Preparing method for copper ammonia fiber conductive textile
A cupro fiber and textile technology is applied in the field of preparation of cupro fiber conductive textiles, which can solve the problems of few reports and studies on conductive polymer/metal composite conductive textiles, and achieve the effects of facilitating material degradation, saving resources and improving reliability.
- Summary
- Abstract
- Description
- Claims
- Application Information
AI Technical Summary
Problems solved by technology
Method used
Image
Examples
Embodiment 1
[0025] Dissolve 1 g of ferric chloride and 0.4 g of sodium p-toluenesulfonate in 200 mL of deionized water. After the dissolution is completed, an oxidant solution is obtained.
[0026] Rinse the copper ammonia fiber with deionized water, dry it, and place it in a 200 mL pyrrole-ethanol solution with a concentration of 0.5 mol / L for 10 minutes. Take it out and immediately put it in the oxidant solution for 10 minutes, take it out, wash it, and circulate the above process three times and dry it to obtain cupra fibers with polypyrrole deposited on the surface.
[0027] Place the polypyrrole / copper ammonia fiber in the ethanol solution of 3-mercaptopropyltrimethoxysilane with a concentration of 3%, soak for 5 minutes, take it out, and then dry it at 100°C. The soaking and drying cycle is 3 times to obtain the modification After the polypyrrole / copper ammonia fiber.
[0028] The modified polypyrrole / copper ammonia fiber is placed in a copper sulfate solution with a concentration of 3%, ...
Embodiment 2
[0034] 1.5 g of ferric chloride and 0.5 g of sodium p-toluenesulfonate were dissolved in 200 mL of deionized water, and the dissolution was completed to obtain an oxidant solution.
[0035] Rinse the cupra with deionized water, dry it, and place it in a 200 mL pyrrole-ethanol solution with a concentration of 0.6 mol / L for 12 minutes. Take it out and immediately put it in the oxidant solution for 12 minutes, take it out, and wash it. The above process is cycled 4 times and dried to obtain cupra with polypyrrole deposited on the surface.
[0036] Place the polypyrrole / copper ammonia fiber in a 3-mercaptopropyltrimethoxysilane ethanol solution with a concentration of 3.5%, soak for 8 minutes, take it out, and then dry at 110°C. The soaking and drying cycle 4 times to obtain the modification After the polypyrrole / copper ammonia fiber.
[0037] The modified polypyrrole / copper ammonia fiber is placed in a copper sulfate solution with a concentration of 6%, soaked for 60 minutes, taken out...
Embodiment 3
[0043] 2.5 g of ferric chloride and 0.8 g of sodium p-toluenesulfonate were dissolved in 200 mL of deionized water, and the dissolution was completed to obtain an oxidant solution.
[0044] Rinse the cupra with deionized water, dry it, and place it in a 200 mL pyrrole-ethanol solution with a concentration of 0.6 mol / L for 20 minutes. Take it out and immediately put it in the oxidant solution for 15 minutes, take it out, and wash it. The above process is cycled three times and dried to obtain cupra fibers with polypyrrole deposited on the surface.
[0045] Place the polypyrrole / copper ammonia fiber in the ethanol solution of 3-mercaptopropyltrimethoxysilane with a concentration of 4%, soak for 5 minutes, take it out, and then dry it at 115°C. The soaking and drying cycle 3 times to obtain the modification After the polypyrrole / copper ammonia fiber.
[0046] The modified polypyrrole / copper ammonia fiber is placed in a copper sulfate solution with a concentration of 5%, soaked for 40 m...
PUM
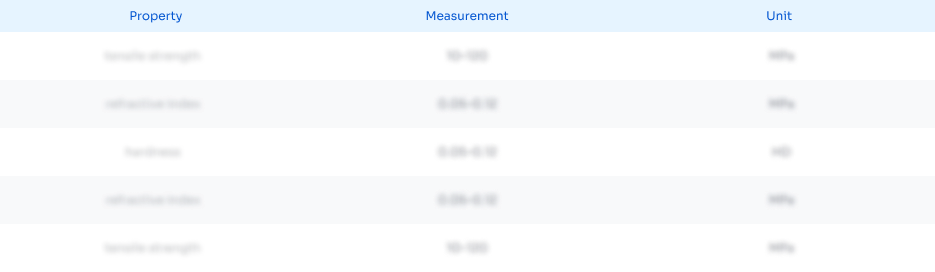
Abstract
Description
Claims
Application Information

- R&D
- Intellectual Property
- Life Sciences
- Materials
- Tech Scout
- Unparalleled Data Quality
- Higher Quality Content
- 60% Fewer Hallucinations
Browse by: Latest US Patents, China's latest patents, Technical Efficacy Thesaurus, Application Domain, Technology Topic, Popular Technical Reports.
© 2025 PatSnap. All rights reserved.Legal|Privacy policy|Modern Slavery Act Transparency Statement|Sitemap|About US| Contact US: help@patsnap.com