Preparation technology of copper and aluminum combined flat wire
A copper-aluminum compounding and preparation technology, which is applied in the direction of cable/conductor manufacturing, electrical components, circuits, etc., can solve the problems of long production process, low interface bonding strength, and low production efficiency, and achieve industrial production lines and scale The effect of chemical production, high interface bonding strength, and adjustable copper layer thickness
- Summary
- Abstract
- Description
- Claims
- Application Information
AI Technical Summary
Problems solved by technology
Method used
Examples
Embodiment Construction
[0013] For better understanding and implementation, the present invention is described in detail below: a preparation process of copper-aluminum composite flat wire, which is a processing method of bimetallic composite materials. Composite, the volume ratio of the clad copper layer is 30%, the blanking method is: the side length of the billet is 44mm, the rolling speed is 80m / min, the pass rolling is divided into nine passes, flat rolling and vertical rolling cross That is, the first, third, fifth, seventh and ninth passes are flat rolling, the second, fourth, sixth and eighth passes are vertical rolling, the single pass reduction rate of flat rolling is 25%, and the single pass of vertical rolling The reduction rate is 15%, the rough machining of the billet is realized after rolling, and it is beneficial to the subsequent drawing and finishing;
[0014] The next process step is: drawing. The drawing speed is 35m / min, the thickness reduction of the first pass is controlled to...
PUM
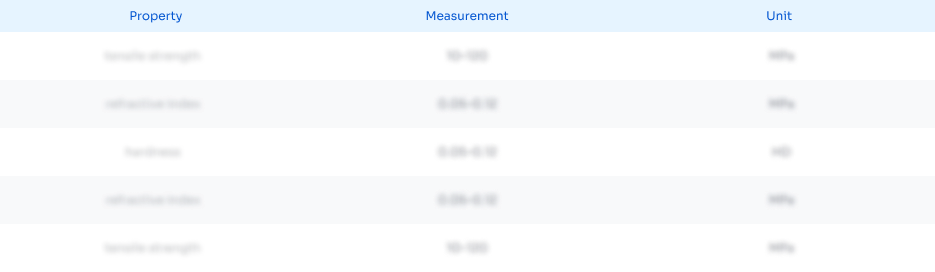
Abstract
Description
Claims
Application Information

- R&D
- Intellectual Property
- Life Sciences
- Materials
- Tech Scout
- Unparalleled Data Quality
- Higher Quality Content
- 60% Fewer Hallucinations
Browse by: Latest US Patents, China's latest patents, Technical Efficacy Thesaurus, Application Domain, Technology Topic, Popular Technical Reports.
© 2025 PatSnap. All rights reserved.Legal|Privacy policy|Modern Slavery Act Transparency Statement|Sitemap|About US| Contact US: help@patsnap.com