Probe system multi-filed loading device
A technology of loading devices and probes, applied in the directions of measuring devices, instruments, scientific instruments, etc., can solve the problems of easy mutual influence, damage to electronic components, affecting the reliability, accuracy and precision of test results, and achieve reliable test results. , The effect of strong anti-interference ability of external environment
- Summary
- Abstract
- Description
- Claims
- Application Information
AI Technical Summary
Problems solved by technology
Method used
Image
Examples
Embodiment Construction
[0021] Below in conjunction with accompanying drawing, further describe the present invention through embodiment, but do not limit the scope of the present invention in any way.
[0022] The present invention provides a probe system multi-field loading device, in the embodiment of the present invention, such as figure 1 As shown, the multi-field loading device includes a multi-field loading box 1, a horizontal moving table 2, a transmission shaft 3, a servo motor 4 that drives the transmission shaft 3 to rotate, an exhaust pipe 6 connected to an external vacuum pump, and an exhaust pipe connected to an external humidity controller 7. Probe 8, cantilever rod 9, fixed bracket 10 with slide rail, transmission shaft 11, servo motor 12 that drives transmission shaft 11 to rotate, force sensor 13, electrode 14, threaded screw rod 15, annular heating rod 16, Temperature sensor 17, circular iron rod 18 and LED flat panel lamp 19 of annular winding copper wire; The material of a plural...
PUM
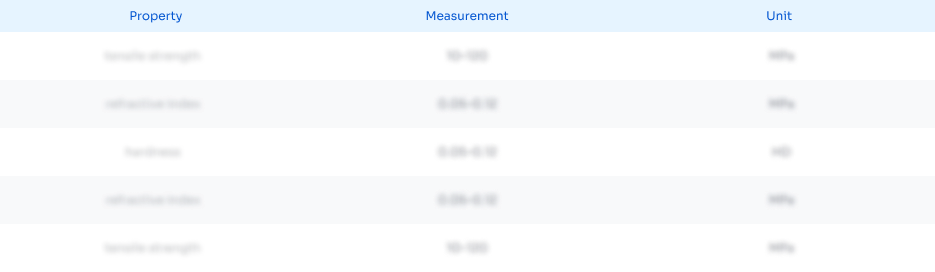
Abstract
Description
Claims
Application Information

- Generate Ideas
- Intellectual Property
- Life Sciences
- Materials
- Tech Scout
- Unparalleled Data Quality
- Higher Quality Content
- 60% Fewer Hallucinations
Browse by: Latest US Patents, China's latest patents, Technical Efficacy Thesaurus, Application Domain, Technology Topic, Popular Technical Reports.
© 2025 PatSnap. All rights reserved.Legal|Privacy policy|Modern Slavery Act Transparency Statement|Sitemap|About US| Contact US: help@patsnap.com