Composition for improving anti-pilling performance of all-cotton fabric and anti-pilling finishing technology
An anti-pilling, cotton fabric technology, applied in the processing of textile materials, continuous processing of textile materials, fabric surface trimming, etc., can solve the problem of affecting consumer comfort. The performance, feel and method cannot be completely satisfied, etc., to achieve the effect of improving gloss, good anti-pilling effect, and good shape retention.
- Summary
- Abstract
- Description
- Claims
- Application Information
AI Technical Summary
Problems solved by technology
Method used
Examples
Embodiment 1
[0027] Fabric specification: 105'' / 40s*40s / 144*76 satin reactive printing
[0028] The gray cloth is processed through the following steps in turn:
[0029] (1) Pre-treatment of gray cloth: Singeing → rolling enzyme cold stacking → scouring → bleaching → mercerizing → whitening of gray cloth in sequence; the singeing grade reaches grade 4 and above. The amount of hydrogen peroxide used in bleaching is 3-4g / L.
[0030] (2) Printing: the pre-treated semi-finished products are printed, steamed and washed in sequence;
[0031] (3) Finishing: Composition finishing, calendering, pre-shrinking steps.
[0032] The formula of the composition in step (3) is: 10%-12% of modified polyether emulsion, 6%-7% of amino fatty acid emulsion, 5%-8% of modified polysiloxane emulsion, acrylic modified polyurethane polymer The product emulsion is 12%-15%, the rest is water, and the pH value is adjusted to 4-5.5 with acetic acid.
[0033] The fabric is soaked and rolled once, with a liquid retent...
Embodiment 2
[0036] 105'' / 60s*60s / 200*100 satin reactive printing
[0037] The gray cloth is processed through the following steps in turn:
[0038] (1) Pre-treatment of gray cloth: Singeing → rolling enzyme cold stacking → scouring → bleaching → mercerizing → whitening of gray cloth in sequence; the singeing grade reaches grade 4 and above. The amount of hydrogen peroxide used in bleaching is 3-4g / L.
[0039] (2) Printing: the pre-treated semi-finished products are printed, steamed and washed in sequence;
[0040] (3) Finishing: Composition finishing, calendering, pre-shrinking steps.
[0041] The formula of the composition in step (3) is: 22%-25% of modified polyether emulsion, 10%-12% of amino fatty acid emulsion, 10%-12% of modified polysiloxane emulsion, acrylic modified polyurethane polymer The product emulsion is 5%-7%, the rest is water, and the pH value is adjusted to 5-6 with acetic acid.
[0042] The fabric is soaked and rolled once, with a liquid retention rate of 78%, set ...
Embodiment 3
[0045] 105’’ / 40s*40s / 133*76 Satin
[0046] The gray cloth is processed through the following steps in turn:
[0047] (1) Pre-treatment of gray cloth: Singeing → rolling enzyme cold stacking → scouring → bleaching → mercerizing → whitening of gray cloth in sequence; the singeing grade reaches grade 4 and above. The amount of hydrogen peroxide used in bleaching is 3-4g / L.
[0048] (2) Printing: the pre-treated semi-finished products are printed, steamed and washed in sequence;
[0049] (3) Finishing: Composition finishing, calendering, pre-shrinking steps.
[0050] The composition formula in step (3) is: modified polyether emulsion 14-16%, amino fatty acid emulsion 16%-18%, modified polysiloxane emulsion 8%-10%, acrylic modified polyurethane polymer The emulsion is 10%-12%, the rest is water, and the pH value is adjusted to 5-5.5 with acetic acid.
[0051] The fabric is soaked and rolled once, with a liquid retention rate of 70%, set at 150-160°C, and set at a speed of 50m / m...
PUM
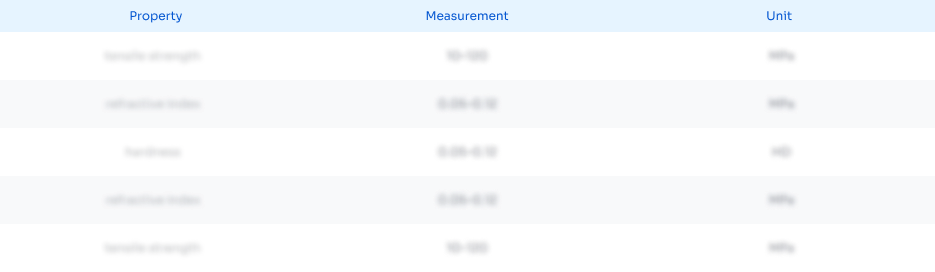
Abstract
Description
Claims
Application Information

- R&D
- Intellectual Property
- Life Sciences
- Materials
- Tech Scout
- Unparalleled Data Quality
- Higher Quality Content
- 60% Fewer Hallucinations
Browse by: Latest US Patents, China's latest patents, Technical Efficacy Thesaurus, Application Domain, Technology Topic, Popular Technical Reports.
© 2025 PatSnap. All rights reserved.Legal|Privacy policy|Modern Slavery Act Transparency Statement|Sitemap|About US| Contact US: help@patsnap.com