Position sensor-free permanent magnet synchronous motor starting method
A technology of permanent magnet synchronous motor and starting method, which is applied to control generator, motor generator control, electronic commutation motor control, etc., can solve the problems of motor out of step, large motor impact, and large influence of motor starting torque.
- Summary
- Abstract
- Description
- Claims
- Application Information
AI Technical Summary
Problems solved by technology
Method used
Image
Examples
Embodiment
[0062] Such as figure 1 Shown is the block diagram of the optimized "three-stage" starting method of the present invention, and the implementation of the optimized "three-stage" starting method comprises the following steps:
[0063] First, when the motor starts, a two-step current injection method based on a current closed loop is used. Among them, the system block diagram of current closed-loop pre-positioning is as follows: figure 2 As shown; the block diagram is composed of d / q axis current regulator, Park transform and its inverse transform, Clarke transform, SVPWM modulation module, three-phase inverter, permanent magnet synchronous motor.
[0064] According to a specific example of the present invention, such as figure 2 As shown, the permanent magnet synchronous motor is an air conditioner compressor, which is controlled by an IPM module and modulated by a seven-stage SVPWM.
[0065] in, is the estimated decoupling angle.
[0066] The specific process of the tw...
PUM
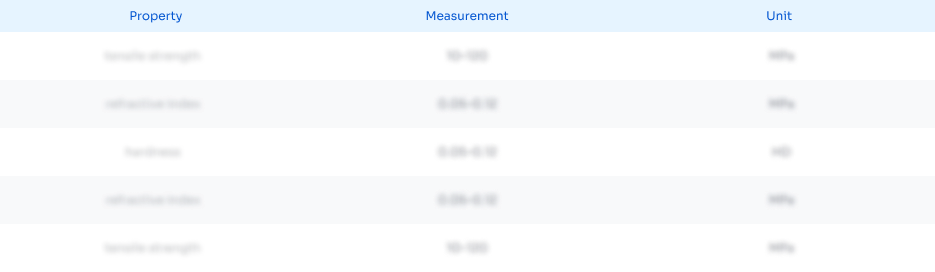
Abstract
Description
Claims
Application Information

- R&D
- Intellectual Property
- Life Sciences
- Materials
- Tech Scout
- Unparalleled Data Quality
- Higher Quality Content
- 60% Fewer Hallucinations
Browse by: Latest US Patents, China's latest patents, Technical Efficacy Thesaurus, Application Domain, Technology Topic, Popular Technical Reports.
© 2025 PatSnap. All rights reserved.Legal|Privacy policy|Modern Slavery Act Transparency Statement|Sitemap|About US| Contact US: help@patsnap.com