Comprehensive treatment method for red mud and copper slag
A comprehensive treatment and red mud technology, applied in the direction of process efficiency improvement, etc., can solve the problems of fayalite reduction in copper slag, fine iron particles cannot be aggregated, and low pellet strength, so as to achieve sustainable development and clean Production, high strength effect
- Summary
- Abstract
- Description
- Claims
- Application Information
AI Technical Summary
Problems solved by technology
Method used
Image
Examples
Embodiment 1
[0030] A copper smelting slag, the composition of chemical analysis is: TFe40.12%, Na 2 O0.46%; red mud produced by a certain Bayer method, its composition is: TFe35.92%, Na 2 O6.89%. After copper slag and red mud are mixed at a mass ratio of 1:2, TFe37.32% in the mixed raw material of red mud and copper slag, Na 2 O4.75%.
[0031] After the mixed raw materials are moistened and milled for 3 minutes, 35% reducing agent (lignite with 50% carbon content) is added to make pellets, and the pellets are dry and the wet ball strength is >8 times. The pellets are dried and then roasted at a roasting temperature of 1250°C. The metallized pellets obtained have a metallization rate of 90.2%. The pellets are subjected to grinding and magnetic separation to finally obtain metallic iron powder with a purity of 92.12% and an iron recovery rate of 85%. .
Embodiment 2
[0033] A copper smelting slag, its composition is: TFe40.12%, Na 2 O0.46%; a Bayer red mud, its composition is: TFe32.03%, Na 2 O7.9%. After mixing copper slag and red mud at a mass ratio of 1:1, the mixed raw material of red mud and copper slag contains TFe36.08%, Na 2 O4.18%.
[0034] After milling the mixed raw materials for 4 minutes, add 25% reducing agent (semi-coke with 70% carbon content) to make pellets, the pellets are dry and the wet ball strength is >9 times. The pellets were dried and then roasted at a roasting temperature of 1250°C. The metallization rate of the obtained metallized pellets was 90.88%. The pellets were subjected to grinding and magnetic separation to finally obtain metallic iron powder with a purity of 91.05% and an iron recovery rate of 87%. .
Embodiment 3
[0036] A copper smelting slag, its composition is: TFe39.21%, Na 2 O0.41%; a Bayer red mud, its composition is: TFe33.51%, Na 2 O7.20%. After copper slag and red mud are mixed at a mass ratio of 1:1.2, the mixed raw material of red mud and copper slag contains TFe36.10%, Na 2 O4.11%.
[0037] After the mixed raw materials are wetted and ground for 4 minutes, 17% reducing agent (anthracite with 80% carbon content) is added to make pellets, and the pellets are dry and the wet ball strength is more than 10 times. The pellets were dried and then roasted at a roasting temperature of 1280°C. The metallized pellets obtained had a metallization rate of 92.32%. The pellets were subjected to grinding and magnetic separation to finally obtain metal iron powder with a purity of 92.55% and an iron recovery rate of 88%. .
PUM
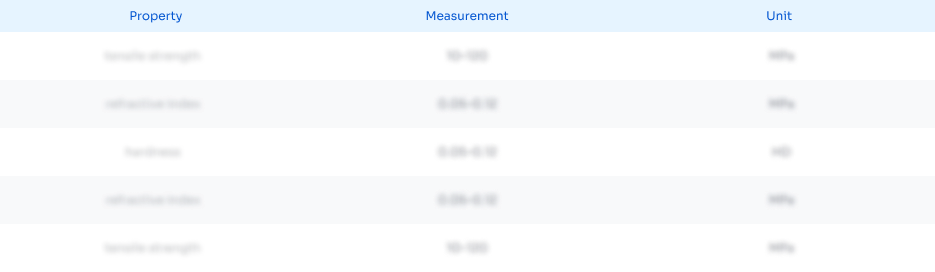
Abstract
Description
Claims
Application Information

- R&D
- Intellectual Property
- Life Sciences
- Materials
- Tech Scout
- Unparalleled Data Quality
- Higher Quality Content
- 60% Fewer Hallucinations
Browse by: Latest US Patents, China's latest patents, Technical Efficacy Thesaurus, Application Domain, Technology Topic, Popular Technical Reports.
© 2025 PatSnap. All rights reserved.Legal|Privacy policy|Modern Slavery Act Transparency Statement|Sitemap|About US| Contact US: help@patsnap.com