A preparing method of an environmental friendly flame-retardant polycarbonate composite material
A technology of flame-retardant polycarbonate and composite materials, applied in the field of polycarbonate, can solve the problems of unsatisfactory heat resistance and flame retardancy, low flame retardancy and heat resistance, etc.
- Summary
- Abstract
- Description
- Claims
- Application Information
AI Technical Summary
Problems solved by technology
Method used
Examples
Embodiment 1
[0018] The preparation method of a kind of environment-friendly heat-resistant flame-retardant polycarbonate composite material proposed by the present invention comprises the following steps:
[0019] S1, 20 parts by weight of nano-zinc oxide, 5 parts of nano-titanium dioxide, 2 parts of nano-aluminum hydroxide, 10 parts of glass fiber, 5 parts of kaolin, 10 parts of nano-zinc stannate, 1 part of ferrocene, 5 parts of molybdic acid Add zinc, 0.5 parts of basic sodium aluminum carbonate, 5 parts of calcium stearate, 3 parts of zinc stearate, and 2.5 parts of silane coupling agent KH-540 into 20 parts of ethanol, stir for 50 minutes, filter and dry to obtain modified fillers;
[0020] S2, by weight, 10 parts of polyvinyl butyral, 10 parts of polyvinylidene fluoride, 1 part of octafluorobiphenyl diglycidyl ether, 5 parts of styrene-acrylonitrile copolymer, 1 part of melamine resin and 50 parts The modified filler is melted and extruded in a twin-screw extruder to obtain a disper...
Embodiment 2
[0023] The preparation method of a kind of environment-friendly heat-resistant flame-retardant polycarbonate composite material proposed by the present invention comprises the following steps:
[0024] S1, by weight 35 parts of nano-zinc oxide, 1 part of nano-titanium dioxide, 10 parts of nano-aluminum hydroxide, 5 parts of glass fiber, 15 parts of kaolin, 2 parts of nano-zinc stannate, 5 parts of ferrocene, 2 parts of molybdic acid Add zinc, 2 parts of basic sodium aluminum carbonate, 2 parts of calcium stearate, 5 parts of zinc stearate, and 1 part of silane coupling agent KH-540 into 35 parts of ethanol, stir for 20 minutes, filter and dry to obtain the modified filler;
[0025] S2, by weight 25 parts of polyvinyl butyral, 5 parts of polyvinylidene fluoride, 5 parts of octafluorobiphenyl diglycidyl ether, 2 parts of styrene-acrylonitrile copolymer, 5 parts of melamine resin and 25 parts The modified filler is melted and extruded in a twin-screw extruder to obtain a disperse...
Embodiment 3
[0028] The preparation method of a kind of environment-friendly heat-resistant flame-retardant polycarbonate composite material proposed by the present invention comprises the following steps:
[0029] S1, by weight 28 parts of nano-zinc oxide, 3.8 parts of nano-titanium dioxide, 6 parts of nano-aluminum hydroxide, 7 parts of glass fiber, 8 parts of kaolin, 7 parts of nano-zinc stannate, 2.8 parts of ferrocene, 3.8 parts of molybdic acid Add zinc, 1 part of basic sodium aluminum carbonate, 4 parts of calcium stearate, 3.5 parts of zinc stearate, and 2.5 parts of silane coupling agent KH-540 into 28 parts of ethanol, stir for 40 minutes, filter and dry to obtain the modified filler;
[0030] S2, by weight 15 parts of polyvinyl butyral, 8 parts of polyvinylidene fluoride, 2.8 parts of octafluorobiphenyl diglycidyl ether, 3.7 parts of styrene-acrylonitrile copolymer, 3.2 parts of melamine resin and 45 parts The modified filler is melted and extruded in a twin-screw extruder to ob...
PUM
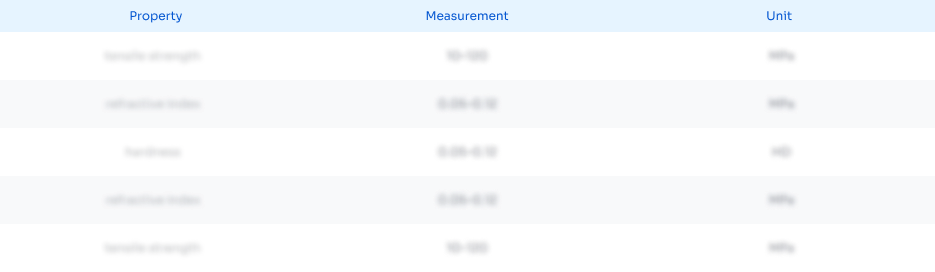
Abstract
Description
Claims
Application Information

- R&D Engineer
- R&D Manager
- IP Professional
- Industry Leading Data Capabilities
- Powerful AI technology
- Patent DNA Extraction
Browse by: Latest US Patents, China's latest patents, Technical Efficacy Thesaurus, Application Domain, Technology Topic, Popular Technical Reports.
© 2024 PatSnap. All rights reserved.Legal|Privacy policy|Modern Slavery Act Transparency Statement|Sitemap|About US| Contact US: help@patsnap.com