Silicone rubber nano composite with high tear resistance and preparation method thereof
A silicone rubber nano-composite technology, applied in the field of silicone rubber, can solve the problems of weak matrix interface, weak carbon nanotube force, uneven dispersion, etc.
- Summary
- Abstract
- Description
- Claims
- Application Information
AI Technical Summary
Problems solved by technology
Method used
Image
Examples
comparative example 1
[0017] Put 100 grams of silicone rubber with a vinyl content of 0.1-0.2% and a molecular weight of 550,000-600,000 on a double-roll mill at room temperature. After the rolls are stabilized, add 40 parts of fumed white carbon black and 5 parts of hydroxyl silicone oil. 1. 0.5 part of dicumyl peroxide, after fully mixing, thin pass 4 times to lower the sheet, then vulcanize on a flat vulcanizing machine with a temperature of 160°C and a pressure of 15MPa. The mechanical properties of the tested material are shown in Table 1:
comparative example 2
[0019] Put 100 grams of silicone rubber with a vinyl content of 0.1-0.2% and a molecular weight of 550,000-600,000 on a double-roll mill at room temperature. After the rolls are stabilized, add 30 parts of fumed white carbon black and 3 parts of hydroxyl silicone oil. , 5 parts of carbon nanotubes, 0.8 parts of 2,5-dimethyl-2,5-bis(tert-butylperoxy) hexane, after fully mixing, thin pass 4 times to lower the sheet, and then at a temperature of 170 ℃, and the pressure is 15MPa on a flat vulcanizing machine. The mechanical properties of the tested materials are shown in Table 1:
Embodiment example 1
[0021] Put 100 grams of silicone rubber with a vinyl content of 0.1-0.2% and a molecular weight of 550,000-600,000 on a double-roll mill at room temperature. After the rolls are stabilized, add dimethyldiphenylthiuram disulfide 0.6 50 parts of fumed white carbon black, 6 parts of hydroxy silicone oil, 3 parts of carbon nanotubes, 3.5 parts of benzoyl peroxide. Vulcanized on a 15MPa flat vulcanizing machine, the mechanical properties of the tested materials are shown in Table 1:
PUM
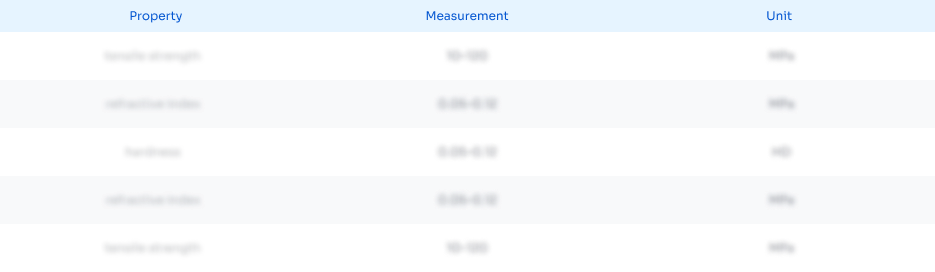
Abstract
Description
Claims
Application Information

- Generate Ideas
- Intellectual Property
- Life Sciences
- Materials
- Tech Scout
- Unparalleled Data Quality
- Higher Quality Content
- 60% Fewer Hallucinations
Browse by: Latest US Patents, China's latest patents, Technical Efficacy Thesaurus, Application Domain, Technology Topic, Popular Technical Reports.
© 2025 PatSnap. All rights reserved.Legal|Privacy policy|Modern Slavery Act Transparency Statement|Sitemap|About US| Contact US: help@patsnap.com