Memory alloy wire installation assembly, connection element used by same and connection element fabrication process
A technology of memory alloy wire and installation components, which is used in the manufacture of contacts, tightening/insulating connectors, connections, etc., can solve the problems affecting the characteristics of memory alloy wires, folded memory alloy wires, and weak connections, and achieves electrical conductivity. Good rate, high connection strength, good electrical conductivity
- Summary
- Abstract
- Description
- Claims
- Application Information
AI Technical Summary
Problems solved by technology
Method used
Image
Examples
Embodiment 1
[0020] The aluminum alloy connector in this embodiment contains the following components by weight percentage:
[0021] Aluminum 80%, Copper 8%, Magnesium 7%, Zinc 5%.
[0022] The manufacturing process of aluminum alloy connectors includes the following steps:
[0023] 1. Put the zinc and magnesium powder into the furnace to melt, and then cast the zinc-magnesium alloy block after refining;
[0024] 2. Put the aluminum block into the furnace and heat up to 820°C to melt, then heat up to 860°C to add copper, mix thoroughly and then refine;
[0025] 3. When casting an aluminum alloy sheet and cooling it down to 220°C, bend one end of the sheet up and then down, and then cool the sheet to room temperature;
[0026] Four, offer jack 5 in the middle part of sheet.
Embodiment 2
[0028] The aluminum alloy connector in this embodiment contains the following components by weight percentage:
[0029] Aluminum 84%, copper 7%, magnesium 6%, zinc 3%.
[0030] The manufacturing process of aluminum alloy connectors includes the following steps:
[0031] 1. Put the zinc and magnesium powder into the furnace to melt, and then cast the zinc-magnesium alloy block after refining;
[0032] 2. Put the aluminum block into the furnace and heat up to 825°C to melt, then heat up to 870°C and add copper, mix thoroughly and then refine;
[0033] 3. When casting an aluminum alloy sheet and cooling it down to 240°C, bend one end of the sheet upward and then bend downward, and then cool the sheet to room temperature;
[0034] Four, offer jack 5 in the middle part of sheet.
Embodiment 3
[0036] The aluminum alloy connector in this embodiment contains the following components by weight percentage:
[0037] Aluminum 90%, Copper 4%, Magnesium 4%, Zinc 2%.
[0038] The manufacturing process of aluminum alloy connectors includes the following steps:
[0039] 1. Put the zinc and magnesium powder into the furnace to melt, and then cast the zinc-magnesium alloy block after refining;
[0040] 2. Put the aluminum block into the furnace and heat up to 830°C to melt, then heat up to 880°C to add copper, mix thoroughly and then refine;
[0041] 3. When casting an aluminum alloy sheet and cooling it down to 260°C, bend one end of the sheet upward and then bend downward, and then cool the sheet to room temperature;
[0042] Four, offer jack 5 in the middle part of sheet.
PUM
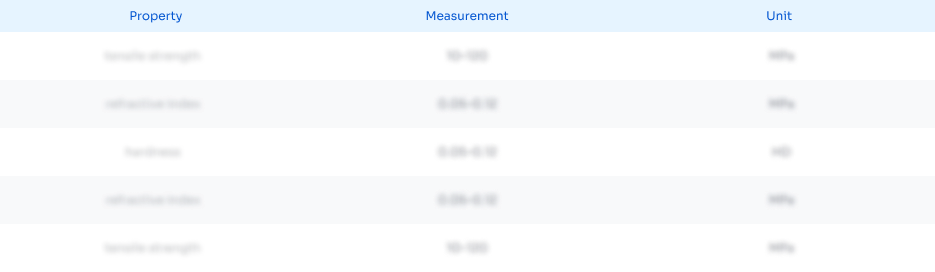
Abstract
Description
Claims
Application Information

- Generate Ideas
- Intellectual Property
- Life Sciences
- Materials
- Tech Scout
- Unparalleled Data Quality
- Higher Quality Content
- 60% Fewer Hallucinations
Browse by: Latest US Patents, China's latest patents, Technical Efficacy Thesaurus, Application Domain, Technology Topic, Popular Technical Reports.
© 2025 PatSnap. All rights reserved.Legal|Privacy policy|Modern Slavery Act Transparency Statement|Sitemap|About US| Contact US: help@patsnap.com