Conductive rubber and application thereof
A technology of conductive rubber and rubber, which is applied in the direction of circuits, conductive materials dispersed in non-conductive inorganic materials, electric switches, etc., can solve the problems of inconvenient processing and molding, unfavorable bonding, small specific surface area, etc. Dust resistance, easy adjustment, simple production method
- Summary
- Abstract
- Description
- Claims
- Application Information
AI Technical Summary
Problems solved by technology
Method used
Examples
Embodiment 1
[0025] Use solid silicone rubber KE-950 with a Shore A hardness of 50, add 1% cross-linking agent DCP, and mix it on a two-roller open rubber mixer at room temperature for 10 minutes to produce a 2mm rubber sheet. Standby; take a metal fiber sintered mat made of stainless steel (SUS316L) fibers with a thickness of 0.30mm, a square side length of 12.0cm, and a porosity of 88% by vacuum sintering with a metal fiber diameter of 0.8 microns. The fiber sintered mat is placed in a square cavity with a side length of 12.2 cm. The depth of the square cavity is 0.60mm. Put a 10-gram compound rubber sheet on the stainless steel non-woven fabric, heat vulcanization molding at 165 ° C for 10 minutes, release the mold, and take out the rubber sheet containing the stainless steel non-woven fabric from the mold cavity, which is the metal non-woven fabric. Cloth rubber composite sheet. This sheet was punched into small discs with a diameter of 3.0 mm. This small disc can be used in the key...
Embodiment 2
[0027] The metal fiber sintered felt used in this example is treated with 2% ethanol solution of silane coupling agent KH-550 (dipped or painted), baked at 90°C for 15 minutes, and then placed in a desiccator spare. Other processing is identical with embodiment one.
Embodiment 3
[0029] Take a metal fiber sintered mat made of stainless steel (SUS316L) fibers with a thickness of 0.30mm, a square side length of 12.0cm, and a porosity of 80%, and a metal fiber diameter of 0.8 microns. In a square mold cavity with a side length of 12.2 cm. The depth of the square cavity is 0.30mm. Put a 10-gram freshly mixed liquid silicone rubber (Silopren? LSR2660) on the stainless steel metal fiber sintered felt, heat vulcanization molding at 120°C for 20 minutes, and release the mold. The stainless steel metal fiber sintered felt is contained in the mold cavity. The rubber sheet is a rubber composite sheet containing metal non-woven fabric.
PUM
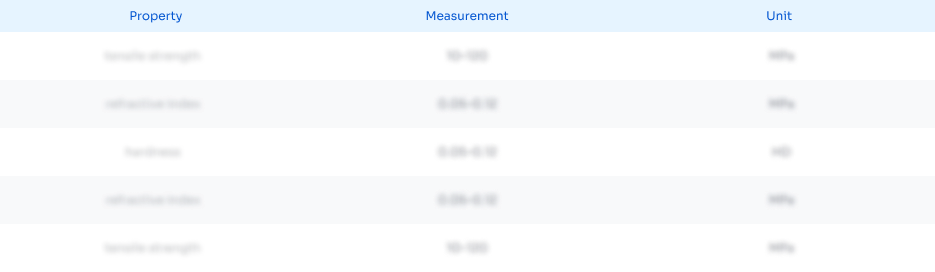
Abstract
Description
Claims
Application Information

- R&D Engineer
- R&D Manager
- IP Professional
- Industry Leading Data Capabilities
- Powerful AI technology
- Patent DNA Extraction
Browse by: Latest US Patents, China's latest patents, Technical Efficacy Thesaurus, Application Domain, Technology Topic, Popular Technical Reports.
© 2024 PatSnap. All rights reserved.Legal|Privacy policy|Modern Slavery Act Transparency Statement|Sitemap|About US| Contact US: help@patsnap.com