Novel composite material drilling bit and manufacturing method thereof
A composite material and manufacturing method technology, applied in twist drills and other directions, can solve the problems of fiber pullout, chipping and poor surface roughness on the surface of the hole wall, achieve reasonable drill tip angle and rake angle, and reduce axial cutting force , The effect of maintaining the sharpness of the cutting edge
- Summary
- Abstract
- Description
- Claims
- Application Information
AI Technical Summary
Problems solved by technology
Method used
Image
Examples
Embodiment
[0021] see Figure 1~3 , a new type of composite material drill bit of the present invention, including a tool holder 1 and a cutting part 2, the end of the cutting part 2 is made with a step 9, and the step 9 divides the cutting part 2 into the first chip part and the tool holder 1 connected second chip part, and the diameter of the first chip part is smaller than the diameter of the second chip part. 7. A chisel edge 4 is provided between the first main cutting edges 8, and a second main cutting edge 6 and a second auxiliary cutting edge 5 symmetrical to the axis line are arranged at the second chip part. The step 9 and the The first secondary chip edge 7 is connected to the second main chip edge 6 . The rake angle γ of the first auxiliary cutting edge 7 and the second auxiliary cutting edge 5 are the same, and both are 5°-7°. The drill point angle β of the first chip part is 120°-130°. The length B of the chisel edge 4 is 1-1.5 mm.
[0022] A method for making the above...
PUM
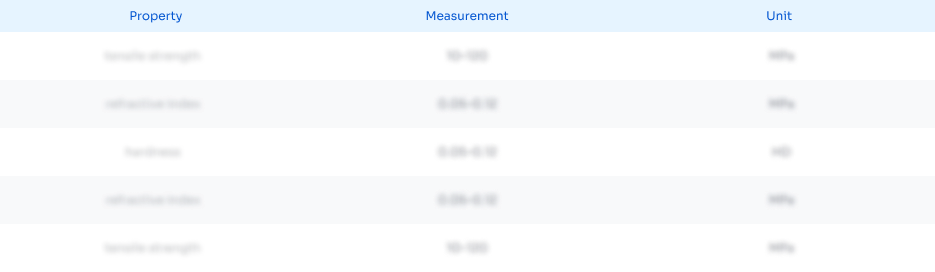
Abstract
Description
Claims
Application Information

- Generate Ideas
- Intellectual Property
- Life Sciences
- Materials
- Tech Scout
- Unparalleled Data Quality
- Higher Quality Content
- 60% Fewer Hallucinations
Browse by: Latest US Patents, China's latest patents, Technical Efficacy Thesaurus, Application Domain, Technology Topic, Popular Technical Reports.
© 2025 PatSnap. All rights reserved.Legal|Privacy policy|Modern Slavery Act Transparency Statement|Sitemap|About US| Contact US: help@patsnap.com