Photoelectric integrated processing device and photoelectric integrated processing technique for waste gases generated by spraying paint
A technology for treating device and waste gas, which is applied in combination devices, chemical instruments and methods, and dispersed particle separation, etc., can solve problems such as troublesome activated carbon treatment, and achieve the effect of saving space, reducing equipment operating costs, and reducing usage.
- Summary
- Abstract
- Description
- Claims
- Application Information
AI Technical Summary
Problems solved by technology
Method used
Image
Examples
Embodiment 1
[0069] In this embodiment, the spray unit 3 of the exhaust gas treatment device has a filler height of 2080mm above the liquid level and a thickness of 960mm. The φ50 Taylor wreath is used as the filler, the liquid level is about 310mm, and the spray liquid dosage is 60m3 / h. There are two rows in total. Ten spray nozzles 2 are arranged on the blind plate 1 of the circulating liquid pipe flange, and the spray nozzles 2 are A3 type. The spray pipe 7 circulating liquid tank 8 and the vertical circulating pump 6 are connected by PP pipes, the main pipe diameter is 100mm, the straight pipe diameter is 65mm, the middle is adjusted and switched by the ball valve and the check valve, and the circulating liquid tank 8 is at the outlet Set Y-type filter and grease trap to remove paint residue, etc. The height of the filler of the demister unit 4 above the liquid level is 2380mm, the thickness is 400mm, and the φ25 Pall ring is used as the filler. The size of a single module of the plasm...
Embodiment 2
[0074] In this device, the spray liquid dosage is 40m3 / h, the spray pipe 7 has a diameter of 65mm, the branch pipe has a diameter of 50mm, and the bottom liquid level is 180mm. The design of the rest of the device is the same as in Example 1. The source of the exhaust gas is the painting exhaust gas of a mold processing factory.
[0075] In this embodiment, the design air volume is 20000m3 / h, the air inlet interface size of the equipment is 1840×2280mm, the design exhaust gas flow rate is 1.3m / s, and the main components of the exhaust gas are methyl isobutyl ketone, diisobutyl ketone, and methyl ethyl ketone. Wait, the temperature is normal temperature. The content of pollutants in and out of exhaust gas is as follows:
[0076] Table 2 Concentration of pollutants in the exhaust gas in and out of Example 2
[0077]
Embodiment 3
[0079] The design of this device is the same as that of Example 1, and the source of exhaust gas is mold coating.
[0080] In this embodiment, the design air volume is 30000m3 / h, the air inlet interface size of the equipment is 1840×2280mm, the design exhaust gas flow rate is 2m / s, the main components of the exhaust gas are toluene, xylene, ethyl acetate, etc., and the temperature is normal temperature. The content of pollutants in and out of exhaust gas is as follows:
[0081] Table 3 Concentrations of pollutants in the exhaust gas in and out of Example 3
[0082] .
PUM
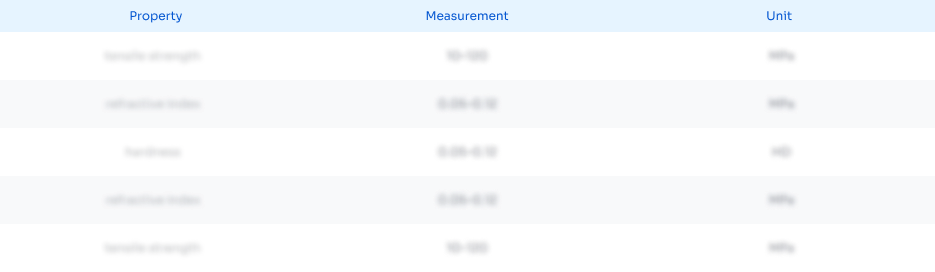
Abstract
Description
Claims
Application Information

- R&D
- Intellectual Property
- Life Sciences
- Materials
- Tech Scout
- Unparalleled Data Quality
- Higher Quality Content
- 60% Fewer Hallucinations
Browse by: Latest US Patents, China's latest patents, Technical Efficacy Thesaurus, Application Domain, Technology Topic, Popular Technical Reports.
© 2025 PatSnap. All rights reserved.Legal|Privacy policy|Modern Slavery Act Transparency Statement|Sitemap|About US| Contact US: help@patsnap.com