Samarium-zinc-iron alloy electroplating liquid and electroplating method thereof
A technology of ferroalloy and electroplating solution, which is applied in the field of samarium-zinc-iron alloy electroplating solution and its electroplating, which can solve the problems of unstable electroplating solution, rough coating, dullness, etc., and achieve high electroplating efficiency, good stability and good corrosion resistance The effect of sex and smoothness
- Summary
- Abstract
- Description
- Claims
- Application Information
AI Technical Summary
Problems solved by technology
Method used
Image
Examples
Embodiment 1
[0020] Embodiment 1: the samarium-zinc-iron alloy electroplating solution of the present embodiment comprises following components:
[0021]
[0022] Use this samarium-zinc-iron alloy plating solution electroplating method as follows:
[0023] Preparation of samarium-zinc-iron alloy electroplating solution: 10 g of potassium citrate, 2 g of ascorbic acid, and 0.05 g of samarium oxide are dissolved in deionized water to form a solution, and 30 g of ferrous sulfate, 10 g of sodium chloride, and 5 g of sodium glycolate are added to the solution , zinc sulfate 80g and stir and dissolve to make a mixed solution, add 0.1g of sodium benzenesulfinate and 1g of alkalized tetraisopropylamine to the mixed solution to dissolve, then add the remaining amount of deionized water to a total volume of 1L, and obtain samarium- Zinc-iron alloy plating solution;
[0024] Adjust the pH of the electroplating solution to 5 with ammonia water, use a carbon electrode as the anode, and the workpiec...
Embodiment 2
[0025] Embodiment 2: the samarium-zinc-iron alloy electroplating solution of the present embodiment comprises following components:
[0026]
[0027] Use this samarium-zinc-iron alloy plating solution electroplating method as follows:
[0028] Preparation of samarium-zinc-iron alloy electroplating solution: 16 g of potassium citrate, 2 g of ascorbic acid, and 0.08 g of samarium oxide are dissolved in deionized water to form a solution, and 30 g of ferrous sulfate, 10 g of sodium chloride, and 8 g of sodium glycolate are added to the solution , zinc sulfate 90g and stir to dissolve to make a mixed solution, add 0.15g of sodium benzenesulfinate and 1.2g of alkalized tetraisopropylamine to the mixed solution, and then add the remaining amount of deionized water to a total volume of 1L to obtain samarium - zinc-iron alloy electroplating solution;
[0029] Adjust the pH of the electroplating solution to 6 with ammonia water, use a carbon electrode as the anode, and the workpiec...
Embodiment 3
[0030] Embodiment 3: the samarium-zinc-iron alloy electroplating solution of the present embodiment comprises following components:
[0031]
[0032]
[0033] Use this samarium-zinc-iron alloy plating solution electroplating method as follows:
[0034] Preparation of samarium-zinc-iron alloy electroplating solution: Dissolve 18g of potassium citrate, 2.6g of ascorbic acid, and 0.12g of samarium oxide in deionized water to form a solution, add 32g of ferrous sulfate, 12g of sodium chloride, and sodium glycolate to the solution 9g, zinc sulfate 95g and stirring and dissolving to make a mixed solution, adding 0.2g of sodium benzenesulfinate and 1.3g of alkalized tetraisopropylamine to the mixed solution to dissolve, then adding the remaining amount of deionized water to a total volume of 1L to obtain Samarium-zinc-iron alloy electroplating solution;
[0035] Adjust the pH of the electroplating solution to 6 with ammonia water, use a carbon electrode as the anode, and the w...
PUM
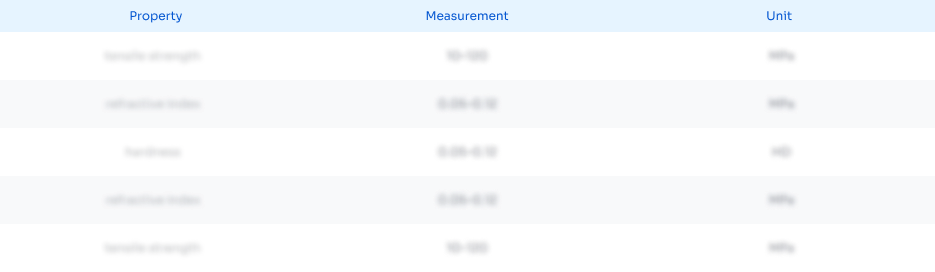
Abstract
Description
Claims
Application Information

- Generate Ideas
- Intellectual Property
- Life Sciences
- Materials
- Tech Scout
- Unparalleled Data Quality
- Higher Quality Content
- 60% Fewer Hallucinations
Browse by: Latest US Patents, China's latest patents, Technical Efficacy Thesaurus, Application Domain, Technology Topic, Popular Technical Reports.
© 2025 PatSnap. All rights reserved.Legal|Privacy policy|Modern Slavery Act Transparency Statement|Sitemap|About US| Contact US: help@patsnap.com