Smelting process for steel for wind power main shaft and steel for wind power main shaft
A wind power main shaft and process technology, applied in the smelting process of wind power main shaft steel and the field of wind power main shaft steel, can solve the problems of inaccurate control of element content, wide fluctuation range of chemical composition, unstable mechanical properties of steel, etc., and achieve excellent quenching The effects of high permeability and impact toughness, narrow fluctuation range, and stable mechanical properties of steel
- Summary
- Abstract
- Description
- Claims
- Application Information
AI Technical Summary
Problems solved by technology
Method used
Examples
Embodiment 1
[0030] Embodiment 1 The smelting process of steel for wind power main shaft, comprising the following steps:
[0031] S1: Put clean steel scrap in an electric arc furnace and heat it to a molten steel temperature of 1580°C, blow oxygen to slag for dephosphorization and decarburization, stir the molten pool to remove gas and inclusions, and then add deoxidizers to deoxidize, ferroalloys and carburizers in sequence to reduce the temperature Tapping is controlled at 1650°C;
[0032] S2: Pour S1 molten steel into the ladle refining furnace, make slag and add SiFe powder to keep the white slag, add alloy to fine-tune the element content in the molten steel, and adjust the weight percentage of aluminum in the molten steel to 0.035%;
[0033] S3: Transfer the molten steel obtained in S2 with a temperature of 1650°C into a ladle refining furnace, keep the Ar pressure at 0.2 Mpa for 15 minutes under a vacuum of 66.7 Pa, and blow argon for 10 minutes at an argon pressure of 0.05 Pa;
...
Embodiment 2
[0044] Embodiment 2 is based on embodiment 1, the difference is:
[0045] S1: Put the clean steel scrap in the electric arc furnace and heat it to the temperature of molten steel above 1590°C, blow oxygen to slag for dephosphorization and decarburization, stir the molten pool to remove gas and inclusions, and then add deoxidizer to deoxidize, ferroalloy and carburizer in turn. The temperature is controlled at 1670°C for tapping;
[0046] S2: Pour S1 molten steel into the ladle refining furnace, make slag and add SiFe powder to keep the white slag, add alloy to fine-tune the element content in the molten steel, and adjust the weight percentage of aluminum in the molten steel to 0.045%;
[0047] S3: transfer the molten steel obtained in S2 with a temperature of 1690°C into a ladle refining furnace, maintain an Ar pressure of 0.4 MPa under a vacuum of 66.7 Pa for 20 min, and blow argon for 15 min under an argon pressure of 0.05 Pa;
[0048] S4: Carry out hanging ladle casting wi...
Embodiment 3
[0056] Embodiment 3 is based on embodiment 1, difference is:
[0057] S1: Put clean steel scrap in an electric arc furnace and heat it to a molten steel temperature of 1585°C, blow oxygen to slag for dephosphorization and decarburization, stir the molten pool to degas and remove inclusions, and then add deoxidizers to deoxidize, iron alloys and carburizers in sequence to reduce the temperature Tapping is controlled at 1660°C;
[0058] S2: Pour S1 molten steel into the ladle refining furnace, make slag and add SiFe powder to keep the white slag, add alloy to fine-tune the element content in the molten steel, and adjust the weight percentage of aluminum in the molten steel to 0.035-0.045%;
[0059] S3: transfer the molten steel obtained in S2 with a temperature of 1670°C into a ladle refining furnace, maintain an Ar pressure of 0.3 MPa under a vacuum of 66.7 Pa for 25 min, and blow argon for 20 min under an argon pressure of 0.05 Pa;
[0060] S4: Carry out hanging ladle casting...
PUM
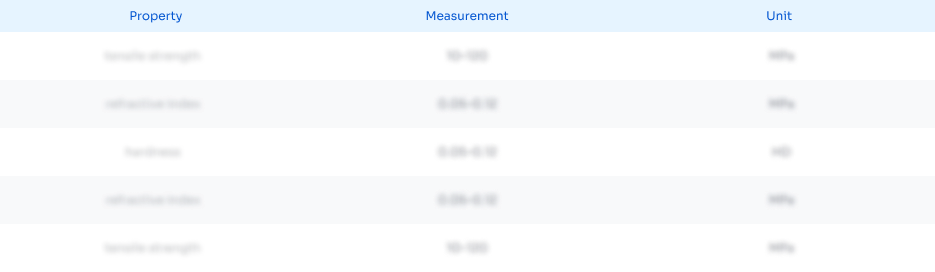
Abstract
Description
Claims
Application Information

- R&D
- Intellectual Property
- Life Sciences
- Materials
- Tech Scout
- Unparalleled Data Quality
- Higher Quality Content
- 60% Fewer Hallucinations
Browse by: Latest US Patents, China's latest patents, Technical Efficacy Thesaurus, Application Domain, Technology Topic, Popular Technical Reports.
© 2025 PatSnap. All rights reserved.Legal|Privacy policy|Modern Slavery Act Transparency Statement|Sitemap|About US| Contact US: help@patsnap.com