Method for producing high-salinity maritime work cement through mineral waste residue waste materials
A technology of marine cement and sulphoaluminate cement, which is applied in the direction of cement production, can solve the problems of inconvenient construction and engineering quality control, lack of uniform standards for preparation technology, unfavorable production and construction costs, etc., and achieve good compactness and volume Effects of stability, high resistance to chloride ion diffusion, and excellent durability
- Summary
- Abstract
- Description
- Claims
- Application Information
AI Technical Summary
Problems solved by technology
Method used
Image
Examples
Embodiment 1
[0033] A marine cement, comprising the following raw materials by weight: 30 parts of slag; 45 parts of sulfoaluminate cement clinker; 0.03 parts of composite activator; 4 parts of early strength agent; 0.3 part of water reducing agent; 0.005 part of air-entraining agent part; 0.4 part of retarder.
[0034] Described sulfoaluminate cement clinker is the sulfoaluminate cement clinker obtained by replacing bauxite production with low-grade bauxite or aluminum slag at 1:1; the main component is Al 2 O 3 , SiO 2 , CaO, Fe 2 O 3 , SO 3 , C 4 A 3 S, C 2 S, C 4 AF. Its chemical composition is mainly Al 2 O 3 (20%-40%), SiO 2 (2%-10%), Fe 2 O 3 (5%-15%), SO 3 (5%-15%), C 4 A 3 S(40%-65%), C 2 S(10%-30%), C 4 AF (20%-35%), CaO added to 100%.
[0035] The water reducing agent is sodium polynaphthalene sulfonate; the air-entraining agent is sodium secondary alkyl sulfonate; the retarder is hydroxycarboxylate;
Embodiment 2
[0044] A marine cement, comprising the following raw materials by weight: 35 parts of slag; 40 parts of sulfoaluminate cement clinker; 0.05 parts of composite activator; 3 parts of early strength agent; 0.4 part of water reducing agent; 0.007 part of air-entraining agent part; 0.3 part of retarder.
[0045] Described sulfoaluminate cement clinker is the sulfoaluminate cement clinker obtained by replacing bauxite production with low-grade bauxite or aluminum slag at 1:1; the main component is Al 2 O 3 , SiO 2 , CaO, Fe 2 O 3 , SO 3 , C 4 A 3 S, C 2 S, C 4 AF. Its chemical composition is mainly Al 2 O 3 (20%-40%), SiO 2 (2%-10%), Fe 2 O 3 (5%-15%), SO 3 (5%-15%), C 4 A 3 S(40%-65%), C 2 S(10%-30%), C 4 AF(20%-35%), CaCO 3 added to 100%;
[0046] The water reducing agent is sodium polynaphthalene sulfonate; the air-entraining agent is sodium secondary alkyl sulfonate; the retarder is hydroxycarboxylate;
Embodiment 3
[0055] A marine cement, comprising the following raw materials by weight: 40 parts of slag; 50 parts of sulfoaluminate cement clinker; 0.04 part of composite activator; 3 parts of early strength agent; 0.5 part of water reducing agent; 0.006 part of air-entraining agent part; 0.5 part of retarder.
[0056] The described sulfoaluminate cement clinker is the sulfoaluminate cement clinker obtained by replacing bauxite production with low-grade bauxite or aluminum slag at 1:1; the main components are Al2O3, SiO2, CaO, Fe2O3, SO3 , C4A3S, C2S, C4AF. Its chemical composition is mainly Al 2 O 3 (20%-40%), SiO 2 (2%-10%), CaO (30%-45%), Fe 2 O 3 (5%-15%), SO 3 (5%-15%), C 4 A 3 S(40%-65%), C 2 S(10%-30%), C 4 AF(20%-35%);
[0057] The water reducing agent is sodium polynaphthalene sulfonate; the air-entraining agent is sodium secondary alkyl sulfonate; the retarder is hydroxycarboxylate;
[0058] The slag is a kind of powder obtained by grinding blast furnace water slag, t...
PUM
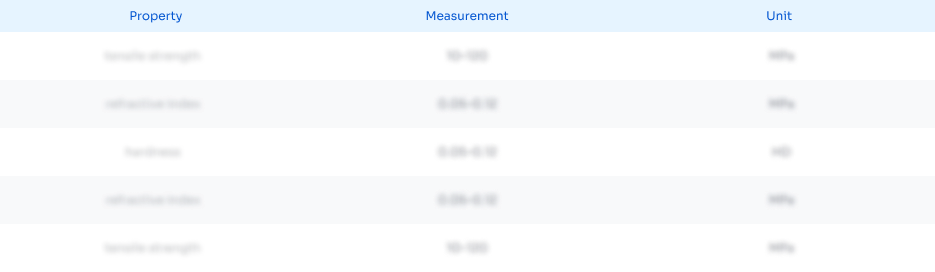
Abstract
Description
Claims
Application Information

- R&D Engineer
- R&D Manager
- IP Professional
- Industry Leading Data Capabilities
- Powerful AI technology
- Patent DNA Extraction
Browse by: Latest US Patents, China's latest patents, Technical Efficacy Thesaurus, Application Domain, Technology Topic, Popular Technical Reports.
© 2024 PatSnap. All rights reserved.Legal|Privacy policy|Modern Slavery Act Transparency Statement|Sitemap|About US| Contact US: help@patsnap.com