Alkylation method
A technology for alkylation and alkylation reaction, applied in the field of alkylation, can solve problems such as the reduction of alkylbenzene selectivity, and achieve the effects of high ethylbenzene selectivity, lower reaction temperature and pressure, and good low-temperature activity
- Summary
- Abstract
- Description
- Claims
- Application Information
AI Technical Summary
Problems solved by technology
Method used
Image
Examples
preparation example
[0068] Preparation of conventional β molecular sieves: add sodium metaaluminate solution (sodium oxide 145.8g / L, aluminum oxide 102.8g / L), tetraethylammonium hydroxide (TEAOH, 2.417N, Guangzhou Dayou Fine Chemical Co., Ltd.) into deionized Heat to dissolve in water, stir evenly to make a working solution, mix coarse-porous silica gel (150-250μm, 500m 2 / g, 0.9mL / g, Qingdao Ocean Chemical Factory) mixed with the above working solution, so that the surface of the silica gel is wetted by the working solution to obtain a reaction mixture, wherein the molar ratio of each component is SiO 2 / Al 2 o 3 =20,Na 2 O / SiO 2 =0.075, TEAOH / SiO 2 =0.09,H 2 O / SiO 2 = 6.5. The reaction mixture was crystallized in a high-pressure reactor at 120°C for 24 hours, and then crystallized at 140°C for 48 hours. After cooling to room temperature, the solid product was separated, washed, and dried at 110°C to obtain SiO 2 / Al 2 o 3 (Molar ratio)=20 beta molecular sieve raw powder, D value is 1....
Embodiment 1
[0073] as previously stated figure 1 Alkylation is carried out according to the technical process, and the alkylation catalyst used is the catalyst A of the preparation example. In addition, the production of alkylbenzene (ethylbenzene) also includes transalkylation reaction and product rectification (flow process is not drawn), and the transalkylation catalyst that uses is AEB-1 type catalyst, and following embodiment is identical:
[0074] After the raw material benzene from pipeline 35 is mixed with the alkylbenzene from pipeline 36 and the part of ethylene coming through pipelines 31 and 32 successively, it enters the first reaction zone 45 through pipeline 37 and reacts to generate alkylbenzene (comprising ethylbenzene, polybenzene, Ethylbenzene), the first reaction zone 45 has 2 sections of catalyst beds, and each section introduces ethylene through pipelines 31,32. Part (30% by weight) of the reaction product in the first reaction zone is led to the inlet of the first ...
Embodiment 2
[0079] as previously stated figure 2 The process flow for alkylation:
[0080] The raw material benzene from the pipeline 135 and the alkylbenzene from the pipeline 136, and the part of impure low-carbon olefins (its main composition (weight %): hydrogen 2.99, nitrogen 36.34, oxygen 1.74, CO1. 7. CO 2 7.67, methane 16.64, ethane 13.91, ethylene 18.33, propylene 0.07, C40.01) mixed, enter the first reaction zone 145 through the pipeline 137 to react to generate alkylbenzene (including ethylbenzene, polyethylbenzene). The first reaction zone 145 has two stages of catalyst beds, and each stage introduces impure light olefins through pipelines 131 and 132. The effluent 138 from the first reaction zone is mixed with the alkylbenzene from the pipeline 136A and part of the impure light olefins from the pipelines 131 and 133 sequentially, and enters the second reaction zone 146 through the pipeline 139 to react and generate alkylbenzene. The second reaction zone 146 has two stages...
PUM
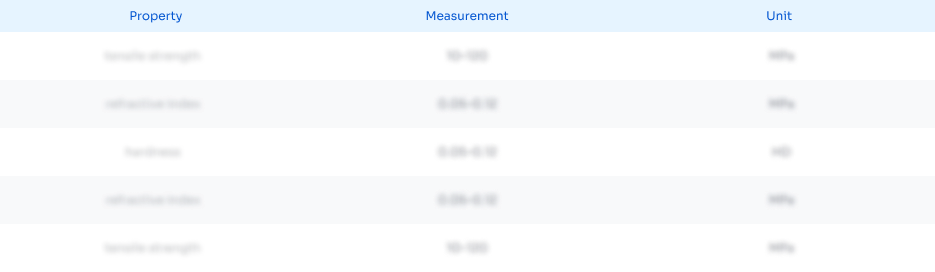
Abstract
Description
Claims
Application Information

- Generate Ideas
- Intellectual Property
- Life Sciences
- Materials
- Tech Scout
- Unparalleled Data Quality
- Higher Quality Content
- 60% Fewer Hallucinations
Browse by: Latest US Patents, China's latest patents, Technical Efficacy Thesaurus, Application Domain, Technology Topic, Popular Technical Reports.
© 2025 PatSnap. All rights reserved.Legal|Privacy policy|Modern Slavery Act Transparency Statement|Sitemap|About US| Contact US: help@patsnap.com