Metal and PA-12 composite material for 3D printing and preparation method of metal and PA-12 composite material
A PA-12, composite material technology, applied in the field of 3D printing, can solve the problems of PA-12's large shrinkage rate and easy warpage deformation, and achieve the effect of low shrinkage rate, improved mechanical properties, and reduced warpage.
- Summary
- Abstract
- Description
- Claims
- Application Information
AI Technical Summary
Problems solved by technology
Method used
Examples
Embodiment 1
[0024] A 3D printing metal PA-12 composite material, prepared from the following raw materials in parts by weight: 250 parts of copper powder, 750 parts of PA-12 nylon material, 2 parts of coupling agent, 5 parts of dispersant, 5 parts of lubricant, 18 parts of toughening agent; Its concrete preparation method step is:
[0025] Step 1: Prepare copper powder, PA-12 nylon material, coupling agent, dispersant, lubricant and toughening agent material, and dry each raw material for later use, so that the moisture content of each raw material is less than 0.05%;
[0026] Step 2: Weigh 250 parts of copper powder, 350 parts of PA-12 nylon material, 2 parts of coupling agent, 5 parts of dispersing agent, 5 parts of lubricant, and 18 parts of toughening agent according to parts by weight;
[0027] Step 3: Add the copper powder weighed in step 2 to the planetary ball mill, add the coupling agent weighed in step 2 and continue mixing for 10 minutes, then add the dispersant and lubricant w...
Embodiment 2
[0032] A 3D printing metal PA-12 composite material, made from the following raw materials in parts by weight: 300 parts of copper powder, 350 parts of PA-12 nylon material, 3 parts of coupling agent, 10 parts of dispersant, 6 parts of lubricant, 20 parts of toughening agent; Its concrete preparation method step is:
[0033] Step 1: Prepare copper powder, PA-12 nylon material, coupling agent, dispersant, lubricant and toughening agent material, and dry each raw material for later use, so that the moisture content of each raw material is less than 0.05%,;
[0034] Step 2: Weigh 300 parts of copper powder, 350 parts of PA-12 nylon material, 3 parts of coupling agent, 10 parts of dispersant, 6 parts of lubricant, and 20 parts of toughening agent according to parts by weight;
[0035] Step 3: Add the copper powder weighed in step 2 to the planetary ball mill, add the coupling agent weighed in step 2 and continue mixing for 10 minutes, then add the dispersant and lubricant weighed ...
Embodiment 3
[0040] A 3D printing metal PA-12 composite material, made from the following raw materials in parts by weight: 330 parts of copper powder, 370 parts of PA-12 nylon material, 5 parts of coupling agent, 15 parts of dispersant, 10 parts of lubricant, 125 parts of toughening agent; Its concrete preparation method step is:
[0041] Step 1: Prepare copper powder, PA-12 nylon material, coupling agent, dispersant, lubricant and toughening agent material, and dry each raw material for later use, so that the moisture content of each raw material is less than 0.05%;
[0042] Step 2: Weigh 330 parts of copper powder, 180 parts of PA-12 nylon material, 5 parts of coupling agent, 15 parts of dispersant, 10 parts of lubricant, and 125 parts of toughening agent according to parts by weight;
[0043] Step 3: Add the copper powder weighed in step 2 to the planetary ball mill, add the coupling agent weighed in step 2 and continue mixing for 10 minutes, then add the dispersant and lubricant weigh...
PUM
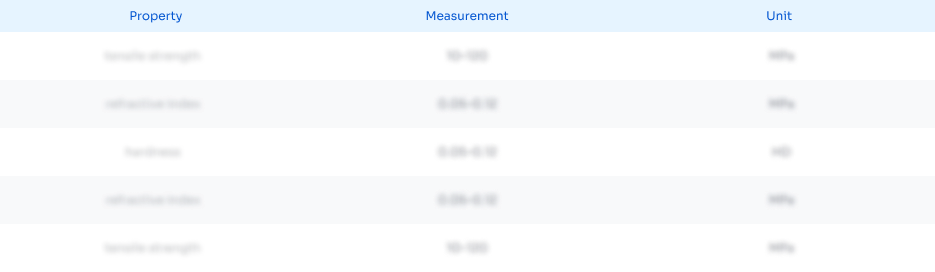
Abstract
Description
Claims
Application Information

- Generate Ideas
- Intellectual Property
- Life Sciences
- Materials
- Tech Scout
- Unparalleled Data Quality
- Higher Quality Content
- 60% Fewer Hallucinations
Browse by: Latest US Patents, China's latest patents, Technical Efficacy Thesaurus, Application Domain, Technology Topic, Popular Technical Reports.
© 2025 PatSnap. All rights reserved.Legal|Privacy policy|Modern Slavery Act Transparency Statement|Sitemap|About US| Contact US: help@patsnap.com