High-strength alkali-resistant brush wires and production process thereof
A production process and alkali-resistant technology, which is applied in the manufacture of rayon, conjugated synthetic polymer rayon, textiles and papermaking, etc., can solve problems such as poor tolerance and unsatisfactory high-temperature environment tolerance, and achieve Low processing cost, improved alkali resistance, and simple production process
- Summary
- Abstract
- Description
- Claims
- Application Information
AI Technical Summary
Problems solved by technology
Method used
Examples
Embodiment 1
[0019] Example 1 A high-strength alkali-resistant brush filament and its production process, consisting of the following raw materials in parts by weight: 40 parts of polyurethane, 10 parts of ammonium methyl sulfate, 10 parts of coupling agent, fatty alcohol polyoxyethylene ether 30 parts, 18 parts of sodium laurate, 4 parts of phosphoric acid, 2 parts of monoethanolamine, 6 parts of glass fiber, 3 parts of organic alcohol amine, 2 parts of azobisisobutyronitrile, 6 parts of amino-2-methyl-1-propanol , 12 parts of silicon dioxide, 40001 parts of polyethylene glycol, 1 part of accelerator, 10 parts of curing agent, 5 parts of alkali absorbing agent, and 2 parts of antioxidant.
[0020] The antioxidant is selected from one or a mixture of metal halide salt mixtures, sulfur compounds, metal acetates, hindered phenols.
[0021] A high-strength alkali-resistant brush filament and its production process, comprising the following steps:
[0022] (1) Put polyurethane, trimethyl ammo...
Embodiment 2
[0031] Embodiment 2 A high-strength alkali-resistant brush filament and its production process, consisting of the following raw materials in parts by weight: 45 parts of polyurethane, 20 parts of ammonium methyl sulfate, 20 parts of coupling agent, fatty alcohol polyoxyethylene ether 35 parts, 20 parts of sodium laurate, 5 parts of phosphoric acid, 4 parts of monoethanolamine, 8 parts of glass fiber, 5 parts of organic alcohol amine, 4 parts of azobisisobutyronitrile, 8 parts of amino-2-methyl-1-propanol parts, 15 parts of silicon dioxide, 40004 parts of polyethylene glycol, 3 parts of accelerator, 20 parts of curing agent, 8 parts of alkali absorbing agent, and 3 parts of antioxidant.
[0032] The antioxidant is selected from one or a mixture of metal halide salt mixtures, sulfur compounds, metal acetates, hindered phenols.
[0033] A high-strength alkali-resistant brush filament and its production process, comprising the following steps:
[0034] (1) Put polyurethane, trime...
Embodiment 3
[0043] Embodiment 3 A high-strength alkali-resistant brush filament and its production process, consisting of the following raw materials in parts by weight: 42 parts of polyurethane, 15 parts of ammonium methyl sulfate, 16 parts of coupling agent, fatty alcohol polyoxyethylene ether 32 parts, 19 parts of sodium laurate, 4 parts of phosphoric acid, 3 parts of monoethanolamine, 7 parts of glass fiber, 4 parts of organic alcohol amine, 2 parts of azobisisobutyronitrile, 7 parts of amino-2-methyl-1-propanol parts, 14 parts of silicon dioxide, 40003 parts of polyethylene glycol, 2 parts of accelerator, 16 parts of curing agent, 6 parts of alkali absorbing agent, and 3 parts of antioxidant.
[0044] The antioxidant is selected from one or a mixture of metal halide salt mixtures, sulfur compounds, metal acetates, hindered phenols.
[0045] A high-strength alkali-resistant brush filament and its production process, comprising the following steps:
[0046] (1) Put polyurethane, trime...
PUM
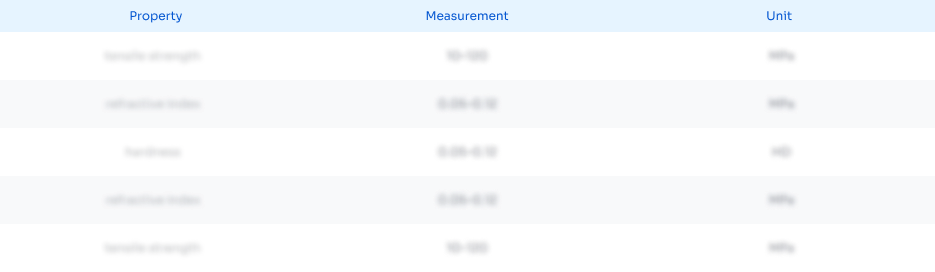
Abstract
Description
Claims
Application Information

- Generate Ideas
- Intellectual Property
- Life Sciences
- Materials
- Tech Scout
- Unparalleled Data Quality
- Higher Quality Content
- 60% Fewer Hallucinations
Browse by: Latest US Patents, China's latest patents, Technical Efficacy Thesaurus, Application Domain, Technology Topic, Popular Technical Reports.
© 2025 PatSnap. All rights reserved.Legal|Privacy policy|Modern Slavery Act Transparency Statement|Sitemap|About US| Contact US: help@patsnap.com