A method for recovering precious metals in spent catalysts
A technology for waste catalysts and precious metals, which is applied in the field of recycling precious metals in waste catalysts, to achieve the effects of simple process, convenient operation and guaranteed fluidity
- Summary
- Abstract
- Description
- Claims
- Application Information
AI Technical Summary
Problems solved by technology
Method used
Examples
Embodiment 1
[0046] Aiming at the problem that the existing recovery methods of waste catalysts containing precious metals all use wet chemical methods that are prone to produce liquid secondary pollutants, and cannot effectively control harmful elements such as sulfur, phosphorus, and silicon, so they cannot be applied to the iron and steel refining industry. The invention provides a method with simple process, low processing cost and high quality of recycled products.
[0047]Use the roaster for preliminary deoiling and then use the AOD furnace for refining. It mainly removes harmful phosphorus, sulfur and silicon elements by adding limestone and blowing high-pressure oxygen into the molten steel in the furnace. Temperature of molten steel, adjustment of chemical composition, removal of impurities, removal of gas; thus widely used in the steel refining industry.
[0048] A method for reclaiming precious metals in spent catalysts, the steps of which are:
[0049] The first step, the prep...
Embodiment 2
[0073] Embodiment 2: Dephosphorization, desulfurization and silicon removal are carried out to reclaim metal molybdenum to molybdenum-containing waste catalyst
[0074] The method steps of this embodiment are the same as in Example 1. The spent catalyst containing 14% molybdenum is sent to the roaster for oxidative roasting to remove the residual oil on the surface. CaO is added to the catalyst; in step C, according to the weight ratio of pig iron to the mixture of step B is 1:2.5, the pig iron is added to the AOD furnace at one time; in step F, the weight ratio of clay brick to the mixture of step B is 1 :300, the weight ratio of fluorite and the mixture of step B is 1:600, the weight ratio of C powder and the mixture of step B is 1:3000, and the weight ratio of silicon carbide and the mixture of step B is 1:3000, ensure filter residue Alkalinity is 3.5.
[0075] That is to say, 95% of the molybdenum metal element in the spent molybdenum catalyst can be recovered, and finall...
Embodiment 3
[0076] Embodiment 3: Dephosphorization, desulfurization and silicon removal are carried out to recover molybdenum and nickel from molybdenum and nickel waste catalysts
[0077] The method step of the present embodiment is the same as that of Example 1, and the waste catalyst containing 18% molybdenum and 5.5% nickel is sent into the roasting furnace to carry out oxidative roasting to remove the residual oil on the surface for use. In step B, according to the content P:CaO= Add CaO to the spent catalyst at a ratio of 1:1; in step C, according to the weight ratio of the mixture of pig iron and step B is 1:1, add pig iron to the AOD furnace at one time; in step F, clay bricks and step B The weight ratio of the mixture of fluorite and step B is 1:100, the weight ratio of fluorite and step B mixture is 1:200, the weight ratio of C powder and step B mixture is 1:1000, the weight ratio of silicon carbide and step B mixture For 1:1000, ensure that the filter residue alkalinity is 3. ...
PUM
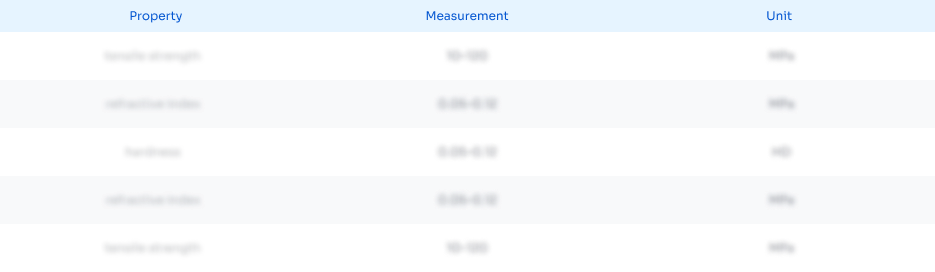
Abstract
Description
Claims
Application Information

- Generate Ideas
- Intellectual Property
- Life Sciences
- Materials
- Tech Scout
- Unparalleled Data Quality
- Higher Quality Content
- 60% Fewer Hallucinations
Browse by: Latest US Patents, China's latest patents, Technical Efficacy Thesaurus, Application Domain, Technology Topic, Popular Technical Reports.
© 2025 PatSnap. All rights reserved.Legal|Privacy policy|Modern Slavery Act Transparency Statement|Sitemap|About US| Contact US: help@patsnap.com