Catalyst for preparing isobutene through isobutane dehydrogenation and preparation method thereof
A catalyst, isobutane technology, applied in the direction of catalyst carrier, chemical instrument and method, metal/metal oxide/metal hydroxide catalyst, etc., can solve the problems of vanadium catalyst is not ideal, the distribution is not uniform enough, etc., to improve the surface Effects of acid-base and electronic properties, improved conversion and selectivity, improved pore structure and surface properties
- Summary
- Abstract
- Description
- Claims
- Application Information
AI Technical Summary
Problems solved by technology
Method used
Examples
Embodiment 1
[0022] (1) Weigh 134.3g of pseudo-boehmite, add 1500mL of deionized water to beating for 20 minutes, then add 11.5mL of concentrated hydrochloric acid (37wt%) to continue beating for 40 minutes.
[0023] (2) After adding 1.8g TEOS and stirring evenly, adjust to pH=9 with ammonia water. Place the material in a hydrothermal kettle and place it in a 95°C oven at a constant temperature for 6 hours. Then it is filtered, dried, placed in a muffle furnace, heated to 550°C at a rate of 2°C / min, and kept at a constant temperature for 6 hours.
[0024] (3) Weigh 6.89g of ammonium metavanadate, 14g of oxalic acid and 0.26g of potassium nitrate, add 83mL of deionized water, stir to dissolve and mix thoroughly with the carrier prepared in step (1), and place it in an oven at 90°C. Dry for 3 hours, place in a muffle furnace, heat up to 550°C at a rate of 2°C / min, and keep the temperature constant for 6 hours. The obtained catalyst is crushed and sieved after being compressed, and particles C1 ...
Embodiment 2
[0026] (1) Weigh 127.7g pseudo-boehmite, add 1500mL deionized water for 20 minutes, add 14.6mL concentrated hydrochloric acid (37wt%) and continue to beat for 40 minutes.
[0027] (2) After adding 3.47g TEOS and stirring evenly, adjust to pH=10 with ammonia water. Place the material in a hydrothermal kettle and place it in a 96°C oven at a constant temperature for 12 hours. Then it is filtered, dried, placed in a muffle furnace, heated to 550°C at a rate of 2°C / min, and kept constant for 3 hours.
[0028] (3) Weigh 11.48g of ammonium metavanadate, 22g of oxalic acid and 2.95g of calcium nitrate, add 78mL of deionized water, stir to dissolve, mix well with the carrier prepared in step (1), and place it in an oven at 90°C. Dry for 3 hours, place in a muffle furnace, heat up to 550°C at a rate of 2°C / min, and keep the temperature constant for 6 hours. The obtained catalyst is crushed and sieved after being compressed, and particles C2 of 20-30 mesh are taken for testing.
Embodiment 3
[0030] (1) Weigh 116.9 g of pseudo-boehmite, add 1300 mL of deionized water to beating for 20 minutes, then add 10.0 mL of concentrated hydrochloric acid (37 wt%) to continue beating for 20 minutes.
[0031] (2) Add 11.76g of silica sol solution (34wt%) and stir evenly, then adjust to pH=11 with ammonia. Place the material in a hydrothermal kettle and place it in an oven at 97°C for 24 hours. Then it is filtered, dried, placed in a muffle furnace, heated to 550°C at a rate of 2°C / min, and kept at a constant temperature for 9 hours.
[0032] (3) Weigh 16.07g of ammonium metavanadate, 22g of oxalic acid and 10.55g of magnesium nitrate, add 72mL of deionized water, stir to dissolve and mix well with the carrier prepared in step (1), and place it in an oven at 90°C. Dry for 3 hours, place in a muffle furnace, heat up to 550°C at a rate of 2°C / min, and keep the temperature constant for 9 hours. The obtained catalyst is crushed and sieved after being compressed, and particles C3 of 20-...
PUM
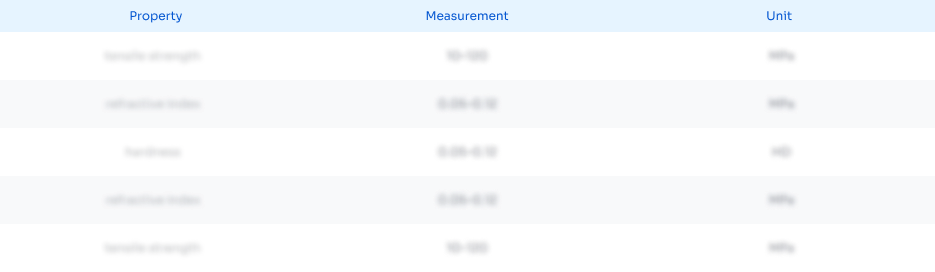
Abstract
Description
Claims
Application Information

- R&D
- Intellectual Property
- Life Sciences
- Materials
- Tech Scout
- Unparalleled Data Quality
- Higher Quality Content
- 60% Fewer Hallucinations
Browse by: Latest US Patents, China's latest patents, Technical Efficacy Thesaurus, Application Domain, Technology Topic, Popular Technical Reports.
© 2025 PatSnap. All rights reserved.Legal|Privacy policy|Modern Slavery Act Transparency Statement|Sitemap|About US| Contact US: help@patsnap.com