Surface molecular imprinting composite photocatalytic material as well as preparation method and application thereof
A technology of surface molecular imprinting and composite photocatalysis, applied in chemical instruments and methods, organic compound/hydride/coordination complex catalysts, physical/chemical process catalysts, etc., can solve the problem of long degradation time and inability to selectively degrade a single To achieve high purity, enhance recycling performance, and improve utilization rate
- Summary
- Abstract
- Description
- Claims
- Application Information
AI Technical Summary
Problems solved by technology
Method used
Image
Examples
Embodiment 1
[0032] Step 1. Preparation of g-C 3 N 4 Photocatalyst: Put 5g of purchased melamine into a crucible, place it in a muffle furnace, and calcine it in an air atmosphere, raise the temperature to 500°C at a heating rate of 4°C / min, and keep it at a constant temperature for 2 hours. Continue to heat up to 520°C, keep at constant temperature for 2 hours, and cool down to room temperature naturally to obtain g-C 3 N 4 Photocatalyst; save for future use.
[0033] Step 2, preparation of Fe by hydrothermal deposition technology 3 o 4 / g -C 3 N 4 Composite material: weigh 2.2gg-C 3 N 4 Disperse in 600ml of ethanol / water solution with a volume ratio of 1:2 and sonicate for 5 hours to make g-C 3 N 4 suspension; the 2mmolFeCl 3 ·6H 2 O and 1 mmol FeCl 2 4H 2 O each dissolved in 20ml of distilled water and added to the above g-C 3 N 4 suspension to obtain a mixed solution. The above mixture was stirred at 80°C for 30 min, and then 10 ml of ammonia water was quickly injected...
Embodiment 2
[0037] Step 1. Preparation of g-C 3 N 4 Photocatalyst: Put 5 g of purchased melamine into a crucible, place it in a muffle furnace, and calcine it in an air atmosphere. Raise the temperature to 500°C at a heating rate of 2.3°C / min, and keep it at a constant temperature for 2 hours. The heating rate continued to rise to 520°C, and kept at a constant temperature for 2 hours, and then cooled to room temperature naturally to obtain g-C 3 N 4 Photocatalyst; save for future use.
[0038] Step 2, preparation of Fe by hydrothermal deposition technology 3 o 4 / g -C 3 N 4 Composite material: weigh 2.2gg-C 3 N 4 Disperse in 600ml of ethanol / water solution with a volume ratio of 1:2 and sonicate for 5 hours to make g-C 3 N 4 suspension; the 2mmolFeCl 3 ·6H 2 O and 1 mmol FeCl 2 4H 2 O each dissolved in 20ml of distilled water and added to the above g-C 3 N 4 suspension to obtain a mixed solution. The above mixture was stirred at 80°C for 30 min, and then 10 ml of ammonia ...
Embodiment 3
[0042] Step 1. Preparation of g-C 3 N 4 Photocatalyst: Put 5 g of purchased melamine into a crucible, place it in a muffle furnace, and calcine it in an air atmosphere, raise the temperature to 500 °C at a heating rate of 4 °C / min, and keep it at a constant temperature for 2 hours. The heating rate continued to rise to 520°C, and kept at a constant temperature for 2 hours, and then cooled to room temperature naturally to obtain g-C 3 N 4 Photocatalyst; save for future use.
[0043] Step 2, preparation of Fe by hydrothermal deposition technology 3 o 4 / g -C 3 N 4 Composite material: weigh 2.2gg-C 3 N 4 Disperse in 600ml of ethanol / water solution with a volume ratio of 1:2 and sonicate for 5 hours to make g-C 3 N 4 suspension; the 2mmolFeCl 3 ·6H 2 O and 1 mmol FeCl 2 4H 2 O each dissolved in 20ml of distilled water and added to the above g-C 3 N 4 suspension to obtain a mixed solution. The above mixture was stirred at 80°C for 30 min, and then 10 ml of ammonia ...
PUM
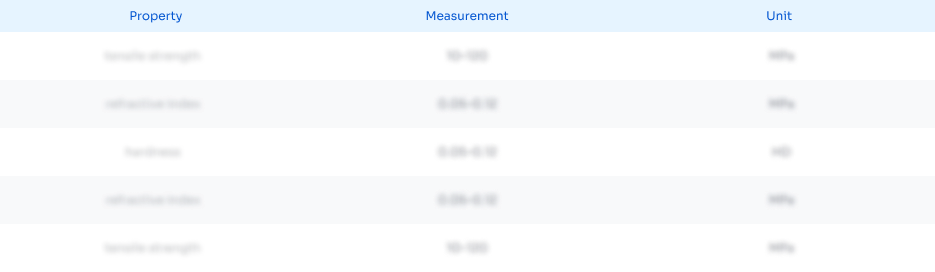
Abstract
Description
Claims
Application Information

- R&D
- Intellectual Property
- Life Sciences
- Materials
- Tech Scout
- Unparalleled Data Quality
- Higher Quality Content
- 60% Fewer Hallucinations
Browse by: Latest US Patents, China's latest patents, Technical Efficacy Thesaurus, Application Domain, Technology Topic, Popular Technical Reports.
© 2025 PatSnap. All rights reserved.Legal|Privacy policy|Modern Slavery Act Transparency Statement|Sitemap|About US| Contact US: help@patsnap.com