Sensorless prediction torque control system and method for asynchronous motor
A technology for asynchronous motors and torque prediction, applied in control systems, vector control systems, motor generator control, etc., can solve problems such as insufficient control accuracy
- Summary
- Abstract
- Description
- Claims
- Application Information
AI Technical Summary
Problems solved by technology
Method used
Image
Examples
Embodiment 1
[0098] Such as Figure 1-2 As shown, a sensorless predictive torque control system for an asynchronous motor according to the present invention includes a first PI controller 1, a model reference adaptive observer 2, and an optimization module 3; the first PI controller 1, and an optimization module 3 The model reference adaptive observer 2 is connected to each other in pairs; the asynchronous motor sensorless predictive torque control system is connected to the inverter 5 when used, and the inverter 5 is connected to the asynchronous motor 6;
[0099] The model refers to an adaptive observer 2 for the stator voltage v obtained at the output of the inverter 5 s and stator current i s Calculate the observed speed by formula 1-4 The model reference adaptive observer 2 includes a reference module 2-1, an adjustable module 2-2, a rotor flux deviation calculation module 2-3 and a second PI controller 2-4, a reference module 2-1, an adjustable module 2-2 are respectively connect...
Embodiment 2
[0133] Such as figure 1 , 3 Shown, it differs from Embodiment 1 in that:
[0134] The sliding mode compensation module 2-1-2 is replaced by the sliding mode compensation optimization module 2-1-2', and the third PI controller 2-1-3 in the sliding mode compensation optimization module 2-1-2' utilizes Self-adjustable proportional gain of K kp and integral gain K ki The sliding mode gain K is calculated by formula 5, and the sliding mode gain K is used for sliding mode compensation, and formula 1 is corrected to formula 1", the above formula is as follows,
[0135] d ψ ^ s d t = - R s σL s ψ ^ s + ...
PUM
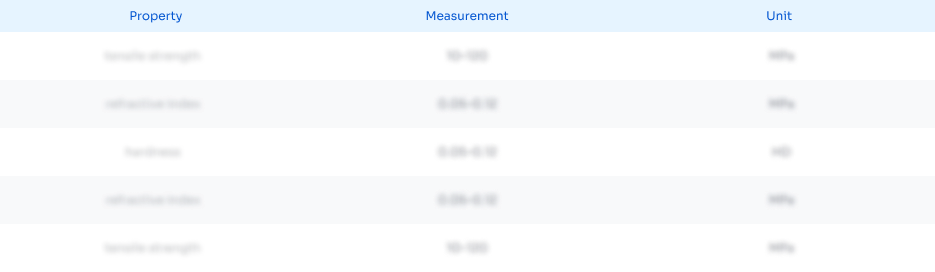
Abstract
Description
Claims
Application Information

- R&D
- Intellectual Property
- Life Sciences
- Materials
- Tech Scout
- Unparalleled Data Quality
- Higher Quality Content
- 60% Fewer Hallucinations
Browse by: Latest US Patents, China's latest patents, Technical Efficacy Thesaurus, Application Domain, Technology Topic, Popular Technical Reports.
© 2025 PatSnap. All rights reserved.Legal|Privacy policy|Modern Slavery Act Transparency Statement|Sitemap|About US| Contact US: help@patsnap.com