Preparation method of corrosion resistant coating layer on surface of magnesium alloy component
A corrosion-resistant coating, magnesium alloy technology, applied in heating inorganic powder coating, nanotechnology and other directions, can solve the problems of easy corrosion, limited application scope, phase transformation of magnesium alloys, etc., to improve corrosion resistance and improve technology Indicators, the effect of strengthening the protective effect
- Summary
- Abstract
- Description
- Claims
- Application Information
AI Technical Summary
Problems solved by technology
Method used
Image
Examples
Embodiment 1
[0026] ① Grooving plan Groove the magnesium alloy substrate. The grooves should be evenly distributed on the surface of the substrate and there is no interval between the grooves. V-shaped grooves are used. The groove width is 2.67mm, the groove depth is 5mm, and the included angle is 30°. Grit blast and clean with acetone.
[0027] ②Set the spraying process parameters:
[0028] Powder feeding gas: nitrogen; gas temperature: 500°C; spraying distance: 30mm; gas pressure: 3.5MPa; gas flow rate: 70m3 / hr; powder feeding volume: 2.8m3 / hr.
[0029] ③The magnesium alloy substrate processed in step ① is sprayed, such as figure 1 As shown, the magnesium alloy component 1 is fixed, and the spray gun 2 sprays it in a straight line.
[0030] ④ Use polyvinyl chloride to seal the coating in step ③. The thickness is 100 μm, and it is taken out after being heated in a drying oven at 170° C. for 60 minutes.
[0031] ⑤ combination figure 2 As shown, the prepared coatings were subjected to...
Embodiment 2
[0034] ① Grooving plan Groove the magnesium alloy substrate. The grooves should be evenly distributed on the surface of the substrate and there is no interval between the grooves. V-shaped grooves are used. The groove width is 2.67mm, the groove depth is 5mm, and the included angle is 30°. Grit blast and clean with acetone.
[0035] ②Set the spraying process parameters:
[0036] Powder feeding gas: nitrogen; gas temperature: 550°C; spraying distance: 30mm; gas pressure: 4.0MPa; gas flow rate: 65m3 / hr; powder feeding volume: 3.0m3 / hr.
[0037] ③The magnesium alloy substrate treated in step ① is sprayed, the magnesium alloy component is fixed, and the spray gun is sprayed on it in a straight line.
[0038] ④ Use polyvinyl chloride to seal the coating in step ③. The thickness is 100 μm, and it is taken out after being heated in a drying oven at 170° C. for 60 minutes.
[0039] ⑤ combination image 3 As shown, the prepared coatings were subjected to salt spray test and microst...
Embodiment 3
[0042] ① Grooving plan Groove the magnesium alloy substrate. The grooves should be evenly distributed on the surface of the substrate and there is no interval between the grooves. V-shaped grooves are used. The groove width is 2.67mm, the groove depth is 5mm, and the included angle is 30°. Grit blast and clean with acetone.
[0043] ②Set the spraying process parameters:
[0044] Powder feeding gas: nitrogen; gas temperature: 600°C; spraying distance: 30mm; gas pressure: 4.5MPa; gas flow rate: 60m3 / hr; powder feeding volume: 3.5m3 / hr.
[0045] ③The magnesium alloy substrate treated in step ① is sprayed, the magnesium alloy component is fixed, and the spray gun is sprayed on it in a straight line.
[0046] ④ Use polyvinyl chloride to seal the coating in step ③. The thickness is 100 μm, and it is taken out after being heated in a drying oven at 170° C. for 60 minutes.
[0047] ⑤ combination Figure 4 As shown, the prepared coatings were subjected to salt spray test and micros...
PUM
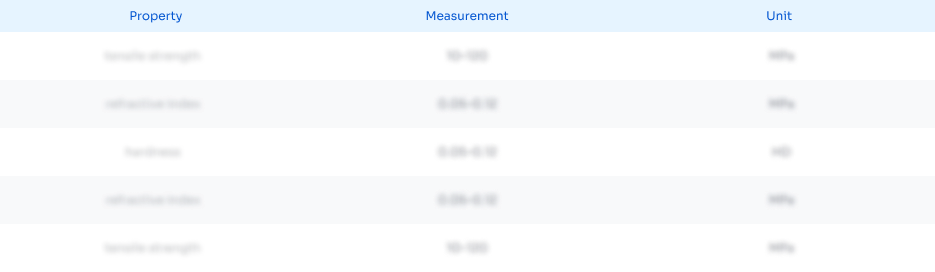
Abstract
Description
Claims
Application Information

- R&D
- Intellectual Property
- Life Sciences
- Materials
- Tech Scout
- Unparalleled Data Quality
- Higher Quality Content
- 60% Fewer Hallucinations
Browse by: Latest US Patents, China's latest patents, Technical Efficacy Thesaurus, Application Domain, Technology Topic, Popular Technical Reports.
© 2025 PatSnap. All rights reserved.Legal|Privacy policy|Modern Slavery Act Transparency Statement|Sitemap|About US| Contact US: help@patsnap.com