Prefabricated assembled steel-concrete composite structure pipeline and manufacturing method thereof
A prefabricated assembly and combined structure technology, applied in the direction of pipes, rigid pipes, pipes/pipe joints/pipe fittings, etc., can solve the problems of easy circumferential and axial deformation, large flexibility of the pipe body, and high installation requirements, so as to improve corrosion resistance And wear resistance, reduce stress concentration points, smooth internal flow resistance
- Summary
- Abstract
- Description
- Claims
- Application Information
AI Technical Summary
Problems solved by technology
Method used
Image
Examples
Embodiment 1
[0113] Example 1 The first embodiment of the prefabricated steel-concrete composite steel pipe with annular ribs
[0114] After derusting and shot-peening treatment of the main steel strip plate, use special rolling rail manufacturing equipment to roll the main steel strip that has been cut to the required size separately into a steel strip with protrusions; press the main steel strip, The plugging steel strips are arranged in order, and after being bonded to the main steel strip, the sealing steel strip and the main steel strip are welded by gas shielded welding, and the formed composite steel strip with a hollow cavity is sent to the rolling mechanism to obtain A tube body with ribs on the outer wall. Cut the pipe body to the required length, drill holes at both ends, weld the end flange, and then divide the steel pipe into corresponding unit plates in the circumferential direction. The unit plates have a certain radian and are welded on both sides The flat steel plate with...
Embodiment 2
[0115] Example 2 Implementation scheme of prefabricated assembled steel-concrete composite steel pipe with spiral ribs
[0116]Adjust the forming angle of the spiral forming machine to an appropriate value according to the diameter of the produced spiral welded steel pipe. After derusting and shot-peening treatment of the main steel strip, the main steel strip cut to the required size is rolled into a steel strip with protrusions by using special rolling rail manufacturing equipment. Arranged in the order of the main steel strip and the plugging steel strip, after being bonded to the main steel strip, use gas shielded welding to weld the plugging steel strip and the main steel strip to form a composite steel strip with a hollow cavity. Rolling mechanism to obtain a tube body with ribs on the outer wall. Cut the pipe body to the required length, drill holes at both ends, weld the end flange, and then divide the steel pipe into corresponding unit plates in the circumferential d...
Embodiment 3
[0117] Example 3 The second embodiment of the prefabricated steel-concrete composite steel pipe with annular ribs
[0118] After derusting and shot-peening treatment of the main steel strip plate, use special rolling rail manufacturing equipment to roll the main steel strip that has been cut to the required size separately into a steel strip with protrusions; then the main steel strip The first pair of sides is bent and opened to form an end flange; the main steel strip and the plugging steel strip are arranged in sequence, and after being bonded to the main steel strip, the sealing steel strip and the main steel strip are welded together by gas shielded welding. The plates are welded, and the formed composite steel strip with a hollow cavity is fed into the bending mechanism to obtain an arc-shaped unit plate with convex ribs on the outer surface and end flanges on both sides. Weld a flat steel plate with bolt holes (that is, a side flange) on the second opposite side of the ...
PUM
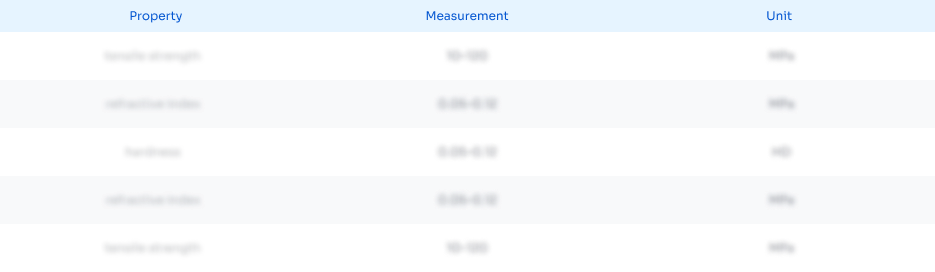
Abstract
Description
Claims
Application Information

- R&D Engineer
- R&D Manager
- IP Professional
- Industry Leading Data Capabilities
- Powerful AI technology
- Patent DNA Extraction
Browse by: Latest US Patents, China's latest patents, Technical Efficacy Thesaurus, Application Domain, Technology Topic, Popular Technical Reports.
© 2024 PatSnap. All rights reserved.Legal|Privacy policy|Modern Slavery Act Transparency Statement|Sitemap|About US| Contact US: help@patsnap.com