Method for recycling rare earth and platinum group metal from spent automobile emission purification catalyst
A technology for purifying catalysts and automobile catalysts, applied in the direction of improving process efficiency, etc., to achieve the effect of simple method, high economic benefit and high dissolution efficiency
- Summary
- Abstract
- Description
- Claims
- Application Information
AI Technical Summary
Problems solved by technology
Method used
Image
Examples
Embodiment 1
[0016] Embodiment 1, see attached figure 1 1. Finely grind the exhausted automobile exhaust purification catalyst to a particle size range of 74-150 μm, mix the finely ground exhausted automobile exhaust catalyst with concentrated acid sulfuric acid at a mass ratio of 1:1, and roast in a muffle furnace at a temperature of 200° C. for 4 hours; The roasted product is leached with 1mol / L sulfuric acid at 80°C for 3 hours, maintaining a liquid-solid ratio of 3, and after filtration and separation, the rare earth solution and insoluble slag containing platinum group metals are obtained; add sodium sulfate to the rare earth solution and react at 80°C After 3 hours, the precipitation of rare earth sulfate double salt was obtained, separated from other components, and after subsequent treatment, rare earth oxides of lanthanum and cerium were obtained; the insoluble residue was dissolved with hydrochloric acid + chlorine gas, and the platinum group metal solution was processed through t...
Embodiment 2
[0017] Embodiment 2, see attached figure 1 1. Finely grind the exhausted automobile exhaust purification catalyst to a particle size range of 74-90 μm, mix the finely ground exhausted automobile exhaust catalyst with concentrated acid sulfuric acid at a mass ratio of 1:0.8, and keep the temperature in a muffle furnace at 300° C. for 3 hours for roasting; The roasted product is leached with 1mol / L sulfuric acid at 60°C for 4 hours, maintaining a liquid-solid ratio of 3, and after filtration and separation, the rare earth solution and insoluble residue containing platinum group metals are obtained; add sodium sulfate to the rare earth solution and react at 80°C After 3 hours, the precipitation of rare earth sulfate double salt was obtained, separated from other components, and after subsequent treatment, rare earth oxides of lanthanum and cerium were obtained; the insoluble residue was dissolved with hydrochloric acid + chlorine gas, and the platinum group metal solution was proc...
Embodiment 3
[0018] Embodiment 3, see attached figure 1 1. Finely grind the exhausted automobile exhaust purification catalyst to a particle size range of 74-125 μm, mix the finely ground exhausted automobile exhaust catalyst with concentrated acid sulfuric acid at a mass ratio of 1:1.2, and keep the temperature in a muffle furnace at 250° C. for 5 hours of roasting; The roasted product is leached with 0.5mol / L sulfuric acid at 80°C for 4 hours, maintaining a liquid-solid ratio of 4, and after filtration and separation, the rare earth solution and insoluble slag containing platinum group metals are obtained; add sodium sulfate to the rare earth solution, and at 80°C After reacting for 3 hours, the precipitation of rare earth sulfate double salt is obtained, which is separated from other components, and after subsequent treatment, rare earth oxides of lanthanum and cerium are obtained; the insoluble residue is dissolved with hydrochloric acid + chlorine gas, and the platinum group metal solu...
PUM
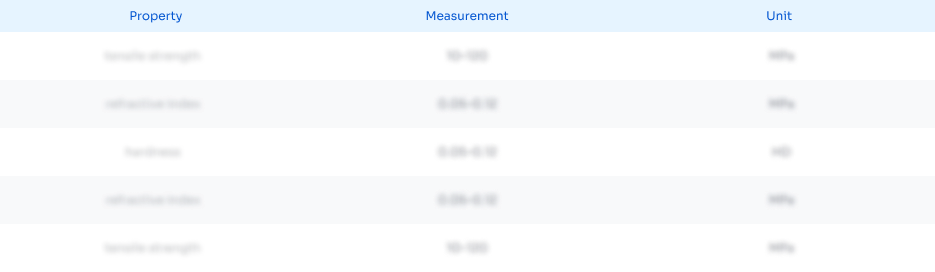
Abstract
Description
Claims
Application Information

- R&D
- Intellectual Property
- Life Sciences
- Materials
- Tech Scout
- Unparalleled Data Quality
- Higher Quality Content
- 60% Fewer Hallucinations
Browse by: Latest US Patents, China's latest patents, Technical Efficacy Thesaurus, Application Domain, Technology Topic, Popular Technical Reports.
© 2025 PatSnap. All rights reserved.Legal|Privacy policy|Modern Slavery Act Transparency Statement|Sitemap|About US| Contact US: help@patsnap.com