Method for treatment on high-voltage Ni-Co-Mn ternary positive electrode material by surface drying method
A ternary material, dry processing technology, applied in the direction of electrical components, battery electrodes, circuits, etc., can solve the problems of poor process controllability, impact on the capacity of ternary materials, complex process, etc., to achieve high batch stability, Taking into account the effect of recycling and reducing the amount of residual lithium
- Summary
- Abstract
- Description
- Claims
- Application Information
AI Technical Summary
Problems solved by technology
Method used
Image
Examples
Embodiment 1
[0018] Step 1, preparation of highly dispersed nickel-cobalt-manganese ternary material matrix:
[0019] Mixing: sieve and disperse the lithium salt with 70 meshes, remove slag and mix with nickel-cobalt-manganese hydroxide at a molar ratio of 1.05:1, add it to a mixer with a speed of 500n / min, and mix thoroughly for 1.5 hours to obtain mixed cornstarch;
[0020] Sintering: Put the mixed raw powder into a crucible and compact it, and sinter it in an air sintering furnace with a temperature of 960°C for 8 hours, then lower the temperature to a furnace temperature ≤80°C, take out the powder, and carry out weak crushing, dispersion, and passing through a 300-mesh sieve in the drying room After treatment, a highly dispersed nickel-cobalt-manganese ternary material matrix can be obtained.
[0021] Step 2, dry surface coating treatment:
[0022] Mixing materials: highly dispersed nickel-cobalt-manganese ternary material matrix and coating agent A are weighed at a molar ratio of 1:...
Embodiment 2
[0025] Step 1, preparation of highly dispersed nickel-cobalt-manganese ternary material matrix:
[0026] Mixing: sieve and disperse the lithium salt with 100 meshes, remove slag and mix it with nickel-cobalt-manganese hydroxide at a molar ratio of 1.08:1, add it into a mixer with a rotation speed of 600n / min, and fully mix for 1 hour to obtain mixed cornstarch;
[0027] Sintering: Put the mixed raw powder into a crucible and compact it, and sinter it in an air sintering furnace at a temperature of 940°C for 12 hours, then lower the temperature to a furnace temperature ≤80°C, take out the powder, and carry out weak crushing, dispersion, and passing through 300 meshes in the drying room After sieve treatment, a highly dispersed nickel-cobalt-manganese ternary material matrix is obtained.
[0028] Step 2, dry surface coating treatment:
[0029] Mixing: Highly dispersed nickel-cobalt-manganese ternary material matrix and coating agent A are weighed at a molar ratio of 1:0.03, ...
Embodiment 3
[0032] Step 1, preparation of highly dispersed nickel-cobalt-manganese ternary material matrix:
[0033] Mixing: sieve and disperse the lithium salt with a 150-mesh sieve, remove the slag and mix it with nickel-cobalt-manganese hydroxide at a molar ratio of 1.1:1, add it into a mixer with a rotation speed of 400n / min, and mix thoroughly for 2 hours to obtain mixed cornstarch;
[0034] Sintering: Put the mixed raw powder into a crucible and compact it, and sinter it in an air sintering furnace at a temperature of 910°C for 15 hours, then cool down to a temperature of ≤80°C, take out the powder, and carry out weak crushing, dispersion, and passing through 300 meshes in the drying room After sieve treatment, a highly dispersed nickel-cobalt-manganese ternary material matrix is obtained.
[0035] Step 2, dry surface coating treatment:
[0036] Mixing: the highly dispersed nickel-cobalt-manganese ternary material matrix and the coating agent A are weighed in a molar ratio of 1:...
PUM
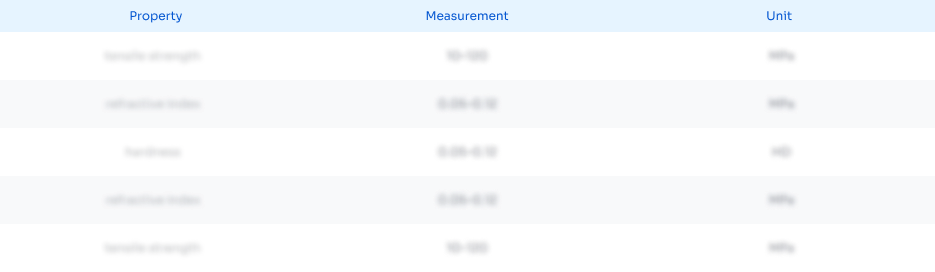
Abstract
Description
Claims
Application Information

- Generate Ideas
- Intellectual Property
- Life Sciences
- Materials
- Tech Scout
- Unparalleled Data Quality
- Higher Quality Content
- 60% Fewer Hallucinations
Browse by: Latest US Patents, China's latest patents, Technical Efficacy Thesaurus, Application Domain, Technology Topic, Popular Technical Reports.
© 2025 PatSnap. All rights reserved.Legal|Privacy policy|Modern Slavery Act Transparency Statement|Sitemap|About US| Contact US: help@patsnap.com