Modified fly ash for reinforcing rubber products and preparation method thereof
A technology for rubber products and fly ash, which is applied in the field of modified fly ash and its preparation, can solve the problems of insignificant treatment effect of metal oxides, insignificant improvement of material physical properties, and high cost of coupling agent treatment, and achieves reduction of Stress concentration and defects, improved mechanical properties, low cost effect
- Summary
- Abstract
- Description
- Claims
- Application Information
AI Technical Summary
Problems solved by technology
Method used
Image
Examples
Embodiment 1
[0034] Such as figure 1 A preparation method of modified fly ash for reinforcing rubber products is shown. Firstly, the fly ash, thermosetting resin solution and interface adhesive solution are prepared from the fly ash head tank, thermosetting resin solution head tank and interface adhesive respectively. The high level tank of the mixture is added to the respective automatic metering device through the pipeline for metering; firstly, 100 parts by weight of fly ash after metering are added into the reactor device through the pipeline; then 5 parts by weight of the metered The thermosetting resin solution, wherein the thermosetting resin solution is composed of raw materials and the weight ratio is: thermosetting resin: organic solvent = 100:150, the fly ash and the thermosetting resin solution are stirred and mixed in the reaction kettle for 5min, and then heated to 80°C After reacting and drying for 90 minutes, cool to room temperature to obtain the first coating of fly ash; ...
example 1
[0035] The application method of modified fly ash in rubber composite materials in Example 1 is calculated in parts by weight. Add 70 parts of natural rubber to the internal mixer and knead for 20 minutes, then add 30 parts of styrene-butadiene rubber and knead for 10 minutes, and then go to the compactor in turn. Add 1.3 parts of accelerator, 5 parts of zinc oxide, 2 parts of stearic acid, 2 parts of microcrystalline wax, 3 parts of antioxidant, 11 parts of process oil, 20 parts of carbon black, 35 parts of modified Fly ash and 0.7 parts of anti-scorch agent, and finally add 2.5 parts of sulfur, mix for 8 minutes, and make a sheet; make a modified coal ash rubber composite material.
Embodiment 2
[0037] Such as figure 1 A preparation method of modified fly ash for reinforcing rubber products is shown. Firstly, the fly ash, thermosetting resin solution and interface adhesive solution are prepared from the fly ash head tank, thermosetting resin solution head tank and interface adhesive respectively. The high level tank of the mixture is added to the respective automatic metering device through the pipeline for metering; firstly, 100 parts by weight of fly ash after metering are added into the reactor device through the pipeline; then 30 parts by weight of the metered The thermosetting resin solution, wherein the thermosetting resin solution is composed of raw materials and the weight ratio is, thermosetting resin: organic solvent = 100:400; the fly ash and the thermosetting resin solution are stirred and mixed in the reaction kettle for 20min, and then the temperature is raised to 120°C After reacting and drying for 30 minutes, cool to room temperature to obtain the firs...
PUM
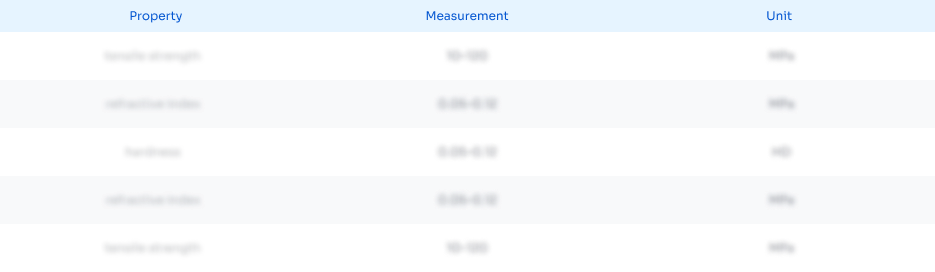
Abstract
Description
Claims
Application Information

- R&D Engineer
- R&D Manager
- IP Professional
- Industry Leading Data Capabilities
- Powerful AI technology
- Patent DNA Extraction
Browse by: Latest US Patents, China's latest patents, Technical Efficacy Thesaurus, Application Domain, Technology Topic, Popular Technical Reports.
© 2024 PatSnap. All rights reserved.Legal|Privacy policy|Modern Slavery Act Transparency Statement|Sitemap|About US| Contact US: help@patsnap.com