Z-pin reinforced composite grid structure and manufacturing method thereof
A technology for reinforcing composite materials and grid structures, which is applied in the field of composite material reinforcement, can solve problems such as strength reduction at joints, and achieve the effects of improving uneven thickness, improving connection strength and fatigue resistance.
- Summary
- Abstract
- Description
- Claims
- Application Information
AI Technical Summary
Problems solved by technology
Method used
Image
Examples
no. 1 example
[0035] The first embodiment: as figure 2 as shown,
[0036] A Z-pin reinforced composite material grid structure of the present invention comprises a transverse bar 1 and a longitudinal bar 2, and a node 3 is formed at the intersection of the transverse bar 1 and the longitudinal bar 2, wherein: the transverse bar 1 and the longitudinal bar 2 adopt "shearing-continuation" in sequence "process, and implant Z-pin4 at the intersection, that is, node 3, to improve the connection strength of the composite grid structure;
[0037] The process of "cutting-continuing laying" is: in each layer of composite material grid structure, only one node of the transverse reinforcement 1 and longitudinal reinforcement 2 is laid, and the other is cut on both sides of the node, so that the thickness of each node is the same as that of the transverse reinforcement 1 , The thickness of the remaining parts on the longitudinal rib 2 is consistent.
[0038] In the embodiment, the implantation direct...
no. 2 example
[0051] The second embodiment: as image 3 as shown,
[0052] In the embodiment, the Z-pin4 is also implanted in the parts of the transverse rib 1 and the longitudinal rib 2 close to the node 3 .
[0053] The parts not described are the same as the first embodiment.
[0054] Compared with the first embodiment, this embodiment implants more Z-pin4, the range is wider, and the connection strength is higher.
no. 3 example
[0055] The third embodiment: as Figure 4 as shown,
[0056] In the embodiment, the angle part formed by the node 3 and the transverse rib 1 and the longitudinal rib 2 is paved with a reinforcing plate 5 made of the same material as the transverse rib 1 and the longitudinal rib 2 .
[0057] The parts not mentioned are the same as the second embodiment.
[0058]Compared with the second embodiment, this embodiment is compared with the first embodiment, and this embodiment adds a reinforcing plate 5 to further enhance the connection strength at the nodes.
PUM
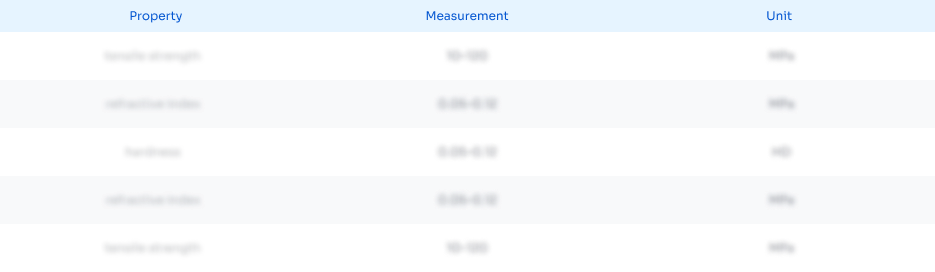
Abstract
Description
Claims
Application Information

- Generate Ideas
- Intellectual Property
- Life Sciences
- Materials
- Tech Scout
- Unparalleled Data Quality
- Higher Quality Content
- 60% Fewer Hallucinations
Browse by: Latest US Patents, China's latest patents, Technical Efficacy Thesaurus, Application Domain, Technology Topic, Popular Technical Reports.
© 2025 PatSnap. All rights reserved.Legal|Privacy policy|Modern Slavery Act Transparency Statement|Sitemap|About US| Contact US: help@patsnap.com