Manufacturing method for terminal structure of trench IGBT device
A manufacturing method and terminal structure technology, applied in semiconductor/solid-state device manufacturing, semiconductor devices, electrical components, etc., can solve the difficulty of process control, the limitation of the depth of the charge storage layer and the maximum doping concentration, and the problem of the P well of the charge storage layer influence and other issues, to achieve the effect of reducing the instability of device performance
- Summary
- Abstract
- Description
- Claims
- Application Information
AI Technical Summary
Problems solved by technology
Method used
Image
Examples
Embodiment
[0020] Example: figure 1 As shown, the manufacturing method of the present invention is fully compatible with other trench IGBT devices, and only one step of photolithography process is needed.
[0021] First, an N-type epitaxial layer is grown on a selected N-type epitaxial silicon substrate or a region fuse to form a charge storage layer, and a P-type epitaxial layer is grown on it to form a channel region. Photolithography terminal area trench pattern, dry etching silicon substrate, growing field oxide layer; photolithography active area and etching field oxide layer; photolithography terminal area protection ring, implanting P-type impurities and diffusing to form an effective protective ring. Photoetching the gate trench in the active area, etching the trench and growing a gate oxide layer, depositing in-situ doped polysilicon material to fill the trench; then photoetching the gate pattern and terminal protection field plate, and etching the polysilicon; Photoetching th...
PUM
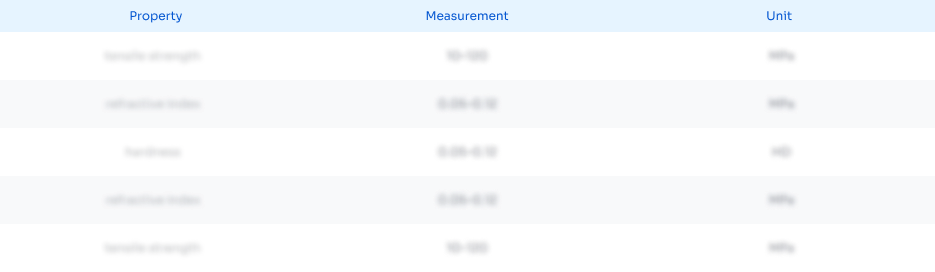
Abstract
Description
Claims
Application Information

- R&D Engineer
- R&D Manager
- IP Professional
- Industry Leading Data Capabilities
- Powerful AI technology
- Patent DNA Extraction
Browse by: Latest US Patents, China's latest patents, Technical Efficacy Thesaurus, Application Domain, Technology Topic, Popular Technical Reports.
© 2024 PatSnap. All rights reserved.Legal|Privacy policy|Modern Slavery Act Transparency Statement|Sitemap|About US| Contact US: help@patsnap.com