A method for comprehensive recovery of electroplating sludge
A technology of electroplating sludge and sodium carbonate, which is applied in the field of solid waste resource utilization, can solve the problems of poor applicability, poor treatment effect, and difficulty in industrialization, and achieve significant economic benefits, small amount of waste residue, and operability strong effect
- Summary
- Abstract
- Description
- Claims
- Application Information
AI Technical Summary
Problems solved by technology
Method used
Image
Examples
Embodiment 1
[0042] Mix 20g of electroplating sludge with 8g of sodium carbonate, place it in a muffle furnace for calcination, and calcine at 700°C for 3 hours. After washing, leaching and filtering, leachate and filter cake are obtained. Introducing CO into the leaching solution 2 Adding seed crystals, the seed crystal coefficient is 0.6, controlling the solution temperature to 70°C, and removing aluminum and a small amount of silicon in the solution. A reducing agent is added to the dealuminated sodium chromate solution to carry out a reduction reaction, and after the reaction, the slurry is filtered and washed to obtain a chromium hydroxide filter cake. The recovery rate of chromium is 95%, and the recovery rate of aluminum is 92%. The filter residue is leached with sulfuric acid at a ratio of acid / residue = 1.0 times, and the leached residue is iron-silicon slag. The leachate is removed to obtain ferric hydroxide. The impurity removal solution is extracted / back-extracted and crysta...
Embodiment 2
[0044] Mix 20g of electroplating sludge with 5g of sodium carbonate, place it in a muffle furnace for calcination, and calcine at 800°C for 2.5h. After washing, leaching and filtering, leachate and filter cake are obtained. Introducing CO into the leaching solution 2 And adding seed crystals, the seed crystal coefficient is 0.8, controlling the solution temperature to 50° C., and removing aluminum and a small amount of silicon in the solution. A reducing agent is added to the dealuminated sodium chromate solution to carry out a reduction reaction, and after the reaction, the slurry is filtered and washed to obtain a chromium hydroxide filter cake. The recovery rate of chromium is 99%, and the recovery rate of aluminum is 91%. The filter residue is leached with hydrochloric acid at a ratio of acid / residue = 3.0 times, and the leached residue is iron-silicon slag. The leachate is removed to obtain ferric hydroxide. The impurity removal solution is extracted / back-extracted and...
Embodiment 3
[0046] Mix 20g of electroplating sludge with 3g of sodium carbonate, place it in a muffle furnace for calcination, and calcine at 900°C for 2 hours. After washing, leaching and filtering, leachate and filter cake are obtained. Introducing CO into the leaching solution 2 And adding seed crystals, controlling the solution temperature to 30° C., the seed crystal coefficient to 0.3, and removing aluminum and a small amount of silicon in the solution. A reducing agent is added to the dealuminated sodium chromate solution to carry out a reduction reaction, and after the reaction, the slurry is filtered and washed to obtain a chromium hydroxide filter cake. Chromium recovery was 92% and aluminum recovery was 90%. The filter residue is leached with nitric acid according to the ratio of acid / residue = 2.0 times, and the leached residue is iron-silicon slag. The leachate is removed to obtain ferric hydroxide. The impurity removal solution is extracted / back-extracted and crystallized ...
PUM
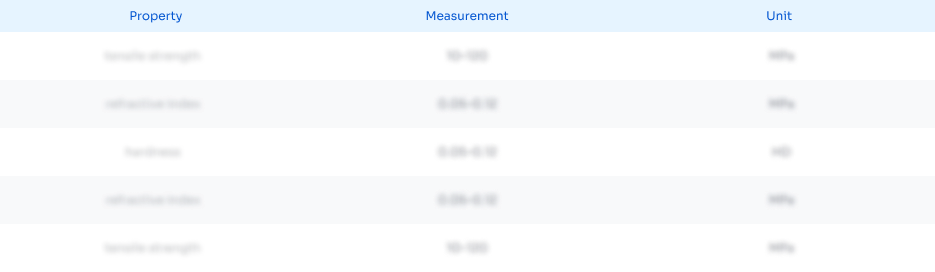
Abstract
Description
Claims
Application Information

- R&D
- Intellectual Property
- Life Sciences
- Materials
- Tech Scout
- Unparalleled Data Quality
- Higher Quality Content
- 60% Fewer Hallucinations
Browse by: Latest US Patents, China's latest patents, Technical Efficacy Thesaurus, Application Domain, Technology Topic, Popular Technical Reports.
© 2025 PatSnap. All rights reserved.Legal|Privacy policy|Modern Slavery Act Transparency Statement|Sitemap|About US| Contact US: help@patsnap.com