Water-saving and energy-saving cashmere dye vat and dyeing process
A cashmere and energy-saving technology, which is applied in the field of cashmere water-saving and energy-saving dyeing vats and dyeing processes, can solve the problems of increasing two-type hair, reducing the profit of cashmere products, and cashmere fiber variation, so as to improve penetration, The effect of improving the dyeing rate and dyeing uniformity
- Summary
- Abstract
- Description
- Claims
- Application Information
AI Technical Summary
Problems solved by technology
Method used
Image
Examples
Embodiment Construction
[0019] like figure 2 The cashmere water-saving and energy-saving dye vat shown includes a dye vat tank 2 and a hanging basket 1 arranged in the dye vat tank 2; a central tube 3 is arranged in the middle of the hanging basket 1; goats are arranged on both sides of the central tube 3. Cashmere placement area 4; around the hanging basket 1, an external dye solution circulation hole 6 is arranged outside the cashmere placement area 4; an internal dye solution circulation hole is arranged around the central tube 3 and inside the cashmere placement area 4 5; the distribution density of the internal dyeing liquid circulation holes 5 is higher than the distribution density of the external dyeing liquid circulation holes 6; the total area of the distribution of the internal dyeing liquid circulation holes 5 is smaller than the total area of the distribution of the external dyeing liquid circulation holes 6 ; The central tube 3 is provided with a closed hollow part 7 .
[0020] Th...
PUM
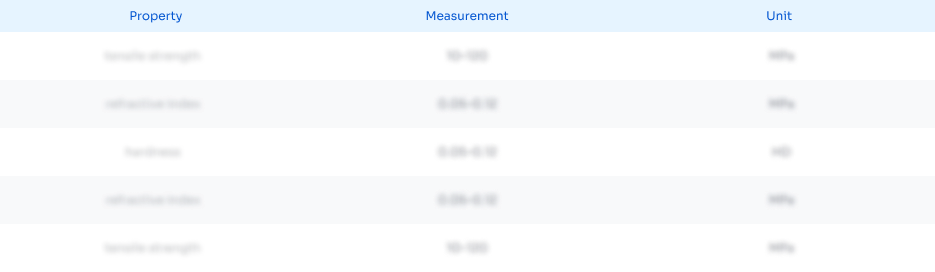
Abstract
Description
Claims
Application Information

- R&D
- Intellectual Property
- Life Sciences
- Materials
- Tech Scout
- Unparalleled Data Quality
- Higher Quality Content
- 60% Fewer Hallucinations
Browse by: Latest US Patents, China's latest patents, Technical Efficacy Thesaurus, Application Domain, Technology Topic, Popular Technical Reports.
© 2025 PatSnap. All rights reserved.Legal|Privacy policy|Modern Slavery Act Transparency Statement|Sitemap|About US| Contact US: help@patsnap.com