Recycled aggregate mountain flour anti-seismic hollow block for masonry frame filled wall and preparation method thereof
A technology of recycled aggregates and hollow blocks, which is applied in buildings, building components, building structures, etc., can solve the problem of less research reports on seismic performance, and achieve the effect of improving shear resistance.
- Summary
- Abstract
- Description
- Claims
- Application Information
AI Technical Summary
Problems solved by technology
Method used
Image
Examples
preparation example Construction
[0028] The present invention also provides a method for preparing recycled aggregate stone powder anti-seismic hollow blocks for masonry frame filling walls. The specific steps are as follows:
[0029] First, mix cement, stone powder, and fine aggregates by wheel milling, and then add polycarboxylate high-efficiency water reducer and water, and keep stirring until the cement slurry can completely cover the fine aggregate particles; then add Regenerate coarse aggregate, and continue to add the remaining polycarboxylate high-efficiency water reducer and water, and make dry recycled aggregate stone powder concrete after forced mixing, and send dry recycled aggregate stone powder concrete to the hydraulic molding machine in batches , the semi-finished product can be obtained by high-frequency vibration and pressure molding; after the semi-finished product is left to stand for 12-24 hours, and then autoclaved for 10-12 hours, a recycled aggregate stone powder anti-seismic hollow mas...
Embodiment 1
[0044] First, mix cement, stone powder, and fine aggregates by wheel milling, and then add polycarboxylate high-efficiency water reducer and water, and keep stirring until the cement slurry can completely cover the fine aggregate particles; then add Regenerate coarse aggregate, and continue to add the remaining polycarboxylate high-efficiency water reducer and water, and make dry recycled aggregate stone powder concrete after forced mixing, and send dry recycled aggregate stone powder concrete to the hydraulic molding machine in batches , the semi-finished product can be obtained by high-frequency vibration and pressure molding; after the semi-finished product is left to stand for 12-24 hours, and then autoclaved for 10-12 hours, a recycled aggregate stone powder anti-seismic hollow masonry can be produced for building frame-filled walls finished block.
[0045] The mass ratio of the cement, recycled coarse aggregate, stone powder, fine aggregate and water is 1:4.75:0.80:2.85:...
Embodiment 2
[0050] It is basically the same as Example 1, the difference is:
[0051] The mass ratio of the cement, recycled coarse aggregate, stone powder, fine aggregate and water is 1:2.95:0.60:2.65:0.35.
[0052] The polycarboxylic acid high-efficiency water-reducer is self-made AMPS modified polyacrylic acid high-efficiency water-reducer, and its dosage is 0.60% of the cement mass.
[0053] n (polyethylene glycol monomethyl ether acrylate): n (sodium methacrylate): n (sodium 2-acrylamide-2-methyl propylene sulfonate): n (acrylic acid) = 1.0: 2.5: 1.0 : 7.0, the MPEG relative molecular weight is 1200, the amount of initiator APS is 6% of the total mass of the mixed monomer solution, the polymerization reaction temperature is 90°C and the polymerization reaction time is 3.5h.
PUM
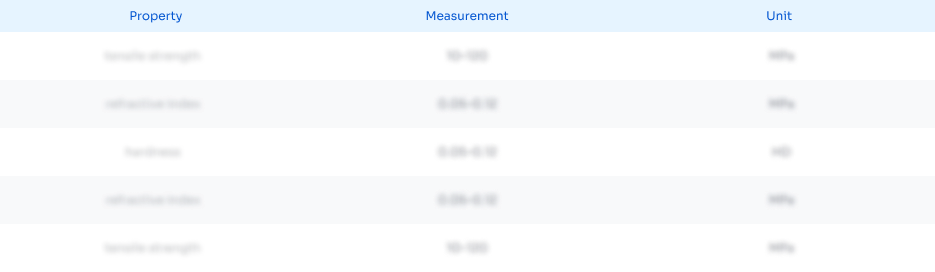
Abstract
Description
Claims
Application Information

- R&D
- Intellectual Property
- Life Sciences
- Materials
- Tech Scout
- Unparalleled Data Quality
- Higher Quality Content
- 60% Fewer Hallucinations
Browse by: Latest US Patents, China's latest patents, Technical Efficacy Thesaurus, Application Domain, Technology Topic, Popular Technical Reports.
© 2025 PatSnap. All rights reserved.Legal|Privacy policy|Modern Slavery Act Transparency Statement|Sitemap|About US| Contact US: help@patsnap.com