On-site external vulcanization processing method of hydrogenation catalysts
A hydrogenation catalyst and sulfidation treatment technology, which is applied in catalyst activation/preparation, chemical instruments and methods, physical/chemical process catalysts, etc. Hydrogen selectivity, reduction of olefin saturation, high desulfurization rate
- Summary
- Abstract
- Description
- Claims
- Application Information
AI Technical Summary
Problems solved by technology
Method used
Image
Examples
Embodiment 1
[0038] Example 1: Preparation of catalyst carrier
[0039] Weigh 100g of aluminum hydroxide powder, add 3g of sesame powder, mix well, use 100ml of 2wt% nitric acid aqueous solution to acidify, after fully kneading into a gel, extrude it into a cylindrical strip with a diameter of 1.6mm on an extruder. And bake in an oven at 100-120°C for 8-12 hours to obtain a dry carrier. Then, it was placed in a muffle furnace and calcined in an air atmosphere at a temperature of 550° C. for 4 hours to obtain a catalyst carrier A.
Embodiment 2
[0040] Example 2: Loading and curing of molybdenum
[0041] Weigh 2.65g of ammonium paramolybdate, add 14ml of distilled water, stir and dissolve to prepare an immersion solution. 20 g of the carrier A prepared in Example 1 was impregnated with this solution and dried in an oven at 120° C. for 6 hours to obtain a Mo-supported catalyst. The dried catalyst is placed in a tube furnace. The furnace is supplied with a sulfur-containing gaseous mixture of hydrogen sulfide and nitrogen with partial pressures of 0.1 atm and 0.9 atm, respectively, and the temperature is increased to 400°C at a temperature rise rate of 40°C / h , Maintain the temperature for 3 hours to sulfide the catalyst to obtain a catalyst B supporting molybdenum.
Embodiment 3
[0042] Example 3: Cobalt loading and presulfurization
[0043] Weigh cobalt nitrate Co (NO 3 ) 2 ·6H 2 2.4 g of O (analytical purity) was dissolved in 14 ml of distilled water, the Mo-loaded catalyst B prepared in Example 2 was impregnated with the solution, and dried in an oven at 120° C. for 6 hours. The dried catalyst is placed in a tube furnace. The furnace is supplied with a sulfur-containing gaseous mixture of hydrogen sulfide and nitrogen with partial pressures of 0.1 atm and 0.9 atm, respectively, and the temperature is increased to 400°C at a temperature rise rate of 40°C / h , Keep the temperature for 3 hours to sulfide the catalyst to obtain a catalyst C loaded with molybdenum and cobalt. MoO of the catalyst 3 The loading of CoO is 9.28% and 2.72%.
PUM
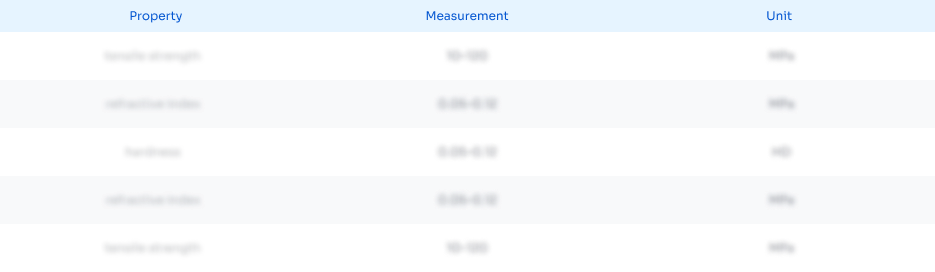
Abstract
Description
Claims
Application Information

- R&D
- Intellectual Property
- Life Sciences
- Materials
- Tech Scout
- Unparalleled Data Quality
- Higher Quality Content
- 60% Fewer Hallucinations
Browse by: Latest US Patents, China's latest patents, Technical Efficacy Thesaurus, Application Domain, Technology Topic, Popular Technical Reports.
© 2025 PatSnap. All rights reserved.Legal|Privacy policy|Modern Slavery Act Transparency Statement|Sitemap|About US| Contact US: help@patsnap.com