A kind of method of producing anhydrous magnesium carbonate with magnesium-containing mother liquor
A technology of anhydrous magnesium carbonate and mother liquor, applied in the direction of magnesium carbonate, chemical instruments and methods, inorganic chemistry, etc., can solve the problems of not fundamentally solving the problems of filtration, increasing the separation process, complicated process, etc., and achieve good filtration and separation performance , low process cost and simple process
- Summary
- Abstract
- Description
- Claims
- Application Information
AI Technical Summary
Problems solved by technology
Method used
Examples
Embodiment 1
[0027] (1) Adjust the pH value: pass ammonia gas with a volume concentration of 95% into 1000g (volume 750mL) of magnesium-containing mother liquor magnesium sulfate subtype salt lake old brine (Mg 2+ The mass concentration is 6.5wt%), to mother liquor pH=10.56, get 765mL Mg(OH) 2 slurry;
[0028] (2) CO 2 Carbonization: CO with a volume concentration of 85% 2 With the pressure of 0.1Mpa and the speed of 2.8L / L solution h, pass into the 765mL Mg(OH) obtained in step (1) 2 Carry out carbonization reaction at room temperature at 20°C in the slurry, and stop the reaction when the pH value is 7.5 to obtain the carbonization mother liquor;
[0029](3) Pyrolysis separation: heat and decompose the carbonized mother liquor obtained in step (2) at 40°C for 50 minutes, and separate solid and liquid to obtain MgCO 3 ·3H 2 O solid salt and pyrolysis separation mother liquor;
[0030] (4) Calcination: MgCO obtained in step (3) 3 ·3H 2 O was calcined at 250°C for 50min to obtain 211...
Embodiment 2
[0035] (1) Adjust the pH value: pass ammonia gas with a volume concentration of 90% into 2000g (volume 1900mL) of magnesium-containing mother liquor polyhalite leaching mother liquor (Mg 2+ The mass concentration is 0.95wt%), to mother liquor pH=11.4, get 1955mL Mg(OH) 2 slurry;
[0036] (2) CO 2 Carbonization: CO with a volume concentration of 95% 2 With the pressure of 0.5Mpa and the speed of 4.5L / L solution h, pass through step (1) gained 1955mL Mg(OH) 2 In the slurry, carry out carbonization reaction at room temperature at 30°C, and terminate the reaction when the pH value is 8.0, to obtain the carbonization mother liquor;
[0037] (3) Pyrolysis separation: heat and decompose the carbonized mother liquor obtained in step (2) at 70°C for 30 minutes, and separate solid and liquid to obtain MgCO 3 ·3H 2 O solid salt and pyrolysis separation mother liquor;
[0038] (4) Calcination: MgCO obtained in step (3) 3 ·3H 2 O was calcined at 290° C. for 40 minutes to obtain 63....
Embodiment 3
[0043] (1) Adjust the pH value: pass ammonia gas with a volume concentration of 98% into 1500g (volume 1300mL) magnesium-containing mother liquor magnesite nitric acid leaching mother liquor (Mg 2+ The mass concentration is 2.8wt%), to mother liquor pH=11.8, get 1335mL Mg(OH) 2 slurry;
[0044] (2) CO 2 Carbonization: CO with a volume concentration of 90% 2 With the pressure of 0.3Mpa and the speed of 0.7L / L solution h, pass through the 1335mL Mg(OH) obtained in step (1) 2 Carry out carbonization reaction at room temperature at 25°C in the slurry, terminate the reaction when the pH value is 7.8, and obtain the carbonization mother liquor;
[0045] (3) Pyrolysis separation: heat and decompose the carbonized mother liquor obtained in step (2) at 60°C for 60 minutes, and separate solid and liquid to obtain MgCO 3 ·3H 2 O solid salt and pyrolysis separation mother liquor;
[0046] (4) Calcination: MgCO obtained in step (3) 3 ·3H 2 O was calcined at 260° C. for 60 minutes t...
PUM
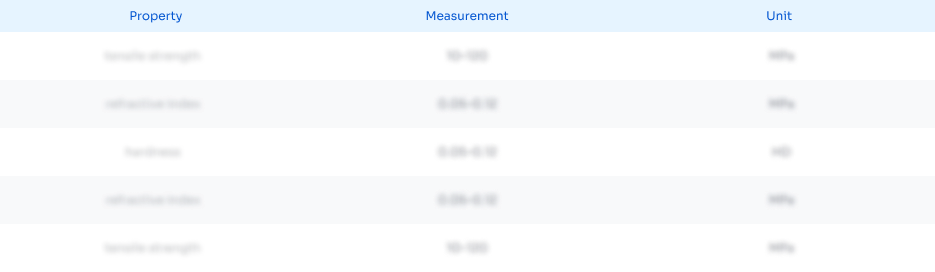
Abstract
Description
Claims
Application Information

- Generate Ideas
- Intellectual Property
- Life Sciences
- Materials
- Tech Scout
- Unparalleled Data Quality
- Higher Quality Content
- 60% Fewer Hallucinations
Browse by: Latest US Patents, China's latest patents, Technical Efficacy Thesaurus, Application Domain, Technology Topic, Popular Technical Reports.
© 2025 PatSnap. All rights reserved.Legal|Privacy policy|Modern Slavery Act Transparency Statement|Sitemap|About US| Contact US: help@patsnap.com