Solvent-free organic silicon release agent and preparation method thereof
A silicone, solvent-free technology, applied in the direction of coating, etc., can solve the problems of endangering human health, safety problems, environmental pollution, etc., and achieve the effects of low production cost, easy peeling, and simple preparation method
- Summary
- Abstract
- Description
- Claims
- Application Information
AI Technical Summary
Problems solved by technology
Method used
Examples
Embodiment 1
[0013] A solvent-free silicone release agent, comprising in parts by weight: 45 parts of vinyl-terminated polydimethylsiloxane, 45 parts of vinyl-terminated polymethylvinylsiloxane, and 1 part of sodium methyl silicate , 1 part of ethyl sodium silicate, 1 part of methyl hydrogen silicone oil, 1 part of acrylic acid, 1 part of sodium chloroplatinate, 2 parts of 1,3-divinyltetramethyldisiloxane, 1 part of sodium bicarbonate , 5 parts of ethanol, 1 part of methyl salicylate, 1 part of pentaerythritol, and 0.1 part of diphenylamine.
[0014] The preparation method of the above-mentioned solvent-free silicone stripping agent is as follows: first mix sodium chloroplatinate, 1,3-divinyltetramethyldisiloxane, sodium bicarbonate and ethanol, heat to 70°C and stir for 10 minutes, wait for After cooling the resulting mixture to 25°C, add vinyl-terminated polydimethylsiloxane, vinyl-terminated polymethylvinylsiloxane, sodium methyl silicate, sodium ethyl silicate, methyl hydrogen silicone...
Embodiment 2
[0016] A solvent-free silicone release agent, comprising in parts by weight: 47 parts of vinyl-terminated polydimethylsiloxane, 47 parts of vinyl-terminated polymethylvinylsiloxane, and 1.5 parts of sodium methyl silicate , 1.5 parts of sodium ethyl silicate, 1.5 parts of methyl hydrogen silicone oil, 1.5 parts of acrylic acid, 1.2 parts of sodium chloroplatinate, 2.5 parts of 1,3-divinyltetramethyldisiloxane, 1.2 parts of sodium bicarbonate , 6 parts of ethanol, 1.2 parts of methyl salicylate, 1.2 parts of pentaerythritol, and 0.2 parts of diphenylamine.
[0017] The preparation method of the above-mentioned solvent-free silicone stripping agent is as follows: first mix sodium chloroplatinate, 1,3-divinyltetramethyldisiloxane, sodium bicarbonate and ethanol, heat to 72°C and stir for 12 minutes, wait for After cooling the resulting mixture to 27°C, add vinyl-terminated polydimethylsiloxane, vinyl-terminated polymethylvinylsiloxane, sodium methyl silicate, sodium ethyl silicat...
Embodiment 3
[0019] A solvent-free silicone release agent, comprising in parts by weight: 53 parts of vinyl-terminated polydimethylsiloxane, 53 parts of vinyl-terminated polymethylvinylsiloxane, and 2.5 parts of sodium methyl silicate , 2.5 parts of ethyl sodium silicate, 2.5 parts of methyl hydrogen silicone oil, 2.5 parts of acrylic acid, 1.8 parts of sodium chloroplatinate, 3.5 parts of 1,3-divinyltetramethyldisiloxane, 1.8 parts of sodium bicarbonate , 9 parts of ethanol, 1.8 parts of methyl salicylate, 1.8 parts of pentaerythritol, and 0.4 parts of diphenylamine.
[0020] The preparation method of the above-mentioned solvent-free silicone stripping agent is as follows: first mix sodium chloroplatinate, 1,3-divinyltetramethyldisiloxane, sodium bicarbonate and ethanol, heat to 78°C and stir for 18 minutes, wait for After cooling the resulting mixture to 33°C, add vinyl-terminated polydimethylsiloxane, vinyl-terminated polymethylvinylsiloxane, sodium methyl silicate, sodium ethyl silicat...
PUM
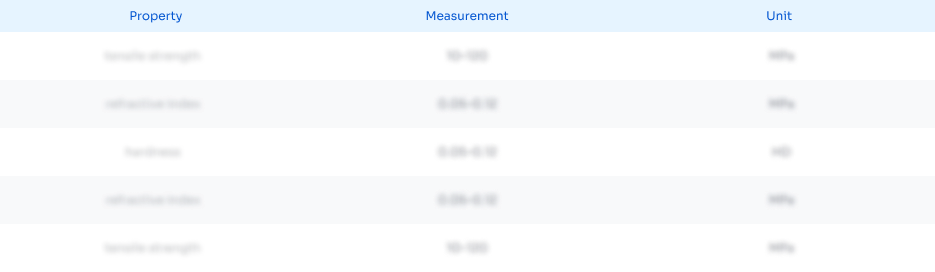
Abstract
Description
Claims
Application Information

- Generate Ideas
- Intellectual Property
- Life Sciences
- Materials
- Tech Scout
- Unparalleled Data Quality
- Higher Quality Content
- 60% Fewer Hallucinations
Browse by: Latest US Patents, China's latest patents, Technical Efficacy Thesaurus, Application Domain, Technology Topic, Popular Technical Reports.
© 2025 PatSnap. All rights reserved.Legal|Privacy policy|Modern Slavery Act Transparency Statement|Sitemap|About US| Contact US: help@patsnap.com