Environment-friendly coconut charcoal fiber composite friction material and manufacturing method for brake pad
A composite friction material, coconut carbon fiber technology, applied in the direction of friction linings, chemical instruments and methods, other chemical processes, etc., can solve the problems of high friction coefficient, scratched brake discs, loss of direction, etc., to achieve long life and extended use. The effect of life and short braking distance
- Summary
- Abstract
- Description
- Claims
- Application Information
AI Technical Summary
Problems solved by technology
Method used
Examples
Embodiment Construction
[0018] The friction material of the present invention includes resin, steel fiber, aramid fiber, coconut carbon fiber and petroleum coke, and the formula of its parts is resin: steel brazing fiber: aramid fiber: coconut carbon fiber: petroleum coke=5-15: 15-40: 1-8:5-35:3-18, made by mixing with a mixer.
[0019] The manufacturing method of the brake pad of the present invention is as follows: resin: steel brazing fiber: aramid fiber: coconut carbon fiber: petroleum coke = 5-15: 15-40: 1-8: 5-35: 3-18 parts formula The aramid fiber and coconut carbon fiber are mixed evenly in the high-speed mixer, and then the steel brazing fiber is put into the high-speed mixer and stirred together with the evenly mixed aramid fiber and coconut carbon fiber mixture. Stir petroleum coke, stir evenly, then add resin to stir, stir evenly, take out, select different brake pad molds according to the occasion of the brake pad, put the friction material in the brake pad mold to brake the brake pads....
PUM
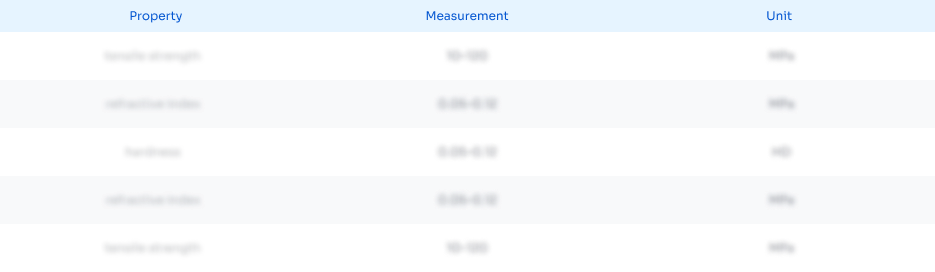
Abstract
Description
Claims
Application Information

- R&D
- Intellectual Property
- Life Sciences
- Materials
- Tech Scout
- Unparalleled Data Quality
- Higher Quality Content
- 60% Fewer Hallucinations
Browse by: Latest US Patents, China's latest patents, Technical Efficacy Thesaurus, Application Domain, Technology Topic, Popular Technical Reports.
© 2025 PatSnap. All rights reserved.Legal|Privacy policy|Modern Slavery Act Transparency Statement|Sitemap|About US| Contact US: help@patsnap.com