mesh sieve, and then compress the ceramic particles under a pressure of 2 MPa with a dry tablet press into a ceramic green body, and then pressurized for 10 minutes under a cold isostatic pressure of 200 MPa to make a uniformly pressed green body.
[0040] 3) After debinding the equalized green body at 600°C, carry out atmosphere sintering under an oxygen atmosphere, the sintering temperature is 1575°C, keep warm for 60h, then cool with the furnace, rough sandpaper with 40 mesh and 200 mesh, and o...
PUM
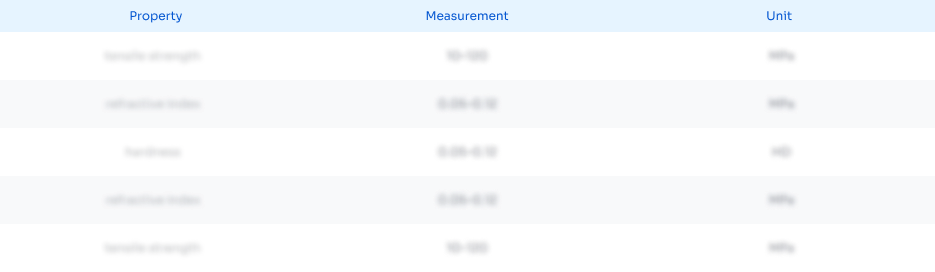
Abstract
Description
Claims
Application Information

- R&D
- Intellectual Property
- Life Sciences
- Materials
- Tech Scout
- Unparalleled Data Quality
- Higher Quality Content
- 60% Fewer Hallucinations
Browse by: Latest US Patents, China's latest patents, Technical Efficacy Thesaurus, Application Domain, Technology Topic, Popular Technical Reports.
© 2025 PatSnap. All rights reserved.Legal|Privacy policy|Modern Slavery Act Transparency Statement|Sitemap|About US| Contact US: help@patsnap.com