Alloy welding flux, preparation method thereof and application thereof
A solder and alloy technology, which is applied in the field of photovoltaic cell welding technology and alloy solder, can solve problems such as not being able to meet lamination welding requirements, achieve excellent welding performance and electrical performance, reduce production energy consumption, and reduce operating steps.
- Summary
- Abstract
- Description
- Claims
- Application Information
AI Technical Summary
Problems solved by technology
Method used
Image
Examples
Embodiment 1
[0055] S1: Use an electronic balance to weigh 317g of tin, 310g of lead, and 366g of bismuth, add the weighed tin, lead, and bismuth into a graphite crucible, and use a vacuum melting furnace to heat and melt the tin, lead, and bismuth in vacuum. Vacuum heating and smelting includes adjusting the vacuum degree to -0.1~0.1MPa, setting the heating temperature to 500°C for heating, and heating the tin, lead and bismuth to 500°C together to be in a completely molten state, and then keeping it warm for 30 minutes. The mixture of tin, lead and bismuth is taken out and poured into a mold for cooling to obtain the first component.
[0056] S2: Divide the first component into six equal parts, take one part and add 1g of indium, add the first component with indium into the graphite crucible, use a vacuum melting furnace The first component is smelted under vacuum heating. Vacuum heating and smelting includes adjusting the vacuum degree to -0.1-0.1MPa, setting the heating temperature to...
Embodiment 2
[0066] S1: Use an electronic balance to weigh 300g of tin, 380g of lead, and 315g of bismuth, add the weighed tin, lead, and bismuth into a graphite crucible, and use a vacuum melting furnace to heat and melt the tin, lead, and bismuth in a vacuum. Vacuum heating and smelting includes adjusting the vacuum degree to -0.1~0.1MPa, setting the heating temperature to 500°C for heating, and heating the tin, lead and bismuth to 500°C together to be in a completely molten state, and then keeping it warm for 30 minutes. The mixture of tin, lead and bismuth is taken out and poured into a mold for cooling to obtain the first component.
[0067] S2: Divide the first component into five equal parts, take one part and add 2g of indium, add the first component with indium into the graphite crucible, use a vacuum melting furnace to The first component is smelted under vacuum heating. Vacuum heating and smelting includes adjusting the vacuum degree to -0.1-0.1MPa, setting the heating temperat...
Embodiment 3
[0076] S1: Use an electronic balance to weigh 285g of tin, 430g of lead, and 280.2g of bismuth, add the weighed tin, lead, and bismuth into the graphite crucible, and use a vacuum melting furnace to heat and melt the tin, lead, and bismuth in a vacuum . Vacuum heating and smelting includes adjusting the vacuum degree to -0.1~0.1MPa, setting the heating temperature to 500°C for heating, and heating the tin, lead and bismuth to 500°C together to be in a completely molten state, and then keeping it warm for 30 minutes. The mixture of tin, lead and bismuth is taken out and poured into a mold for cooling to obtain the first component.
[0077] S2: Divide the first component into five equal parts, take one part and add 1g of indium, add the first component with indium into the graphite crucible, use a vacuum melting furnace to The first component is smelted under vacuum heating. Vacuum heating and smelting includes adjusting the vacuum degree to -0.1-0.1MPa, setting the heating te...
PUM
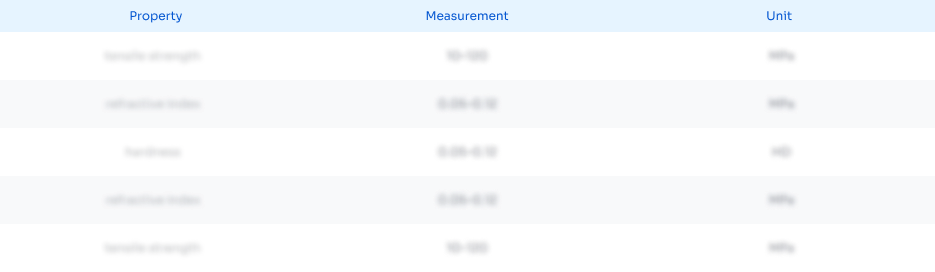
Abstract
Description
Claims
Application Information

- Generate Ideas
- Intellectual Property
- Life Sciences
- Materials
- Tech Scout
- Unparalleled Data Quality
- Higher Quality Content
- 60% Fewer Hallucinations
Browse by: Latest US Patents, China's latest patents, Technical Efficacy Thesaurus, Application Domain, Technology Topic, Popular Technical Reports.
© 2025 PatSnap. All rights reserved.Legal|Privacy policy|Modern Slavery Act Transparency Statement|Sitemap|About US| Contact US: help@patsnap.com