Method for removing magnesium in sulfuric acid leaching process of rhodochrosite
A rhodochrosite and high-acid leaching technology, which is applied in the direction of improving process efficiency, etc., can solve the problems of large excess coefficient of fluoride salt, shortened service life of cathode plate, increased fluoride ion content, etc., and achieves shortened leaching time and high leaching temperature. High, the effect of high residual acid concentration
- Summary
- Abstract
- Description
- Claims
- Application Information
AI Technical Summary
Problems solved by technology
Method used
Examples
Embodiment 1
[0029] A method for removing magnesium in the sulfuric acid leaching process of rhodochrosite, comprising the steps:
[0030] (1) Add electrolytic manganese into the leaching tank and return to the anolyte 300ml. When the stirring paddle can be stirred, start to add the slurry containing rhodochrosite powder 100g, and start stirring; after adding the rhodochrosite powder slurry, add concentrated sulfuric acid. The amount of sulfuric acid added is based on controlling the concentration of residual acid at the end of leaching to 40g / L. After adding concentrated sulfuric acid, the electrolytic manganese is finally filled and returned to the anolyte to 800ml. The aforementioned electrolytic manganese returns to MnSO in the anolyte 4 Concentration 38.9g / l, MgSO 4 Concentration 170.2g / l, (NH4 ) 2 SO 4 Concentration 78.2g / l.
[0031] (2) After fully leaching for 3.5 hours, add liquid ammonia to neutralize, so that the solution system is neutral, and the pH value is controlled at ...
Embodiment 2
[0035] A method for removing magnesium in the sulfuric acid leaching process of rhodochrosite, comprising the steps:
[0036] (1) Add electrolytic manganese into the leaching tank and return to the anolyte 300ml. When the stirring paddle can be stirred, start to add the slurry containing rhodochrosite powder 100g, and start stirring; after adding the rhodochrosite powder slurry, add concentrated sulfuric acid. The amount of sulfuric acid added is based on the residual acid concentration at the end of leaching at 25g / L. After adding concentrated sulfuric acid, the electrolytic manganese is finally filled and returned to the anolyte to 800ml. The aforementioned electrolytic manganese returns to MnSO in the anolyte 4 Concentration 38.9g / l, MgSO 4 Concentration 170.2g / l, (NH 4 ) 2 SO 4 Concentration 78.2g / l.
[0037] (2) After fully leaching for 4.0 hours, add liquid ammonia to neutralize, so that the solution system is neutral, and the pH value is controlled at 6-7; adding l...
PUM
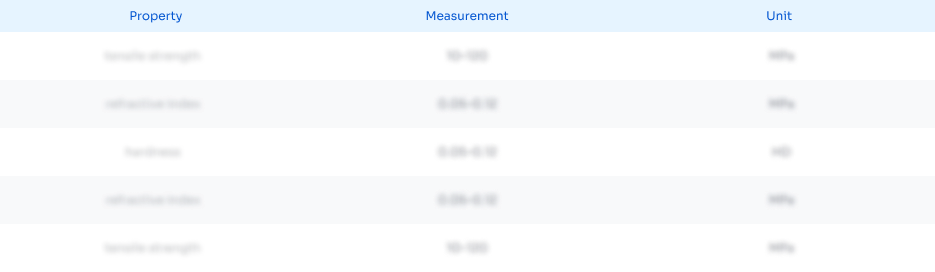
Abstract
Description
Claims
Application Information

- Generate Ideas
- Intellectual Property
- Life Sciences
- Materials
- Tech Scout
- Unparalleled Data Quality
- Higher Quality Content
- 60% Fewer Hallucinations
Browse by: Latest US Patents, China's latest patents, Technical Efficacy Thesaurus, Application Domain, Technology Topic, Popular Technical Reports.
© 2025 PatSnap. All rights reserved.Legal|Privacy policy|Modern Slavery Act Transparency Statement|Sitemap|About US| Contact US: help@patsnap.com