A modular rov control system
A control system and modular technology, applied in the direction of three-dimensional position/channel control, etc., can solve the problems of communication network paralysis, system reliability and stability reduction, limited hardware board resources, etc., and achieve strong error correction and independent judgment capabilities , Guarantee the effect of safe work or recycling, high intelligence and fault tolerance
- Summary
- Abstract
- Description
- Claims
- Application Information
AI Technical Summary
Problems solved by technology
Method used
Image
Examples
Embodiment 1
[0035] Implementation 1: If figure 1 As shown, the modular ROV control system includes a remote communication system, a motion planning processor, an attitude detection system, a robotic arm motion control system, a thruster control system, a video acquisition system, an underwater lighting control system, a hydraulic control system, an underwater surveillance system. The remote communication system is used to receive commands sent by the surface controller, and at the same time collect data from various sub-systems underwater for upload. The motion planning processor makes a comprehensive judgment based on the current state of the system and the commands sent by the water surface controller, and reasonably plans the motion control of the ROV. The position and attitude detection system is used to detect the attitude and depth of the ROV body. Information such as movement speed and underwater position. The robot arm motion control system controls the underwater master-slave ...
Embodiment 2
[0036] Implementation 2: If figure 2 As shown, according to the requirements of the operational ROV control system, the structure of the motion planning processor is divided into four parts: monitoring layer, control layer, execution layer, and data management layer. The main tasks are: data communication with various sensors, thrusters, manipulators and surface equipment; sensor data processing, dynamic positioning control and operation control.
Embodiment 3
[0037] Implementation 3: If image 3 As shown, the attitude detection system adopts dual CPU control mode. The ARM processor is used to collect the data information of the depth gauge, altimeter and ultra-short baseline, and the data collection speed is not high. At the same time, the processor is also responsible for sending data to the control system network and receiving commands. In addition, it also has the functions of important parameter setting and important data storage. The DSP processor has the function of high-speed calculation. Using it to collect and fuse the data of the attitude acquisition system and the Doppler current meter, the attitude of the ROV in three-dimensional space and the relative position underwater can be calculated in real time.
PUM
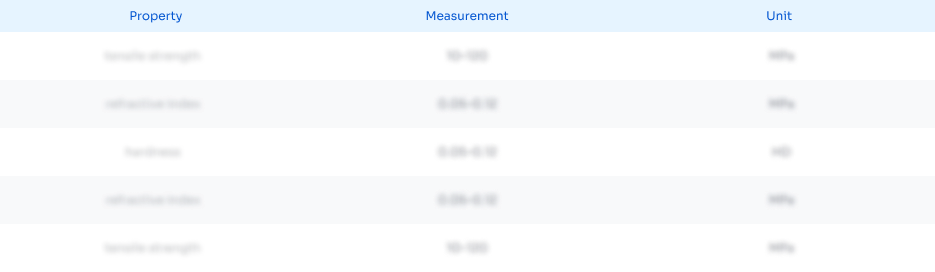
Abstract
Description
Claims
Application Information

- Generate Ideas
- Intellectual Property
- Life Sciences
- Materials
- Tech Scout
- Unparalleled Data Quality
- Higher Quality Content
- 60% Fewer Hallucinations
Browse by: Latest US Patents, China's latest patents, Technical Efficacy Thesaurus, Application Domain, Technology Topic, Popular Technical Reports.
© 2025 PatSnap. All rights reserved.Legal|Privacy policy|Modern Slavery Act Transparency Statement|Sitemap|About US| Contact US: help@patsnap.com