Manganese processing rotary kiln with gas furnace supplying heat
A technology of rotary kiln and gas furnace, applied in the field of rotary kiln, can solve the problems of low thermal efficiency, small heat transfer area between materials and kiln body, etc., and achieve the effects of improving thermal efficiency, promoting material turning and relieving environmental protection pressure
- Summary
- Abstract
- Description
- Claims
- Application Information
AI Technical Summary
Problems solved by technology
Method used
Image
Examples
Embodiment Construction
[0021] Now in conjunction with accompanying drawing, the present invention is described in further detail.
[0022] Such as figure 1 and figure 2 The manganese processing rotary kiln heated by the gas furnace shown in the figure includes the rotary kiln 1, which is arranged obliquely, and has a built-in burner 6, which is connected to the air control valve 19 and the gas control valve 20; the high end of the rotary kiln is equipped with an air lock 11 feeding, and connect the cyclone dust collector 8 through the wing segment 15 and the air pipe 17, the cyclone dust collector 8 is connected to the induced draft fan A, the exhaust port of the induced draft fan A is connected to the bag filter 10, and the bottom of the cyclone dust collector 8 is connected to the air locker, A dust collection bucket 23 is arranged below the air locker; fins 14 are arranged inside the fin section 15, a cover cylinder 16 is provided outside the fin section 15, and a sleeve-type air heat exchanger...
PUM
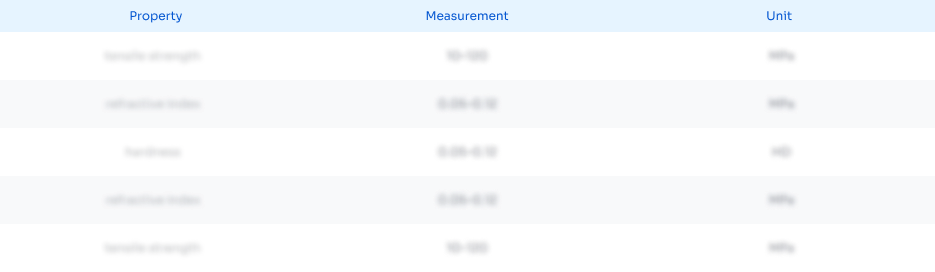
Abstract
Description
Claims
Application Information

- Generate Ideas
- Intellectual Property
- Life Sciences
- Materials
- Tech Scout
- Unparalleled Data Quality
- Higher Quality Content
- 60% Fewer Hallucinations
Browse by: Latest US Patents, China's latest patents, Technical Efficacy Thesaurus, Application Domain, Technology Topic, Popular Technical Reports.
© 2025 PatSnap. All rights reserved.Legal|Privacy policy|Modern Slavery Act Transparency Statement|Sitemap|About US| Contact US: help@patsnap.com