Method of preparing titanium nitride-coated carbon black material through alkoxide hydrolysis
A technology for coating carbon black and titanium nitride with titanium nitride is applied in chemical instruments and methods, fibrous fillers, inorganic pigment treatment, etc. Improve chemical stability and thermal stability, improve thermal stability, good effect of purity
- Summary
- Abstract
- Description
- Claims
- Application Information
AI Technical Summary
Problems solved by technology
Method used
Examples
Embodiment 1
[0022] (1) Mix 5mL methoxyethanol and 6mL tetraisopropyl titanate with 160mL anhydrous isopropanol and 3mL distilled water, and then reflux the mixture at 80°C for 4 hours to hydrolyze to form TiO particles 2 ;
[0023] (2) Put 15g of carbon black with a particle size of 35nm into the above solution; adjust the pH value to about 7 with a small amount of ammonia water, gradually heat to 80°C and reflux for 3 hours, and the TiO produced by hydrolysis 2 Depositing carbon black particles coated with titanium dioxide on the surface of carbon black;
[0024] (3) The titanium dioxide-coated carbon black particles prepared above were centrifugally filtered, washed 5 times with ethanol, and dried at room temperature for 6 hours;
[0025] (4) Nitriding the dry titanium dioxide-coated carbon black particles at 900°C, using ammonia gas as the reducing agent, and the nitriding time is 3 hours, and the titanium nitride-coated particles coated with titanium nitride on the surface can be obt...
Embodiment 2
[0027] (1) Add 5mL of methoxyethanol and 6mL of tetraisopropyl titanate to 120mL of anhydrous isopropanol and 5mL of distilled water for mixing, and then reflux the mixed solution at 85°C for 3 hours to hydrolyze to generate granular TiO 2 ;
[0028] (2) Put 8g of carbon black with a particle size of 50nm into the above solution; adjust the pH value to about 7 with a small amount of ammonia water, gradually heat to 80°C and reflux for 2.5 hours, and the TiO2 generated by hydrolysis is deposited on the surface of the carbon black to obtain a titanium dioxide coating. Coated carbon black particles;
[0029] (3) The titanium dioxide-coated carbon black particles prepared above were centrifuged and washed with ethanol for 3 times, and dried at room temperature for 4 hours;
[0030] (4) Nitriding the dry titanium dioxide-coated carbon black particles at 850°C, using ammonia gas as a reducing agent, and the nitriding time is 4 hours, and the titanium nitride-coated particles coated...
Embodiment 3
[0032] (1) For every 5mL of methoxyethanol and 4mL of tetraisopropyl titanate, add 180mL of anhydrous isopropanol and 10mL of distilled water for mixing, and then reflux the mixed solution at 70°C for 2 hours to hydrolyze to form TiO particles 2 ;
[0033] (2) Take 25g of carbon black with a particle size of 15nm and put it into the above solution; adjust the pH value to about 7 with a small amount of ammonia water, gradually heat to 80°C and reflux for 2 hours, and the TiO2 generated by hydrolysis is deposited on the surface of the carbon black to obtain titanium dioxide coating carbon black particles;
[0034] (3) The titanium dioxide-coated carbon black particles prepared above were centrifuged and washed with ethanol for 8 times, and dried at room temperature for 8 hours;
[0035] (4) Nitriding the dry titanium dioxide-coated carbon black particles at 800°C, using ammonia gas as the reducing agent, and the nitriding time is 2 hours, and the titanium nitride-coated particl...
PUM
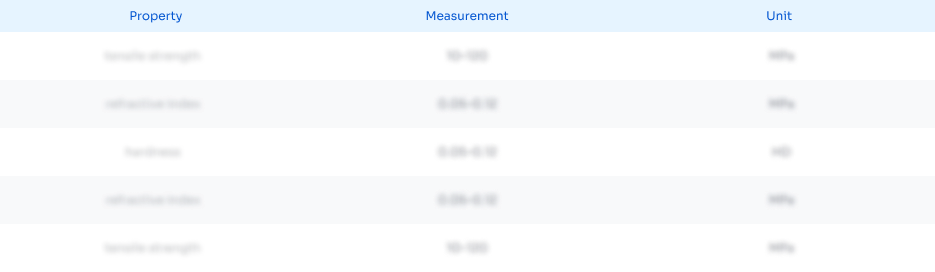
Abstract
Description
Claims
Application Information

- Generate Ideas
- Intellectual Property
- Life Sciences
- Materials
- Tech Scout
- Unparalleled Data Quality
- Higher Quality Content
- 60% Fewer Hallucinations
Browse by: Latest US Patents, China's latest patents, Technical Efficacy Thesaurus, Application Domain, Technology Topic, Popular Technical Reports.
© 2025 PatSnap. All rights reserved.Legal|Privacy policy|Modern Slavery Act Transparency Statement|Sitemap|About US| Contact US: help@patsnap.com