Manufacturing method of screw
A technology for screws and screw blanks, which is applied in the processing field of alloy materials, can solve the problems of heavy weight, general quality, and high cost of materials, and achieve the effects of prolonging service life, improving strength, and good mechanical properties
- Summary
- Abstract
- Description
- Claims
- Application Information
AI Technical Summary
Problems solved by technology
Method used
Image
Examples
Embodiment 1
[0027] The raw materials with the composition and mass percentages in Example 1 in Table 1 were weighed respectively to make steel products.
[0028] The steel is first subjected to isothermal normalizing treatment. The temperature of isothermal normalizing treatment is 950°C, and the temperature is kept for 200 minutes. Carbon treatment and tempering treatment, the carburizing treatment is to first raise the temperature to 910°C, keep it for 70min, then drop it to 900°C, keep it for 30min, then drop it to 840°C, keep it for 20min, and finally air cool to room temperature; The treatment temperature is 180°C, and the tempering treatment time is 100min.
[0029]The screw blanks are degreased and derusted sequentially (the temperature of degreasing and derusting treatment is 50°C, the treatment time is 5min, and the treatment liquid used is: thiourea 3.5g / L, sodium dihydrogen phosphate 3g / L, OP- 1012ml / L), activation treatment (the treatment liquid that activation treatment adop...
Embodiment 2
[0031] Weigh the raw materials with the composition and their mass percentages as shown in Table 1, Example 2, respectively, to make steel products.
[0032] The steel is first subjected to isothermal normalizing treatment. The temperature of isothermal normalizing treatment is 945°C, and the heat preservation time is 210min. Carbon treatment and tempering treatment, the carburizing treatment is to first raise the temperature to 895 ° C, keep it for 85 minutes, then drop it to 885 ° C, keep it for 45 minutes, then drop it to 825 ° C, keep it for 35 minutes, and finally air cool to room temperature; The treatment temperature is 155° C., and the tempering treatment time is 130 minutes.
[0033] The screw blanks are degreased and derusted sequentially (the temperature of degreasing and derusting treatment is 35°C, the treatment time is 8min, and the treatment liquid used is: thiourea 2.8g / L, sodium dihydrogen phosphate 7g / L, OP- 106ml / L), activation treatment (the treatment liqu...
Embodiment 3
[0035] Weigh the raw materials with the composition and mass percentages in Example 3 in Table 1, respectively, to make steel products.
[0036] The steel is first subjected to isothermal normalizing treatment. The temperature of isothermal normalizing treatment is 940°C, and the heat preservation time is 225 minutes. Carbon treatment and tempering treatment, the carburizing treatment is to first raise the temperature to 900°C, hold for 80min, then drop to 890°C, hold for 40min, then drop to 830°C, hold for 30min, and finally air cool to room temperature; The treatment temperature is 160° C., and the tempering treatment time is 120 minutes.
[0037] The screw blanks are degreased and derusted sequentially (the temperature for degreasing and derusting treatment is 40°C, the treatment time is 8min, and the treatment liquid used is: thiourea 3.0g / L, sodium dihydrogen phosphate 6g / L, OP- 108ml / L), activation treatment (the treatment liquid that activation treatment adopts is: nit...
PUM
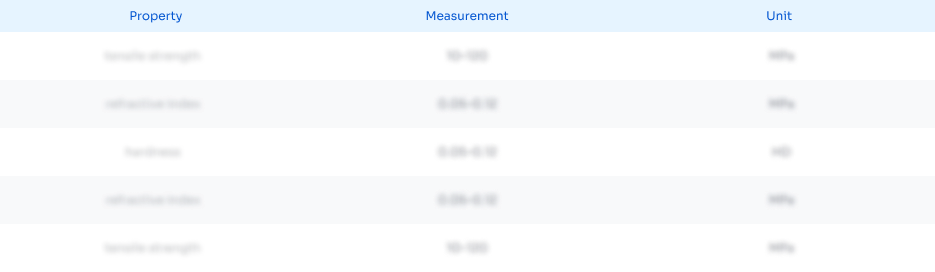
Abstract
Description
Claims
Application Information

- R&D
- Intellectual Property
- Life Sciences
- Materials
- Tech Scout
- Unparalleled Data Quality
- Higher Quality Content
- 60% Fewer Hallucinations
Browse by: Latest US Patents, China's latest patents, Technical Efficacy Thesaurus, Application Domain, Technology Topic, Popular Technical Reports.
© 2025 PatSnap. All rights reserved.Legal|Privacy policy|Modern Slavery Act Transparency Statement|Sitemap|About US| Contact US: help@patsnap.com