Organic electroluminescence device
An electroluminescent device and electroluminescent technology, applied in the direction of organic semiconductor devices, electro-solid devices, electrical components, etc., can solve the problems of low light emitting performance, refractive index difference, light loss, etc., to improve luminous efficiency, hole transport, etc. The effect of enhanced performance and enhanced light extraction efficiency
- Summary
- Abstract
- Description
- Claims
- Application Information
AI Technical Summary
Problems solved by technology
Method used
Image
Examples
Embodiment 1
[0048] A method for preparing an organic electroluminescent device, comprising the following steps:
[0049] (1) The conductive anode 1 is made of indium tin oxide glass (ITO). First, the conductive anode 1 is subjected to photolithography treatment, and then cut into 2×2cm 2 Then use detergent, deionized water, acetone, ethanol, and isopropanol to ultrasonically clean the glass surface for 15 minutes to remove organic pollutants on the glass surface, clean it and air dry it;
[0050] (2) 20mgMoO 3 Immerse in 10ml of zinc acetate solution, the mass percentage concentration of zinc acetate solution is 35%, soak for 60min to obtain a suspension solution, after drying the suspension solution, put it in a muffle furnace for calcination, the calcination temperature is 400°C, and the calcination time is 30min, to obtain MoO coated with ZnO particles on the surface 3 , and then use the vacuum coating system to 5×10 -3 The pressure of Pa and the evaporation rate of 1nm / s will coat ...
Embodiment 2
[0059] A method for preparing an organic electroluminescent device, comprising the following steps:
[0060] (1) The conductive anode is made of aluminum-doped zinc oxide glass (AZO). First, the conductive anode is subjected to photolithography treatment, and then cut into 2×2cm 2 Then use detergent, deionized water, acetone, ethanol, and isopropanol to ultrasonically clean the glass surface for 15 minutes to remove organic pollutants on the glass surface, clean it and air dry it;
[0061] (2) 50mgWO 3 Soak in 10ml of zinc acetate solution, the mass percent concentration of zinc acetate solution is 10%, soak for 30min to obtain a suspension solution, dry the suspension solution, put it in a muffle furnace for calcination, the calcination temperature is 500°C, and the calcination time is 15min to obtain WO coated with ZnO particles on the surface 3 , the mass ratio of zinc acetate to tungsten oxide is 0.02:1, and then the vacuum coating system is used to 2×10 -4 The pressure...
Embodiment 3
[0070] A method for preparing an organic electroluminescent device, comprising the following steps:
[0071] (1) The conductive anode is made of indium-doped zinc oxide glass (IZO). First, the conductive anode is photolithographically processed, and then cut into 2×2cm 2 Then use detergent, deionized water, acetone, ethanol, and isopropanol to ultrasonically clean the glass surface for 15 minutes to remove organic pollutants on the glass surface, clean it and air dry it;
[0072] (2) Add 10mgV 2 o 5 Immerse in 10ml of zinc acetate solution, the mass percentage concentration of zinc acetate solution is 60%, soak for 60min to obtain a suspension solution, after drying the suspension solution, put it in a muffle furnace for calcination, the calcination temperature is 300°C, and the calcination time is 60min, to obtain the surface coated with ZnO particles V 2 o 5 , the mass ratio of zinc acetate to vanadium pentoxide is 0.6:1, and then the vacuum coating system is used to 1×1...
PUM
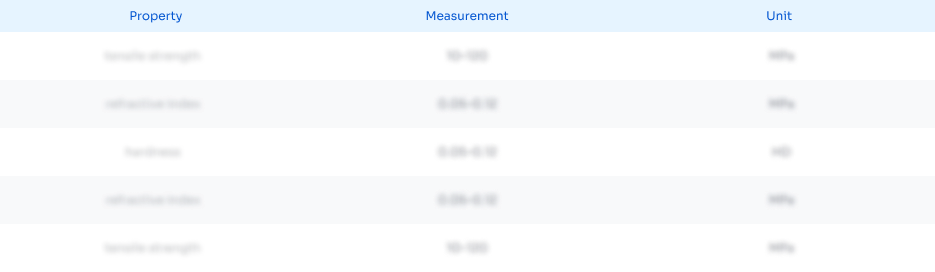
Abstract
Description
Claims
Application Information

- R&D
- Intellectual Property
- Life Sciences
- Materials
- Tech Scout
- Unparalleled Data Quality
- Higher Quality Content
- 60% Fewer Hallucinations
Browse by: Latest US Patents, China's latest patents, Technical Efficacy Thesaurus, Application Domain, Technology Topic, Popular Technical Reports.
© 2025 PatSnap. All rights reserved.Legal|Privacy policy|Modern Slavery Act Transparency Statement|Sitemap|About US| Contact US: help@patsnap.com