Metal coating used for improving corrosion resistance of spring and preparing method of metal coating
A metal coating and corrosion resistance technology, applied in the field of metal coatings for improving the corrosion resistance of springs and their preparation, can solve the problems of reducing the service life of the equipment, the surface of the spring is easily oxidized, reducing the service life of the spring, etc. Service life, increased corrosion resistance, effect of increased corrosion resistance
- Summary
- Abstract
- Description
- Claims
- Application Information
AI Technical Summary
Problems solved by technology
Method used
Examples
Embodiment 1
[0025] This embodiment provides a metal coating for improving the corrosion resistance of springs, the composition of the metal coating is: carbon: 0.02%, magnesium: 3.1%, chromium: 8.5%, vanadium: 4.5%, Nickel: 8.5%, Cobalt: 2.3%, Niobium: 0.2%, Arsenic: 0.1%, Molybdenum: 0.7%, Tungsten: 0.02%, Selenium: 2.2%, Titanium: 3.2%, Bismuth: 2.6%, Sodium: 1.5%, Neodymium: 2.7%, promethium: 2.3%, erbium: 5.2%, samarium: 4.2%, additives: 7.2%, and the balance is iron;
[0026] The components of the additives are by mass percentage: aluminum powder: 12%, mica powder: 13%, zinc powder: 6%, chromate: 5%, borax: 4%, manganese dioxide: 2%, and amount of iron;
[0027]The preparation method of the auxiliary agent is as follows: mix aluminum powder, mica powder, zinc powder, manganese dioxide, and iron into a heating furnace, heat to 450°C, keep warm for 30min, then heat to 860°C, and then add chromate , Stir the borax components evenly, then heat to 1020°C, keep warm for 3 hours, then use...
Embodiment 2
[0033] This embodiment provides a metal coating for improving the corrosion resistance of springs, the composition of the metal coating is: carbon: 0.04%, magnesium: 3.3%, chromium: 8.8%, vanadium: 4.7%, Nickel: 8.9%, Cobalt: 2.5%, Niobium: 0.5%, Arsenic: 0.3%, Molybdenum: 0.9%, Tungsten: 0.04%, Selenium: 2.5%, Titanium: 3.5%, Bismuth: 2.8%, Sodium: 1.8%, Neodymium: 2.9%, promethium: 2.8%, erbium: 5.4%, samarium: 4.5%, additives: 7.5%, and the balance is iron;
[0034] The components of the additives are by mass percentage: aluminum powder: 14%, mica powder: 15%, zinc powder: 8%, chromate: 7%, borax: 6%, manganese dioxide: 4%, and amount of iron;
[0035] The preparation method of the auxiliary agent is as follows: mix aluminum powder, mica powder, zinc powder, manganese dioxide, and iron into a heating furnace, heat to 480°C, keep warm for 40min, then heat to 880°C, and then add chromate , Stir the borax components evenly, then heat to 1080°C, keep warm for 5 hours, then us...
Embodiment 3
[0041] This embodiment provides a metal coating for improving the corrosion resistance of springs, the composition of the metal coating is: carbon: 0.03%, magnesium: 3.2%, chromium: 8.7%, vanadium: 4.6%, Nickel: 8.8%, Cobalt: 2.4%, Niobium: 0.4%, Arsenic: 0.2%, Molybdenum: 0.8%, Tungsten: 0.03%, Selenium: 2.3%, Titanium: 3.4%, Bismuth: 2.7%, Sodium: 1.6%, Neodymium: 2.8%, promethium: 2.5%, erbium: 5.3%, samarium: 4.4%, additives: 7.3%, and the balance is iron;
[0042] The components of the additives are by mass percentage: aluminum powder: 13%, mica powder: 14%, zinc powder: 7%, chromate: 6%, borax: 5%, manganese dioxide: 3%, and amount of iron;
[0043] The preparation method of the auxiliary agent is as follows: mix aluminum powder, mica powder, zinc powder, manganese dioxide, and iron into a heating furnace, heat to 460°C, keep warm for 35min, then heat to 868°C, and then add chromate , Stir the borax components evenly, then heat to 1050°C, keep warm for 4 hours, then us...
PUM
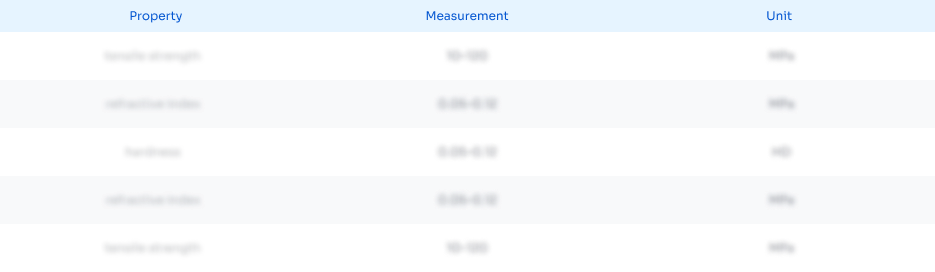
Abstract
Description
Claims
Application Information

- Generate Ideas
- Intellectual Property
- Life Sciences
- Materials
- Tech Scout
- Unparalleled Data Quality
- Higher Quality Content
- 60% Fewer Hallucinations
Browse by: Latest US Patents, China's latest patents, Technical Efficacy Thesaurus, Application Domain, Technology Topic, Popular Technical Reports.
© 2025 PatSnap. All rights reserved.Legal|Privacy policy|Modern Slavery Act Transparency Statement|Sitemap|About US| Contact US: help@patsnap.com