Preparation method of nylon powder for selective laser sintering
A laser sintering and nylon powder technology is applied in the field of nylon powder preparation for selective laser sintering, which can solve the problems of excessive solvent residues in nylon salts, changing the color of nylon salts, and affecting the performance of sintered parts, so as to improve drying efficiency and drying quality. Improved, fast heating effect
- Summary
- Abstract
- Description
- Claims
- Application Information
AI Technical Summary
Problems solved by technology
Method used
Image
Examples
preparation example Construction
[0021] A method for preparing nylon powder for selective laser sintering, characterized in that it comprises the following steps:
[0022] 1) Put a sufficient amount of dibasic acid, diamine and ethanol into a reaction vessel, and react to obtain a nylon salt solution, and centrifugally filter to obtain a copolymerized nylon salt. The dibasic acid is adipic acid, sebacic acid, One or more of undecanedioic acid, dodecanedioic acid, tridecanedioic acid, tetradecanedioic acid, the diamines are hexamethylenediamine, decanediamine, undecanediamine , one or more of dodecanediamine, tridecanediamine, tetradecanediamine;
[0023] 2) Place the obtained nylon salt in a microwave drying apparatus and dry it for 10-30 minutes at a temperature of 30-40°C to obtain a dried nylon salt after drying. The humidity of the dried nylon salt is 0.1-5.0%;
[0024] 3) Add dry nylon salt, molecular weight regulator, and deionized water into the closed polymerization reactor, and obtain copolymerized ...
Embodiment 1
[0028] Add 6.9Kg of dodecanedioic acid, 5.16Kg of dodecanediamine and 9.6Kg of ethanol into the reactor, generate a copolymerized nylon salt solution at 75°C, and centrifugally filter to obtain nylon 1212 salt;
[0029] The nylon salt prepared above was placed in a microwave drying apparatus and dried at 40°C for 10 minutes to obtain the dried nylon salt. The humidity of the dried nylon salt was 0.1%;
[0030] Add the copolymerized nylon salt, molecular weight regulator and deionized water into the polymerization kettle. Airtight, vacuumize, and then pass through the carbon dioxide protection gas 0.15MPa. Raise the temperature to 200°C, the pressure reaches 1.2MPa, keep the pressure for 3 hours, then slowly release the air to normal pressure, raise the temperature to 245°C and keep the reaction for 3 hours, stop heating, water-cool the strands to discharge, pelletize, and obtain copolymerized nylon 1212 pellets. Then add the prepared copolymerized nylon 1212 pellets into the...
Embodiment 2
[0032] Add 6.9Kg of dodecanedioic acid, 5.16Kg of dodecanediamine and 9.6Kg of ethanol into the reactor, generate a copolymerized nylon salt solution at 75°C, and centrifugally filter to obtain nylon 1212 salt;
[0033] The nylon salt prepared above was placed in a microwave drying apparatus and dried at 35°C for 25 minutes to obtain the dried nylon salt. The humidity of the dried nylon salt was 5%;
[0034] Add the copolymerized nylon salt, molecular weight regulator and deionized water into the polymerization kettle. Airtight, vacuumize, and then pass through the carbon dioxide protection gas 0.12MPa. Raise the temperature to 220°C, the pressure reaches 1.5MPa, keep the pressure for 2 hours, then slowly release the air to normal pressure, raise the temperature to 260°C and keep the reaction for 2 hours, stop heating, water-cool the strands to discharge, pelletize, and obtain copolymerized nylon 1212 pellets. Then add the prepared copolymerized nylon 1212 pellets into the p...
PUM
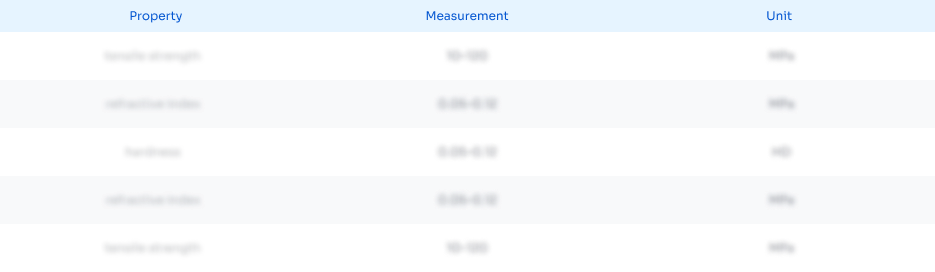
Abstract
Description
Claims
Application Information

- R&D
- Intellectual Property
- Life Sciences
- Materials
- Tech Scout
- Unparalleled Data Quality
- Higher Quality Content
- 60% Fewer Hallucinations
Browse by: Latest US Patents, China's latest patents, Technical Efficacy Thesaurus, Application Domain, Technology Topic, Popular Technical Reports.
© 2025 PatSnap. All rights reserved.Legal|Privacy policy|Modern Slavery Act Transparency Statement|Sitemap|About US| Contact US: help@patsnap.com