High-entropy alloy for sewage degradation and preparing method thereof
A high-entropy alloy and sewage technology, applied in the field of high-entropy alloy, can solve the problems of low efficiency and limit the application of high-entropy alloy, and achieve the effects of improving efficiency, strong operability and low preparation cost
- Summary
- Abstract
- Description
- Claims
- Application Information
AI Technical Summary
Problems solved by technology
Method used
Image
Examples
preparation example Construction
[0029] The preparation method provided by the invention has the following steps:
[0030]Dosing according to any one of the high-entropy alloy components in the specific examples, directly using the method of (ball milling) mechanical alloying, wherein the ball milling is carried out under the protection of argon, the high-entropy alloy for degrading sewage can be obtained. alloy. Among them, the purity of metal element raw material powder is higher than 99%, and the particle size is 200-325 mesh. The ball-to-material ratio in the ball milling process was 15:1, n-heptane was used as the process control agent, and the ball milling speed was 300 rpm. The relevant operations of the ball milling tank were all carried out in a glove box, and the glove box was an atmosphere of argon at atmospheric pressure.
[0031] The practical effects of the present invention will be further described below in conjunction with specific examples.
Embodiment 1
[0033] Preparation of high entropy alloy powder Co 20 Ti 20 Cr 20 al 20 Zn 20
[0034] The metal element powder raw materials (Cr, Co, Ti, Zn, Al) with a purity greater than 99% are compounded according to the equiatomic ratio, and then put into the ball mill tank together with the ball mill medium, and 1%wt process control agent is added. The ball mill tank and ball mill medium are made of stainless steel, the process control agent is n-heptane, and the ball-to-material ratio is 15:1.
[0035] An all-round planetary ball mill is adopted, and the ball milling speed is 300rpm. The powder was taken for observation every 5 hours, and each time the can was opened to take the powder, it was carried out in a glove box, and the glove box was an argon environment at an atmospheric pressure.
[0036] Generally, Co can be obtained by ball milling for about 60 hours. 20 Ti 20 Cr 20 al 20 Zn 20 High-entropy alloy powder, the powder particle size is generally 0.6-10μm. Depend o...
Embodiment 2
[0040] Preparation of high entropy alloy powder Co 20 Ni 20 Ti 20 al 20 Zn 20
[0041] The metal element powder raw materials (Co, Ni, Ti, Zn, Al) with a purity greater than 99% are compounded according to the equiatomic ratio, and then put into the ball mill tank together with the ball mill medium, and 1%wt process control agent is added. The ball mill tank and ball mill medium are made of stainless steel, the process control agent is n-heptane, and the ball-to-material ratio is 15:1.
[0042] An all-round planetary ball mill is adopted, and the ball milling speed is 300rpm. The powder was taken for observation every 5 hours, and each time the can was opened to take the powder, it was carried out in a glove box, and the glove box was an argon environment at an atmospheric pressure.
[0043] Generally, Co can be obtained by ball milling for about 90 hours. 20 Ni 20 Ti 20 al 20 Zn 20 High-entropy alloy powder, the powder particle size is generally 0.6-10μm. Depend o...
PUM
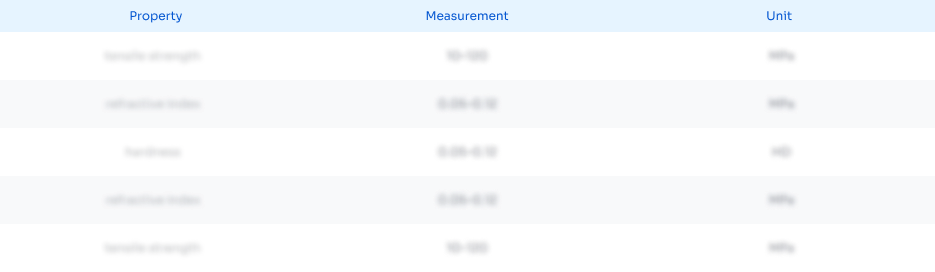
Abstract
Description
Claims
Application Information

- Generate Ideas
- Intellectual Property
- Life Sciences
- Materials
- Tech Scout
- Unparalleled Data Quality
- Higher Quality Content
- 60% Fewer Hallucinations
Browse by: Latest US Patents, China's latest patents, Technical Efficacy Thesaurus, Application Domain, Technology Topic, Popular Technical Reports.
© 2025 PatSnap. All rights reserved.Legal|Privacy policy|Modern Slavery Act Transparency Statement|Sitemap|About US| Contact US: help@patsnap.com