More than 99% alumina granulated powder for cold isostatic pressing and preparation method thereof
A technology for alumina and granulated powder, applied in the field of alumina ceramics, can solve the problems of poor post-processing performance and low green density, and achieve good application prospects, low cost, and good toughness.
- Summary
- Abstract
- Description
- Claims
- Application Information
AI Technical Summary
Problems solved by technology
Method used
Image
Examples
Embodiment 1
[0019] The ball mill adopts an octagonal ball mill. Put 150Kg of high-alumina alumina balls (specifications Φ6, Φ8, Φ12 (mm) according to the mass ratio of 3:3:4) in the barrel, and put 100KgCT-3000SG, 50Kg deionized water, 200g Yttrium oxide, 400g magnesium oxide, 600g D-134 were ball milled for 46 hours, and 2kg P-222 was added for ball milling for 1.5 hours before the slurry was discharged. After the slurry was discharged, it was filtered with an 80-mesh screen, and the slurry was put into the mixing tank and stirred through the magnet.
[0020] Start the centrifugal spray granulator, set the inlet temperature to 220°C, the outlet temperature to 95°C, the rotation speed to 15000rpm, and the negative pressure to 120pa.
[0021] The granulated powder is sieved with 60 mesh and 325 mesh to remove coarse and fine particles. The powder must be iron-removed to remove impurities, and the powder is homogenized for 24 hours using a cold isostatic rubber mold to make a billet.
[002...
Embodiment 2
[0026] The ball mill adopts an octagonal ball mill. Put 100Kg of high-alumina alumina balls of more than 99% in the bucket (specifications Φ6, Φ8, Φ12 (mm) according to the mass ratio 3:3:4), and put in 50Kg CT-3000SG, 80Kg deionized water, 400g of yttrium oxide, 800g of magnesia, 200g of D-134 were ball milled for 40 hours, and 3kg of P-222 was added for ball milling for 1 hour before the slurry was discharged. After the slurry was discharged, it was filtered with an 80-mesh screen, and the slurry was put into a mixing tank for stirring through a magnet.
[0027] Start the centrifugal spray granulator, set the inlet temperature to 220°C, the outlet temperature to 95°C, the rotation speed to 15000rpm, and the negative pressure to 120pa.
[0028] The granulated powder is sieved with 60 mesh and 325 mesh to remove coarse and fine particles. The powder must be iron-removed to remove impurities, and the powder is homogenized for 28 hours using a cold isostatic rubber mold to make a...
Embodiment 3
[0032] The ball mill adopts an octagonal ball mill. Put 150Kg of high-alumina alumina balls above 99% in the bucket (specifications Φ6, Φ8, Φ12 (mm) according to the mass ratio 3:3:4), and put 150Kg CT-3000SG, 150Kg deionized water, 100g of yttrium oxide, 200g of magnesia, 600g of D-134 were ball milled for 50 hours, and 1kg of P-222 was added for ball milling for 3 hours before the slurry was discharged. After the slurry was discharged, it was filtered with an 80-mesh screen, and the slurry was put into a mixing tank and stirred through a magnet.
[0033] Start the centrifugal spray granulator, set the inlet temperature to 220°C, the outlet temperature to 95°C, the rotation speed to 15000rpm, and the negative pressure to 120pa.
[0034] The granulated powder is sieved with 60 mesh and 325 mesh to remove coarse and fine particles. The powder must be iron-removed to remove impurities, and the powder is homogenized for 36 hours using a cold isostatic rubber mold to make a billet....
PUM
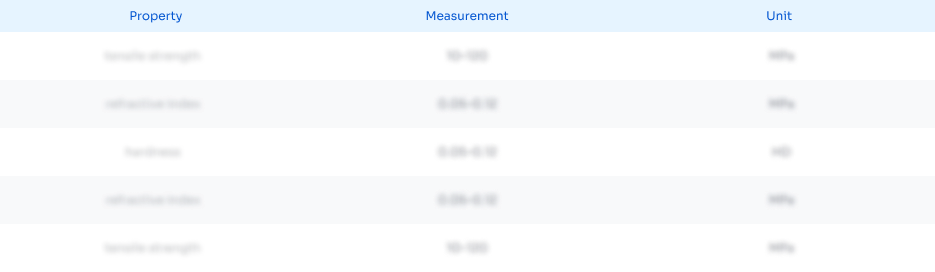
Abstract
Description
Claims
Application Information

- R&D
- Intellectual Property
- Life Sciences
- Materials
- Tech Scout
- Unparalleled Data Quality
- Higher Quality Content
- 60% Fewer Hallucinations
Browse by: Latest US Patents, China's latest patents, Technical Efficacy Thesaurus, Application Domain, Technology Topic, Popular Technical Reports.
© 2025 PatSnap. All rights reserved.Legal|Privacy policy|Modern Slavery Act Transparency Statement|Sitemap|About US| Contact US: help@patsnap.com